引言
TC11合金是典型的(α+β)双相钛合金,名义成分为Ti-6.5Al-3.5Mo-1.5Zr-0.3Si,是我国应用最为广泛、技术成熟稳定的钛合金,在航空工业主要用于发动机压气机盘、叶片和喷管等[1-4]。本公司采购的一批TC11合金棒料直径为120mm,交付量为2494kg/16支,节号依次为1-1、1-2、……4-1、4-2……8-1、8-2,在入厂超声波检验时发现节号4-2局部有超标显示。棒料超声波验收要求为GB/T5193A1级,该批棒料整体杂波水平φ1.2-6dB,超标显示当量为1.2+13dB,深度73mm,距离4-2号棒料端面210mm。超声波超标部位波形如图1所示,在超声波超标处切取试片(见图2)。
本文采用X射线探伤仪、光学显微镜、维氏硬度计、扫描电镜、能谱仪等检测设备分析了超声波检测到的缺陷的产生原因。
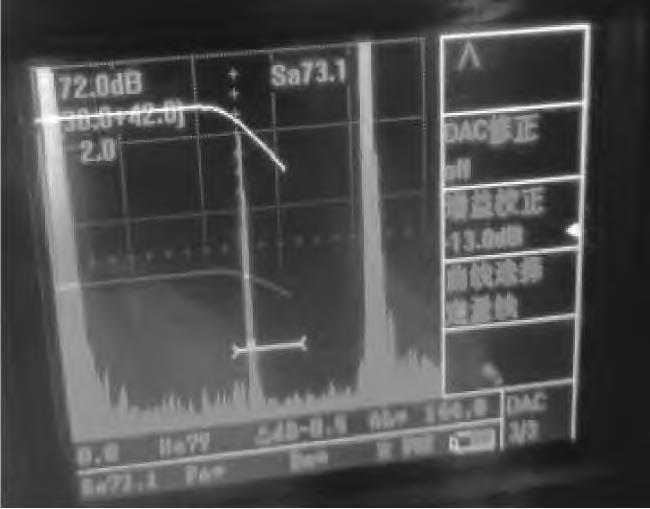
图 1 4-2 号超声波超标处波形
1、X射线检测
