引言
钛合金具有比强度高、密度低、耐腐蚀、耐热性能好以及生物相容性优异等优点,被广泛应用于航空航天、新能源及生物医疗领域[1-2]。但是,钛合金具有锻造温度区间窄、变形抗力大、高温组织性能对生产环境敏感等工艺特征,使用传统工艺生产加工钛合金构件时,生产工艺复杂、生产效率低、材料利用率低、加工成本高[3-4]。近年来,增材制造技术的发展为钛合金构件的生产制造提供了全新的思路[5],该技术无需配套零件模具,通过逐层堆垛的方式制造实体零件[6],可以有效减少工序,降低生产成本,具有广阔发展前景[7-9]。相比于传统的加工方式,增材制造在成型原理、原料形态以及制件性能等方面发生了根本性转变,被认为是制造业的一次革命性突破。金属材料的增材制造根据热源的选取不同可以分为电弧增材制造(Wire Arc Additive Manufacture, WAAM)、激光增材制造(Laser Additive Manufacturing, LAM)以及电子束增材制造(Electron Beam Additive Manufacture, EBAM)等技术[10]。其中电弧增材制造技术以电弧作为热源,采用逐层堆焊的方式制造实体零件,因其加工成本低,沉积效率高等优点[11]被广泛地应用于钛、铝等金属材料的增材制造。WAAM 方法及概念的提出可以追溯到 1925 年,Baker[12]使用简单的电弧焊接沉积出了金属的花托和装饰性收纳篮。在钛合金电弧增材制造中,由于逐层堆垛过程中会经历多次热循环,凝固过程金属过冷度高、温度变化大,高温 β 相会转变为不同形态的 α 相,包括马氏体 α'、马氏体 α''、针状 α、晶界 α 和网篮状组织等。这些不均匀的微观组织及脆性相容易形成裂纹,影响整个构件的力学性能[13,14]。为改善电弧增材制造钛合金的微观组织及提高其力学性能,国内外学者通过优化加工工艺与冶金等方式对钛合金增材组织进行调控。Malinov 等[15]发现通过不同的热处理,钛合金中 α、α'、α''和 β 相的比例会有所不同;何智等[16]研究了超声冲击对电弧增材制造钛合金零件组织和性能的影响,发现超声冲击能够使晶粒破碎为细小的等轴晶,并且随着冲击次数的增多,试样的抗拉强度有所提高;Mereddy 等[17]通过在电弧增材制造钛合金时添加硅元素发现,随着硅添加量的增多,晶粒尺寸逐渐减小。
