1、引言
目前国内外新兴的金属增材制造技术打印技术为新产品的制造带来了革命性的突破,在很大程度上改变了传统的思维方式和固有的研发流程,实现了复杂产品构件设计制造的高质量快速响应。欧美等世界各国的高度重视金属增材制造技术快速发展。尤其对该技术在航空航天领域的应用开展了大量研究工作并将这一先进技术工程化。美国航空航天局已于2012年底开始打印零件并用于下一代大推力火箭的测试。2013年8月,NASA对用3D打印技术制作出的火箭发动机喷射器进行了成功测试。欧洲宇航防务集团创新工场和欧洲光学学会使用直接金属激光烧结技术制造的钛零件替代空客A320发动机舱的铸钢铰链支架。在关键载荷位置优化金属结构布置,削减了75%的原材料重量。
金属3D打印也叫金属增材制造。基于给粉的方式不同,3D打印技术主要分为两大类:基于同步送粉激光熔覆技术发展起来的成型技术,本项目采用的3D打印技术是目前成形最精密的SLM(精密选区熔化)技术,基于快速成形的最基本思想即逐层熔覆的增材制造方式,根据零件的三维模型。将模型按一定的厚度切片分层,即将零件的三维形状信息转换成一系列二维轮廓信息,随后在数控系统的控制下,用激光通过阵镜控制来熔化金属粉末,直接成形具有特定几何形状的零件。成形过程中金属粉末完全熔化,熔化的粉末制件产生良好的冶金结合。由于SLM技术可直接获得几乎任意形状、具有完全冶金结合、高精度的近乎致密金属零件,应用范围比较广,主要是航空航天领域的超轻结构件、机械领域的工具及模具、生物医疗领域等。它主要特点是:不去除材料的毛坯表面精度可到达Ra6.3μm,与部分机加工方式精度相当;成形精度高,可获得0.1mm的立方网格结构体;由于SLM光斑集中,成形过程熔池大小≤0.1mm,沉积成形体材料内部组织非常细小、均匀,晶粒尺寸达到微米级;致密度几乎能达到100%。零件机械性能与锻造工艺所得相当,综合性能优异。本项目需采用TC11高温钛合金材料实现航天高精度复杂零件SLM增材制造并应用目前在国内还较少,需进行相关设计制造技术研究。
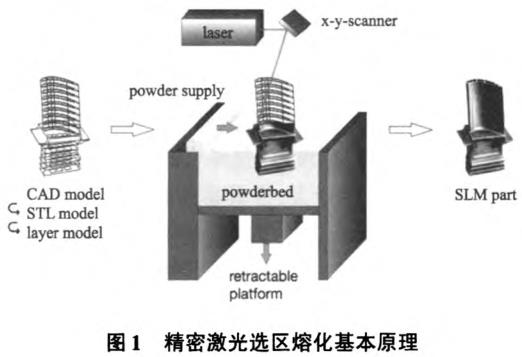
提高产品结构的功率质量比对航天产品意义十分重大。航天高温钛合金结构件复杂的产品制造过程可通过开展基于SLM技术的设计、制造研究而高效、集约实现。即首先通过有限元分析计算及专业软件实现基于SLM增材制造结构的轻量化、一体化设计:其次通过合理优化的工艺参数和后续热处理来实现SLM增材制造零件制备;之后应用技术研究包括SLM增材制造高温钛合金难加工材料的切削性能研究、SLM增材制造零件的精密机械加工技术研究、基于SLM技术产品检测与试验方法研究等实现实际应用。通过以上研究解决了零件快速成型问题,减轻零件重量,改善切削加工性能,提高产品质量,缩短生产周期,满足使用要求。
2、产品特点