首先对缺陷部位进行X射线定位检测,照射方向垂直于试片横截面,获得的X光底片如图3所示。经X射线照射,仅有一处白点显示,然后从点状显示处的侧面检测其分布深度,结果如图4所示。
由X射线底片可知,缺陷部位的线衰减系数大于正常部位,而线衰减系数与吸收材料的密度成正比,因此,初步判断缺陷为贯穿性的,密度高。
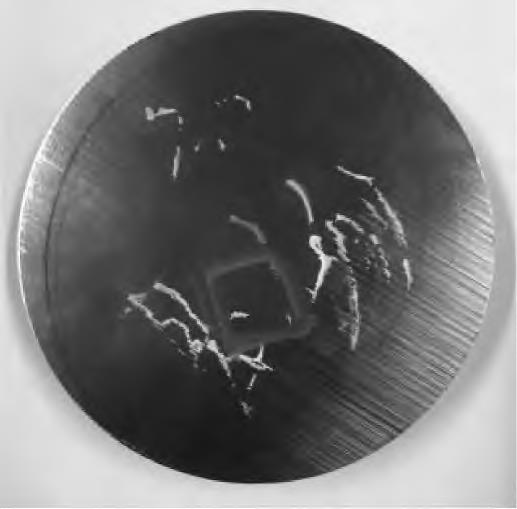
图 2 超声波超标试样
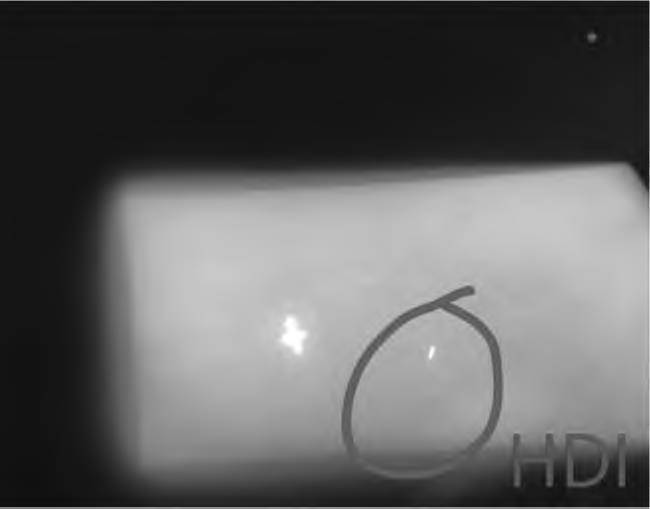
图 3 缺陷位置
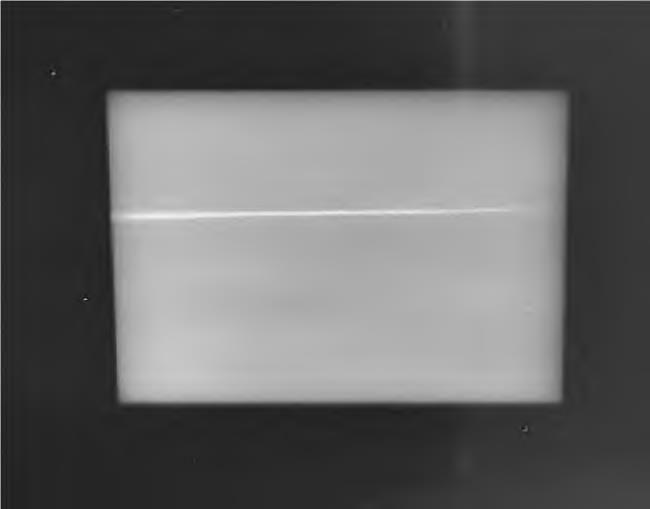
图 4 缺陷深度
2、金相检验
贯穿性高密度缺陷一侧横截面抛光态形貌如图5所示,夹杂物与基体之间有明显界限。图6表明,浸蚀后夹杂物与基体之间有明显的过渡区。图7为夹杂物纵截面抛光态宏观形貌,抛光态夹杂物目视可见,且与基体界面熔合良好,仅有个别微小孔洞。
图8为夹杂物-过渡区-基体之间的显微组织。Ⅰ区为夹杂物;Ⅱ区为夹杂物前沿的过渡区;Ⅲ区为基体前沿的过渡区,显微组织为β相;Ⅳ区为基体,其显微组织为正常的α+β组织。