当前,钛合金的电弧增材制造方法及微观组织调控已经逐渐成为研究热点,学者们围绕着新型方法、增材制造后处理以及增材过程实时调控等方面进行了大量研究。然而系统性的综述报道还很少,缺少对当前研究工作的总结与展望。本文针对钛合金电弧增材制造工艺方法及微观组织调控,首先介绍了不同的 WAAM 系统,并对不同钛合金电弧增材制造方法进行了介绍与对比分析,提出了钛合金电弧增材制造所面临的主要问题和难点,在此基础上重点综述了当前用于调控材料组织及性能的几种辅助工艺,最后对钛合金电弧增材制造的未来发展做了展望。将为钛合金电弧增材制造技术提供基础研究思路,为高效高质量钛合金增材制造件的开发与应用提供技术参考,对推动该技术的进一步应用具有重要意义。
1、 钛合金电弧-丝材增材制造工艺方法
WAAM 系统由热源、自动送丝系统、数控工作台或机器人系统组成。当前 WAAW 主要基于传统焊接电弧进行优化改造,按照热源及送丝方式的不同,WAAM 主要分为三种工艺方法:以钨极气体保护焊(Gas Tungsten Arc Welding, GTAW)为热源的旁轴送丝增材制造技术、以等离子弧焊(Plasma Arc Welding, PAW)为热源的旁轴送丝增材制造技术和以熔化极气体保护焊(Gas Metal Arc Welding, GMAW)为热源的同轴送丝增材制造技术,其特性如表 1 所示。
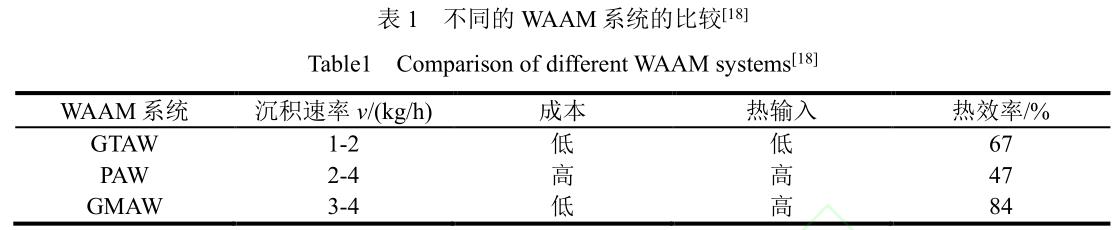
1.1 基于 GTAW 的 WAAM 工艺
基于 GTAW 的电弧增材制造技术利用钨电极和基板之间产生的电弧来熔化焊丝,按照设定的路径逐层沉积实体零件,如图 1 所示[19]。在沉积过程中,送丝方向影响材料传输和沉积质量。可采用后送丝、侧送丝、前送丝等不同方式,钛及钛合金的增材制造通常采用前送料。随着电弧长度的增加,屏蔽喷嘴与工件之间的距离也相应增加。Baufeld 等[20-22]在 GTAW热源制备的电弧增材制造 TC4 钛合金中,发现其组织为粗大的外延生长 β 柱状晶,并且当焊接方向发生改变后 β 柱状晶的指向也随之发生改变,如图 2 所示。堆垛件的顶部和底部的组织也有所不同,顶部冷却速度较快,组织为较为细小的 α 集束,底部在多次的热循环作用下,组织为粗大的网状 α 结构。Wang 等[23,24]也发现了相似的 β 柱状晶组织,并且还研究了送丝速度对焊后组织转变的影响。当送丝速度增加到一定程度时,柱状 β 晶粒最终将转变为等轴晶。Wang 和 Baufeld 等对电弧增材制造的钛合金的力学性能也有所研究,发现钛合金构件在沉积方向及焊接方向上的力学性能存在各向异性。原因是初生的β 相贯穿整个试样外延生长,从而造成各方向上组织与性能均存在差异。钛合金增材制造件显微组织的不均匀性与其力学性能的各向异性有所关联,所以可以通过优化成型工艺参数来获得组织均匀的钛合金构件,弱化各向异性,提升综合力学性能。