本课题产品工作环境恶劣,工作工质为约1200℃的高温气体,表面工作温度达(400~500)℃,承载着高达几万转的工作转速的轮系。为了满足恶劣环境和减重设计要求,对材料高温性能要求高,且结构与制造过程复杂。原产品由前壳体A、前壳体B、进气嘴、后壳体、排气管、左、右支架、压板共12个零件组成,通过锻造、焊接、热处理、精密机加、组合机加、装配等工艺环节组装成壳体组合件,主要制造过程见图2。
产品制造过程中主要存在以下问题:①制造周期长。产品从备料到产出需六个月时间;②材料利用率低。整体材料利用率为21.3%,材料浪费严重:③焊接难度大。耐高温钛合金材料焊接需要保护,大厚度封闭焊缝需多层焊接并容易产生裂纹;④加工难度大。涡轮壳体尺寸加工要求高,但由于多次焊接、热处理造成壳体变形大,另外壳体结构复杂,需要较多的工装保证加工尺寸:⑤装配难度大。涡轮壳体与支架安装处由于焊接变形和无法二次机加,装配时与涡轮支架装配间隙大,降低了结构刚度,易造成装配过约束。
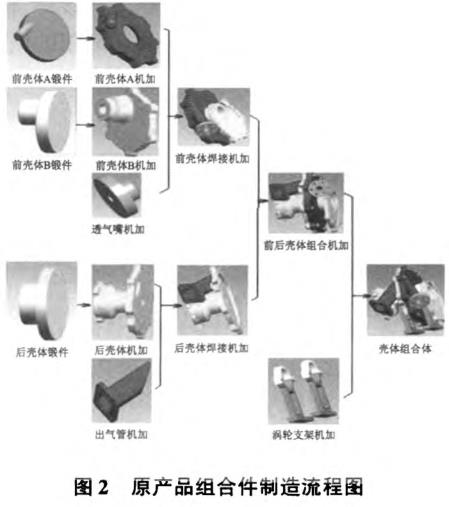
3、基于SLM增材制造的功能最优一体化、轻量化设计
实现过程首先在于设计基于SLM技术优先关注功能的实现,不考虑制造工艺。通过有限元分析计算及专业的金属3D打印模型设计、处理软件实现基于SLM技术的功能最优一体化、轻量化的设计技术。
采用一体化设计:在满足现有产品性能和接口要求的前提下,首先对涡轮壳体进行了结构一体化设计,由原来12个零件缩减至两个零件。通过仿真计算,为壳体的3D打印提供依据。模型如图3所示。
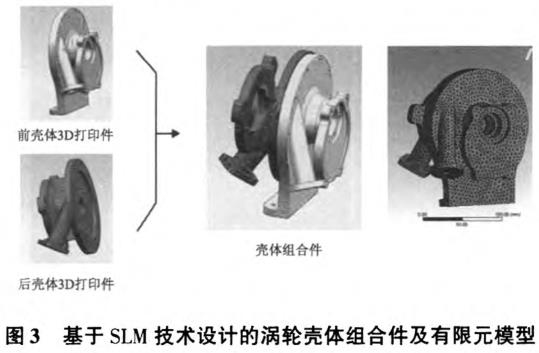
轻量化设计:通过专业软件对壳体非主承力部位进行镂空结构处理,应用拓扑网状结构,保证结构体刚度强度的情况下,保证壁厚不变及避开安装孑L的情况下,获得更大的减重效率模型薄壁边界与内部构建中空网格支撑形状如图4。
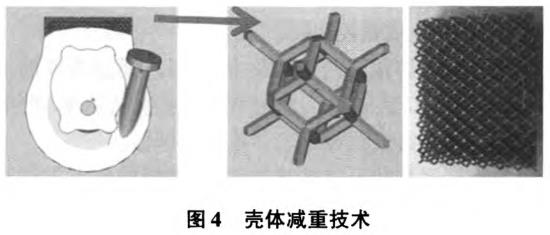
壳体结构功能优化设计:利用专业的金属3D打印模型设计处理软件对壳体结构进行功能化结构设计、优化处理,使壳体构件更加趋于完全功能化。如采取新的结构设计对壳体构件筋条进行处理。
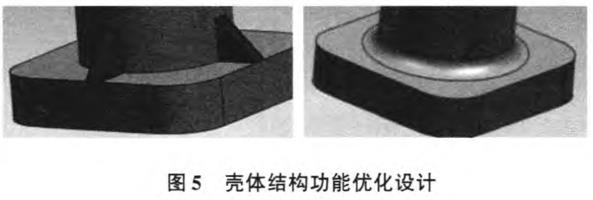
4、SLM成形工艺技术
项目采用TC11高温钛合金实现壳体制造。TC11高温钛合金工作温度可达500℃以上,但成型过程变形与开裂的倾向大。对产品在激光选区熔化成形过程中会发生变形的部位,通过整体支撑加固、薄壁加厚、不同辅助支撑结构措施来自由成形产品中的复杂结构:经过金属3D打印专用软件的系统运算、模拟对比,最终确定局部支撑形貌。优化支撑结构也解决了钛合金激光选区熔化过程中的变形开裂问题:
SLM增材制造构件内部质量和性能的控制主要是通过合理优化的工艺参数和后续热处理来实现。