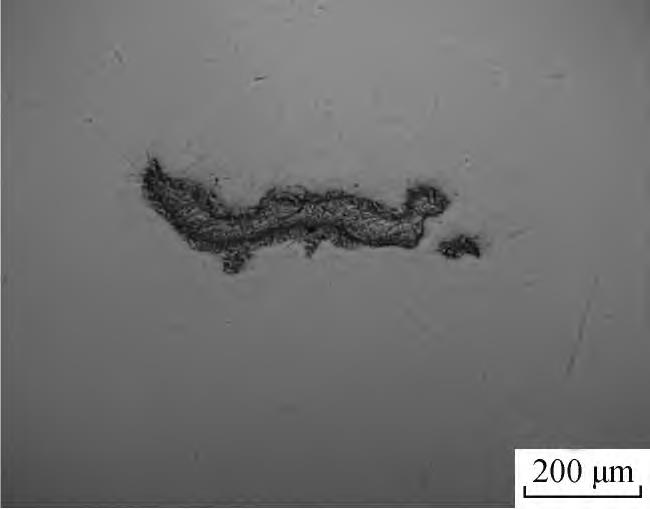
图 5 夹杂物横截面抛光态微观形貌
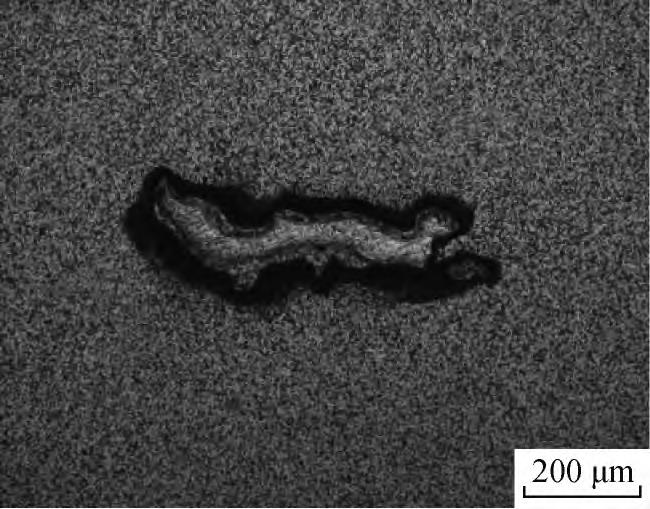
图 6 夹杂横截面腐蚀态微观形貌
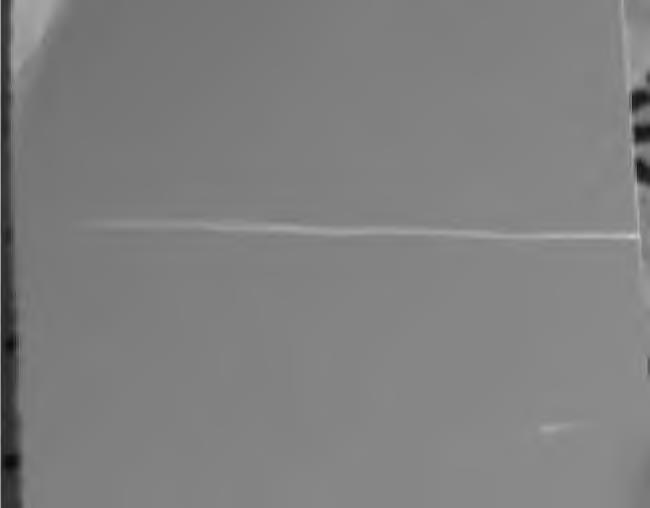
图 7 夹杂纵截面宏观形貌
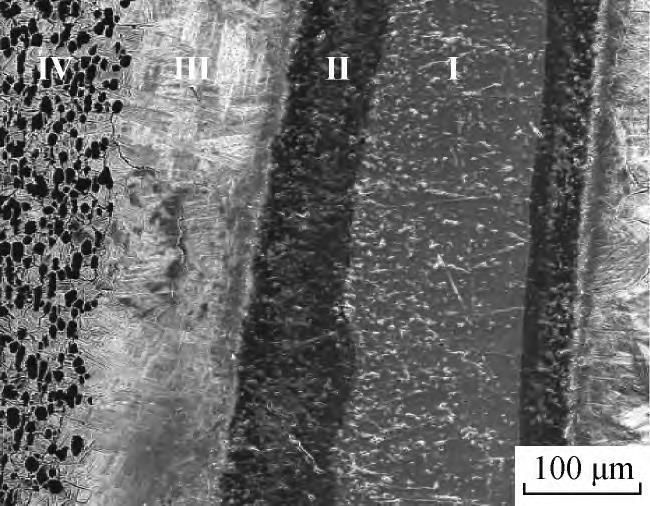
图 8 夹杂物与基体间的显微组织
3、微区化学成分和显微硬度检测
图9为夹杂物的能谱分析线扫描结果,中间发白区域主要成分为Mo,其密度为10.2g/cm3,TC11钛合金密度为4.48g/cm3,可进一步确认缺陷为贯穿性高密度Mo夹杂。从夹杂物区至过渡区至基体的Mo含量迅速降低至正常含量。图10和表1为Mo夹杂、过渡区和基体的能谱分析位置和检测结果,Mo夹杂前沿过渡区Mo含量约为20%~27%,Ti、Al含量略低于基体区,无Zr元素,此处可能为Mo夹杂区,基体元素向夹杂处扩散,形成过度区。
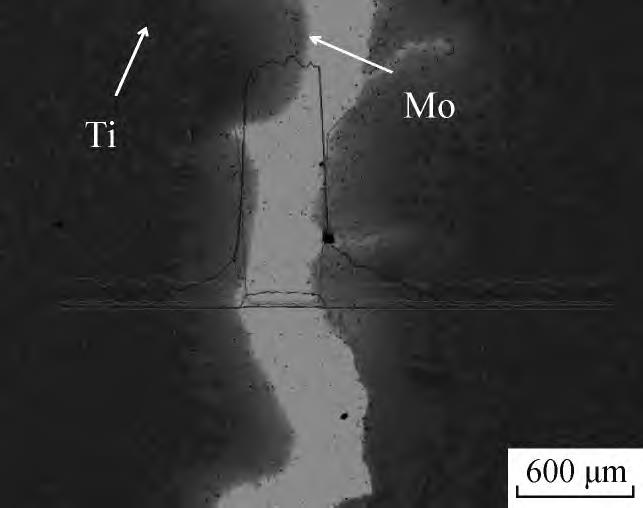