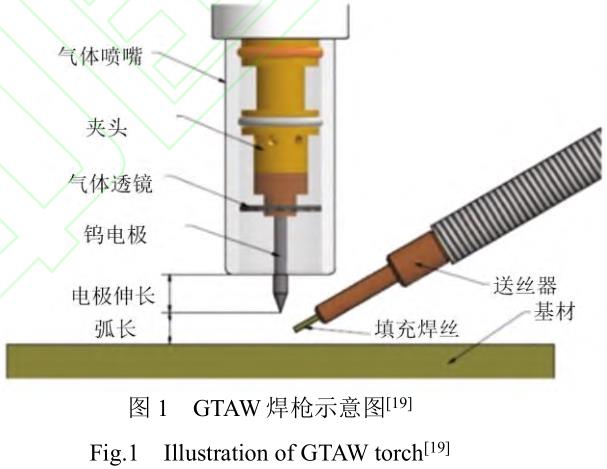
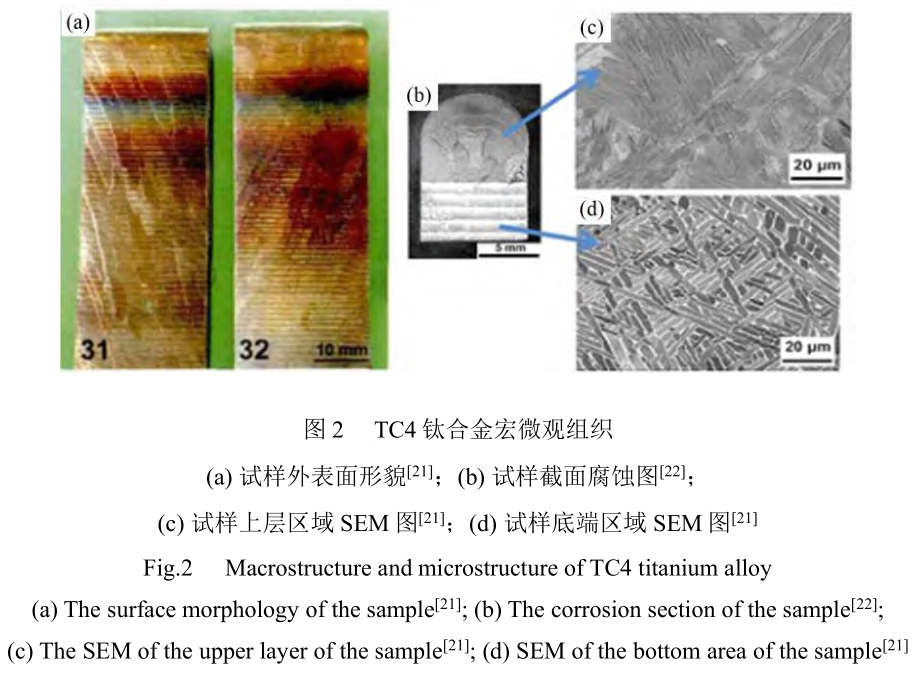
1.2 基于 PAW 的 WAAM 工艺
PAW 增材制造技术使用等离子弧作为热源进行增材制造,等离子弧具有高电离度、高能量密度、高流速等特点,通过热压缩和机械压缩等作用,等离子焊接中的电弧能量密度可以达到 GTAW 的 3 倍,且具有电弧稳定、沉积速度快、成型质量高等优点,如图 3 所示是一种基于 PAW 的 WAAM 系统[25]。Martina 等[26]利用 PAW 增材制造方法制备了 TC4 钛合金构件,并研究了不同工艺参数对钛合金成型特征及组织特征的影响。通过改善工艺获得了粗大 β 柱状晶粒,并建立工艺参数与堆垛件总壁宽、有效壁宽和层高之间的回归模型。Lin 等[27]研究了等离子弧增材制造 TC4 钛合金的组织演化与力学特征。研究发现,随沉积层数的增加,通过逐渐减少电流以降低热输入,能够减小 β 晶粒尺寸,然而 α 相在 β 晶粒内分布不均匀,存在针状马氏体和魏氏体的混合组织,并且 α 片层的宽度与沉积高度有一定联系。
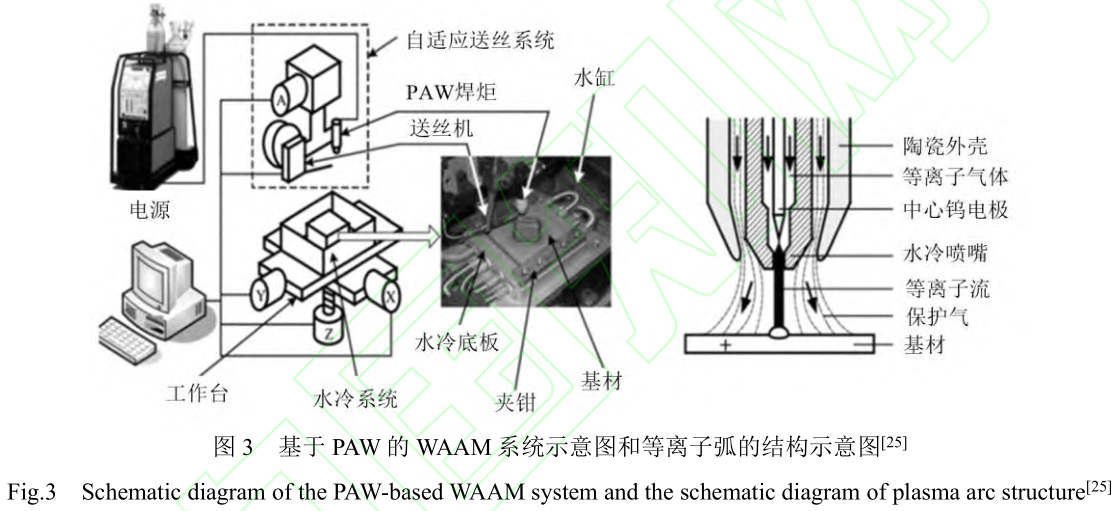
1.3 基于 GMAW 的 WAAM 工艺
GMAW 电弧增材制造技术是一种以熔化极气体保护焊为热源,将丝材均匀送入熔池熔化并快速凝固成型的增材制造方法。20 世纪 90 年代,Spencer 等[28]提出了采用 GMAW 技术进行增材制造的方法来快速成型金属模具。但使用此方法较大的热输入会导致材料存在较大的残余应力,且焊接过程中飞溅、烟尘较大。目前 GMAW 常采用冷金属过渡(Cold Metal Transfer,CMT)方法,这是一种由 Fronius 公司开发的脉冲短路焊接技术,CMT 通过耦合焊接参数和焊丝移动确保受控熔滴转移,采用此种工艺,能在较低的热输入下实现熔滴接触过渡,减少飞溅。Gou 等[29]通过研究 CMT 电弧增材制造制备 TC4 构件过程中热输入对增材构件组织与性能的影响情况,发现一部分 α′马氏体组织由于逐层沉积的热循环过程而转变为 α+β 层状的混合物,且 α 晶粒中出现了大量的位错。张飞奇等[30]以 TC4 钛合金丝材为原料,采用 CMT 电弧增材制造,得到堆积层底部为柱状晶、顶部为等轴晶的组织结构,在堆积区与熔合区均没有马氏体相的出现。值得注意的是,在使用 GMAW 进行钛合金的增材制造时,会出现电弧漂移,并且获得的表面也很粗糙,所以对于钛合金的电弧增材制造,还是以 GTAW 和 PAW 两种工艺方法为主。