1)设备:采用EOS M280型选择性激光熔化设备。400W光纤激光器,最大零件成形尺寸为250mm×250mm×300mm,成形过程中通过惰性气体对成形零件进行保护。
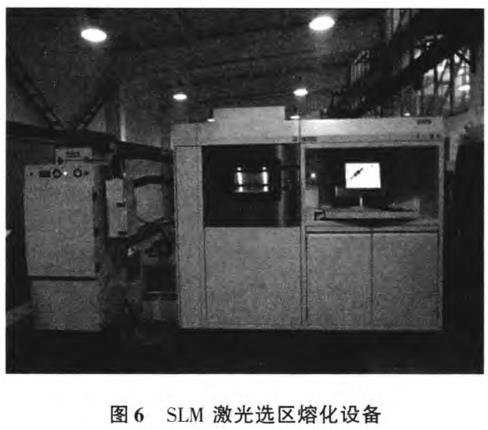
2)基材:钛合金板
3)激光选区熔化代码生成:在激光选区熔化之前确定成形件的三维模型。然后通过Magics软件对模型进行处理,最终生成支撑。然后将处理好的模型Rp—Tools切片分层生成程序文件,最终生成数控代码。
4)激光选区熔化工艺参数及生产过程:通过合理的工艺试验验证,严格控制成形工艺过程,确保激光功率、扫描速度、扫描路径、气氛控制等工艺参数的合理性。
5)激光选区熔化壳体的热处理:根据新的成形方法对传统标准热处理工艺进行调整,建立与SLM增材制造工艺及TC11高温钛合金相匹配的热处理制度(双退火),改善材料内部组织和残余应力状态。调整零件性能。
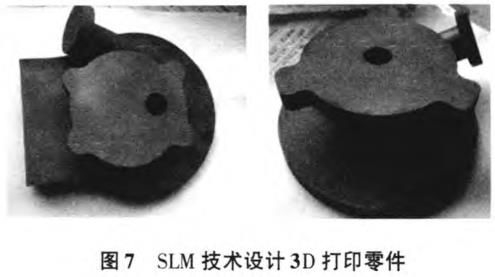
5、SLM增材制造高温钛合金零件切削性能研究
5.1 SLM增材制造高温钛合金材料切削性能研究
SLM增材制造的TC11耐高温钛合金材料为新型难加工材料。具有高温强度、硬度高,热导率低,精密切削加工过程中切削温度高,加工变形大,刀具易磨损的难加工特点。选择各种切削刀具。针对SLM增材制造耐高温钛合金材料车削、铣削、磨削精密切削加工过程开展切削性能研究。研究SLM增材制造高温钛合金材料切削过程中的与切削参数以及刀具和切削参数之间的关系,掌握材料切削性能。将切削性能研究成果进行实际应用,促进高效率、高精度、高性能SLM增材制造技术的应用,参数选择见图8。
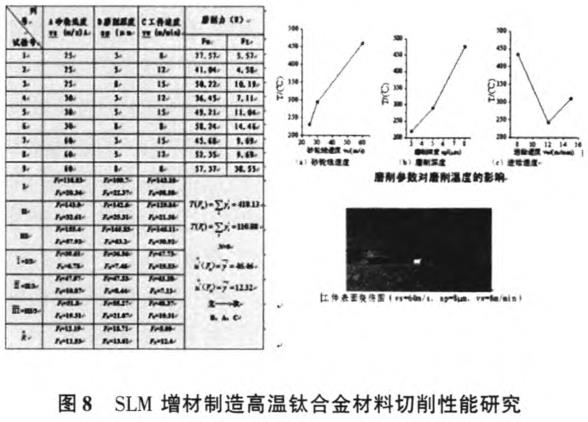
5.2 SLM增材制造零件的精密机械加工技术研究
1)工艺流程设计:整体设计的零件复杂,空间交汇点多,需满足众多关键技术要求。精度要求达微米级。结合SLM复杂壳体的特点进行工艺流程设计:采用多轴加工中心,精密车床、精密磨床多种设备充分结合,制定多种关键工序控制点结合的工艺流程。利用加工中心工作台旋转功能和原点转换功能一次加工多个关联的基准,并采用试切法调整零偏,为后续所有加工提供加工基准;同时针对SLM增材制造涡轮壳体的变形问题提出平衡装夹力、增加辅助支撑、调整加工参数等工艺策略,解决复杂结构精密加工难点,满足基于SLM增材制造涡轮壳体的微米级尺寸精度及众多关键技术要求。精密加工过程见图9。
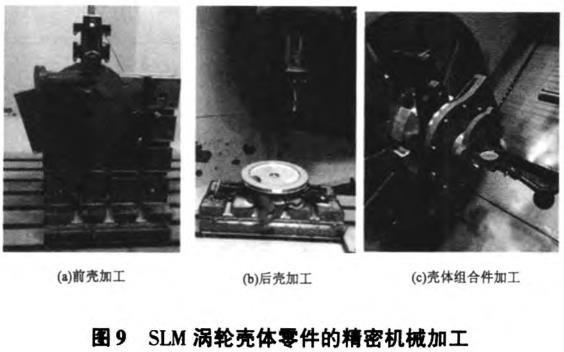