图 9 夹杂与基体间的能谱分析的线扫描结果
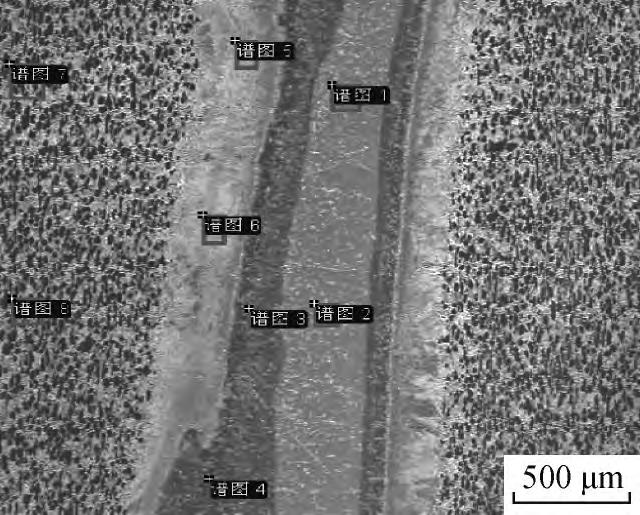
图 10 夹杂物与基体间能谱分析的点扫描位置
基体前沿过渡区Mo含量约为12%,Al、Ti、Zr、Si含量与基体正常区基本一致,说明此处原为基体正常区,由于夹杂物中Mo向此处扩散,导致此处Mo含量升高,因Mo为β相稳定元素,导致此处β转变温度显著降低,因此其显微组织为典型的高Mo偏析β相。
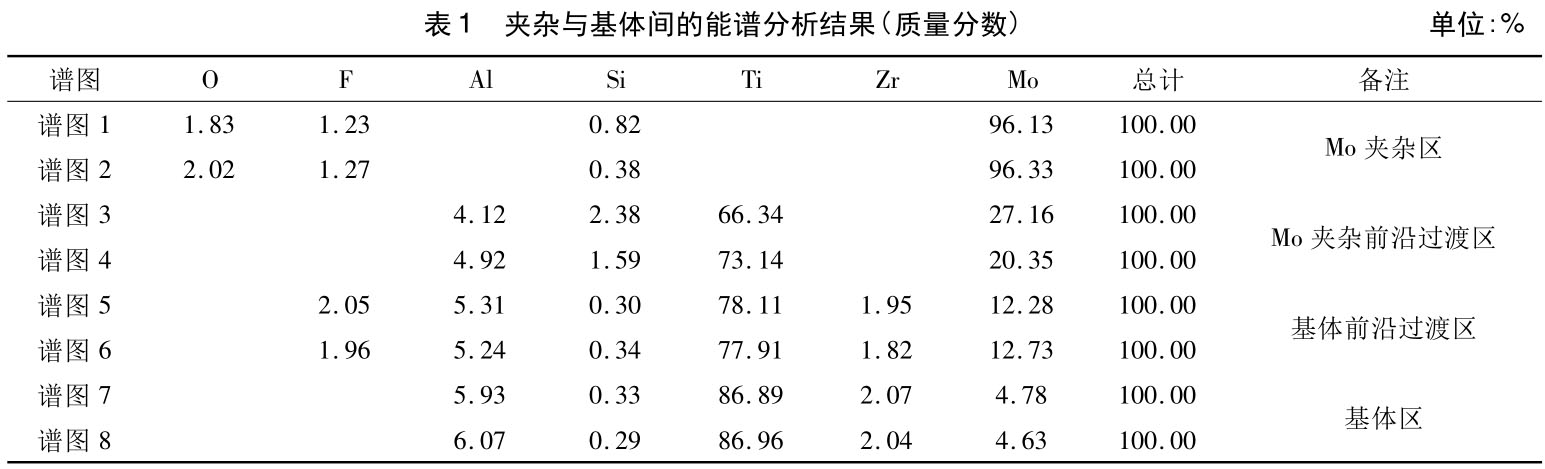
表2为Mo夹杂至基体的显微硬度,基体至Mo夹杂物区显微硬度从352HV0.1逐步降低至262HV0.1,平缓的硬度梯度能保证夹杂物在棒料开坯和锻造过程中与周围正常基体同步变形,减小了夹杂物处产生较大裂纹的可能性。成品棒料中的夹杂物与基体之间有良好的熔合界面说明了这一点。
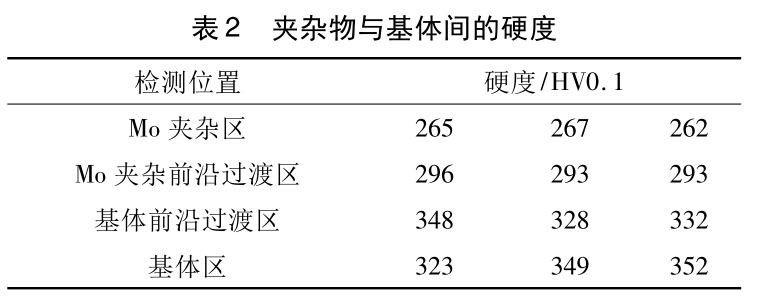
4、缺陷产生原因