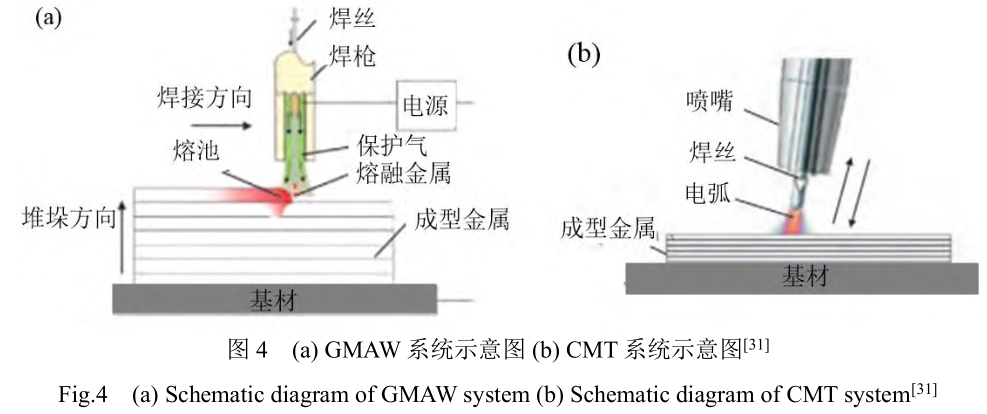
综上所述,对于钛合金电弧-丝材增材制造技术,GTAW、PAW 和 GMAW 三种工艺方法各有特点:GTAW 工艺设备简单,成本较低;PAW 电弧能量密度高,可以获得变形较小且成型良好的构件;在 GMAW 中,焊枪和焊丝同轴,简化了路径生成过程,其沉积速率是 GTAW 和 PAW 方法的 2~3 倍,但稳定性较差。CMT 电弧增材制造方法能够精确控制热输入且实现较高的堆积效率,将成为未来制备钛合金复杂大型构件一种有效的方法。WAAM 工艺还要与材料特性相匹配,零件的精度要求及结构复杂情况将决定 WAAM 工艺的选择。对于钛合金来讲,GMAW 会导致电弧漂移,影响构件的成型质量,GTAW和 PAW 更适用于钛合金,但由于其采用外部送丝的方式,增材构件的成型质量主要取决于堆垛过程中的送丝与电弧的稳定性[32],通过对送丝的控制,实现连续的搭桥熔滴过渡方式[33], 会获得成型良好的优质零件。
2 、电弧增材制造钛合金微观组织调控
如前所述,WAAM 具有成本低、生产效率高的优点。然而,WAAM 制造过程中涉及到电弧热源下的液态金属的非平衡凝固[34],前一道金属在逐层堆垛过程中,经历多次热循环,这种独特的热特性将影响增材构件的微观组织、机械性能和残余应力分布[35],这些问题严重限制了钛合金增材制造构件的使用寿命和应用范围。因此,需要对增材制造的钛合金进行组织调控以提升其性能,当前主要有两种调控方式:一种是在增材制造完成后对增材件进行后处理;另一种是在增材过程中的实时调控。
2.1 钛合金增材件的后热处理
大多数 WAAM 制造的钛合金增材件在垂直(构建)方向上的强度和伸长率均低于沉积方向,这是由于柱状 β 晶粒通过为沉积方向上的张力提供显著的损伤累积路径,来控制断裂行为[36]。当沉积层中存在某些脆性相,如魏氏体相或针状 α 相时,延展性较弱。较大的柱状 β 晶有助于良好的延展性,但可能导致强度降低[37]。通过使用适当的热处理工艺,可以有效地控制和调整金属合金所需的微观结构和机械性能,降低焊后残余应力,提高材料合金组织、性能的均匀性,提高构件的塑性与疲劳寿命[38]。