2)切削工艺的选择及切削参数的优化:针对SLM新型难加工材料切削过程产生振动及形成较差的切削条件的特点。运用防振刀杆、改制螺纹铣刀等刀具形式,同时将切削性能研究成果进行实际应用,针对切削加工的主要因素如切削速度、进给速度、切削程度等,进行切削工艺试验进行切削参数的优化,保证精度指标。解决深盲孔加工、小螺纹孔加工、高精度偏心孔的数控加工等加工难题,为零件实现SLM增材制造提供应用技术保障。
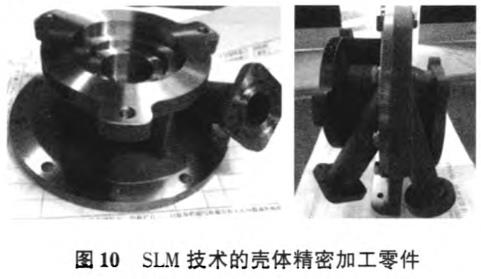
6、基于SLM技术产品检测与试验方法研究
为了检测产品性能满足性。开展了零件三维扫描测量、化学成分和组织分析、高温和室温力学性能检测、无损探伤等检测。并根据产品使用要求开展地面载荷试验。
1)三维扫描测量技术实现产品的快速、可视化尺寸及形位质量检测
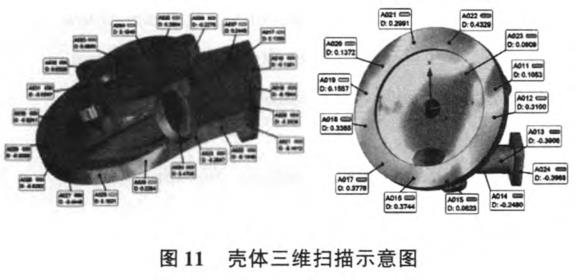
2)SLM增材制造高温钛合金材料的成分及理化性能检测和评判标准研究。为新材料应用可行性提供基础数据化学成分和组织分析通过产品同炉试块分析,成分检测内容包括:Ti、Al、Si、Zr、Mo、C、H、O、N等;高温和室温力学性能检测包括抗拉强度、规定非比例延伸强度、断后伸长率、断面收缩率等室温力学性能检测,500℃高温力学性能检测;着色渗透荧光检测和x光探伤主要检测壳体成形后的表面质量和内部裂纹等缺陷。
3)地面试验考核气密试验考核产品结合面密封可靠度的试验,对产品充气0.6MPa。保持5min,不允许有压降。试验满足设计指标。
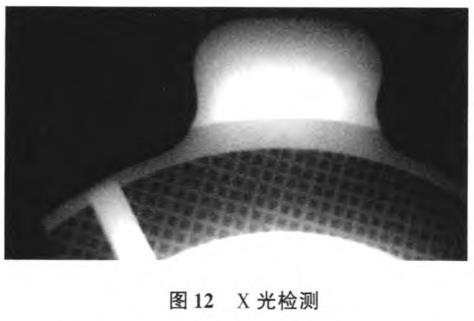
按照技术要求,产品在额定负载和半负载下进行冷气试验,考核产品在冷状态下与其它零部件的匹配性以及功能满足性。冷气负载试验结果表明性能满足设计指标。
7、结论
采用了基于SLM的金属增材制造技术实现了结构复杂度高、工作环境苛刻、可靠性要求高的航天关键零件的3D打印与精密加工。突破了基于SLM技术的功能最优一体化、轻量化的设计技术,应用拓扑网状结构,在保持结构强度和刚度基本不变的条件下,减轻了零件的结构质量10%左右,零件生产周期相对于传统制造工艺缩短50%以上,材料利用率由21.3%提高到达到85%以上:突破了基于SLM技术耐高温钛合金TC11增材制造技术应用研究,材料性能达到材料手册提供的物理性能指标,零件尺寸精度达到±0.1mm、表面粗糙度小于Ra6.3μm,处于国内领先水平;突破了精密加工及三维检测技术,实现了复杂零件空间尺寸的三维在线检测,大大提升了检测效率。产品通过了地面冷气试验考核验证。
该项目为航天产品快速制造平台构建提供了技术支持,提供了一种高效、集约的新型设计制造方式,对提高产品性能、提高材料利用率、降低研制周期、节约生产装配成本具有重要意义。
参考文献:
[1]王运赣.三维打印自由成形[M].北京:机械工业出版社,2012.
[2]任敬心.难加工材料磨削技术[M].北京:电子工业出版社,2011.
相关链接