X射线分析表明,缺陷为细长条状高密度夹杂物。由显微组织和能谱分析结果可知,高密度纯Mo夹杂与基体组织之间为冶金结合,并有元素扩散,可以排除在铸锭锻造成棒料的过程中外来夹杂物嵌入的可能性。因为锻造过程嵌入的高熔点Mo夹杂会与基体产生明显的间隙界面,且不会发生明显的元素扩散和冶金结合。超声波检测缺陷位置在4-2号棒料的一端,根据棒料节号进行反推,夹杂物缺陷大约位于铸锭中部,如图11所示。本批棒料所用铸锭共进行三次熔炼,示意图如图12所示。本批棒料制备了两根一次电极,棒料中的Mo元素在一次电极制备过程中以l-60Mo合金添加剂而非纯Mo的形式加入。两根一次电极一次熔炼形成的一次锭经炉内对焊后进行二次熔炼和三次熔炼。铸锭三次熔炼过程正常、平稳、无异常,成品铸锭头尾化学成分均满足技术要求,且偏差较小,说明整个熔炼过程受控,并无产生Mo夹杂的明显条件。根据缺陷出现在铸锭中部且一次锭的对焊过程,可推测产生缺陷的原因可能是一次锭起吊装炉过程中,底部与铸锭存放区的钢板接触,导致外来物带入铸锭中。
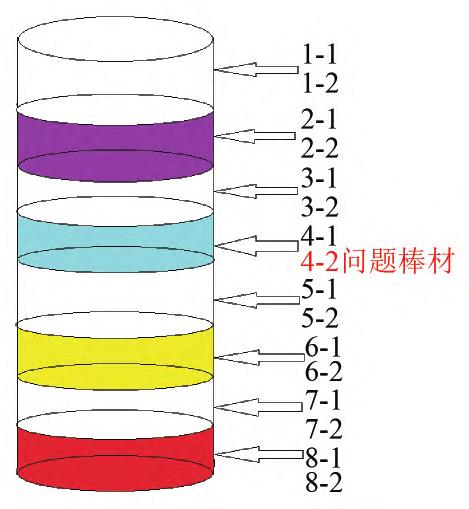
图 11 棒料位置分布示意图
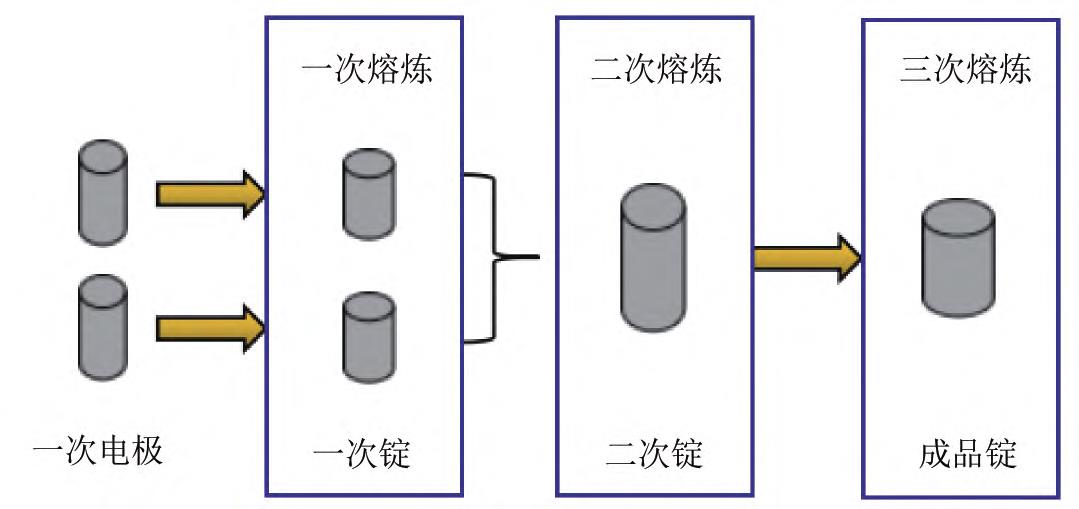
图 12 铸锭熔炉过程示意图
5、结论
TC11钛合金棒料超声波超标部位的缺陷为细长条Mo夹杂,夹杂物与基体界面熔合良好,并形成由元素扩散产生的过渡区。Mo夹杂可能产生于一次锭熔炼后对焊前的吊装过程,说明铸锭生产现场环境有待进一步改善。建议加强生产现场管控,防止外来金属带入生产现场,设置专用的吊装区域,并在吊装前对该区域进行彻底清理。
TC11棒料缺陷在入厂复验时发现,说明棒料出厂前超声波检测有漏检。应改进超声波检测方式。
参考文献
[1]江想莲.TC11钛合金热变形行为及其组织演变规律的研究[D].沈阳:东北大学,2011.
[2]张利军,薛祥义,张晨辉,等.TC11钛合金锻件中疑似夹杂物缺陷成因分析[J].理化检验:物理分册,2015(10):734-736.
[3]宫敏利,李淑英.TC4钛合金锻件缺陷分析[J].热加工工艺,2016,45(3):258-260.
[4]宋鸿武,张士宏,程明,等.钛合金热变形过程中裂纹缺陷的预测[J].稀有金属材料与工程,2012,41(5):781-785.
相关链接