Wauthle 等[39]发现对 TC4 成型件进行去应力热处理可有效促进 α'马氏体转变为平衡相 α 片晶。Gou 等研究发现 900℃和 1200℃热处理后,马氏体 α'相全部转变为 α+β 相,且显著提升组织的硬度和延伸率。Brandl 等[40]采用高温固溶+淬火+退火热处理钛合金堆垛件,发现 TC4 堆垛件组织中柱状 β 晶大量转变为球状,显著减少了材料的各向异性。多阶段后热处理工艺将生产出强度和延展性符合要求的产品,但其缺点是不经济且耗时,因此,通常采用单阶段后热处理来提高塑性、增强强度、消除脆性相和细化晶粒(主要针对柱状晶)。
2.2 层间冷却
图 5 为层间冷却的 WAAM 系统的示意图。可移动气体喷嘴具有提供氩气、氮气或 CO2气体的功能,用于在每个沉积层上提供主动的强制冷却,该工艺可以控制钛合金层间热循环温度在一定范围内,以获得所需的微观结构和机械性能,有助于提高钛合金的硬度和机械强度[41]。Ding 等[42]研究表明,当使用压缩气体进行层间强制冷却来制造 TC4 薄壁结构时,发现层间冷却减少了表面氧化,细化了显微组织,提高了硬度和强度。此外,由于沉积层之间的停留时间缩短,制造效率显著提高。
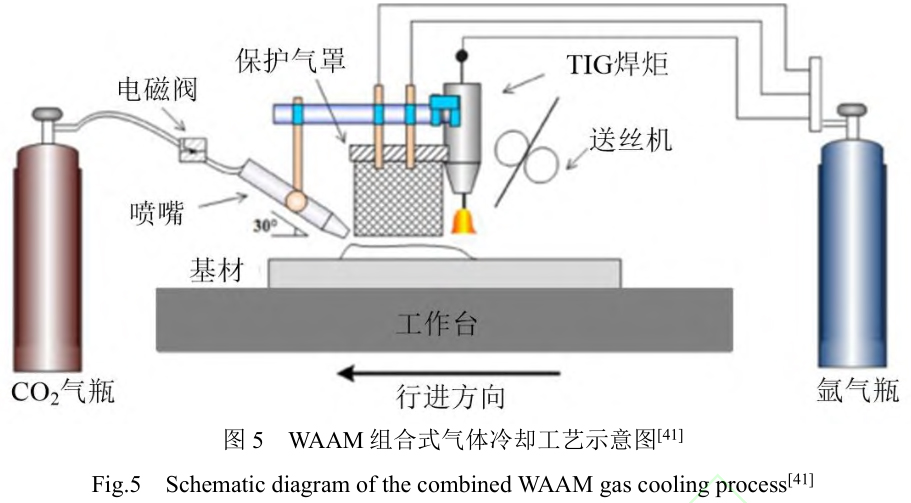
2.3 喷丸和超声波冲击处理
喷丸和超声波冲击处理已广泛应用于工业产品中,这两种技术都是使用高能介质冲击材料表面,通过在材料表面施加压缩应力,使零件中产生弹性变形和塑性变形,从而细化表层晶粒,使取向随机化,进而提高零件的机械强度[43]。经过超声波冲击处理后,WAAM 制备的 TC4 零件的表面残余应力可降低至 58%,显微硬度可提高 28%。此外,表面改性层经过塑性变形,晶粒显著细化,位错密集。Yang 等[44]将 GTAW 焊枪与超声波冲击处理头相连来制造 TC4 构件,沉积过程结束后,立即在沉积件表面施加两次超声波冲击。原有 β 晶粒的宏观结构由粗化的柱状晶转变为等轴晶和短柱状晶的交替分布。Gou 等[45]采用 GMAW 进行 TC4 钛合金增材制造时添加超声波喷丸处理,在每个电弧熄灭后从部件的三个方向进行超声波喷丸,沉积的 TC4 部件中柱状 β 晶和次生 α 晶粒显著细化。超声波冲击处理技术受到穿透深度的限制,穿透深度约为表面下 60μm。因此,尽管这两种技术都是良好的后机械处理,但它们只能改善表面层的材料性能,且作用范围有限。
2.4 添加元素冶金原位调控
热处理及机械处理方法虽然在优化微观组织、提高力学性能以及缓解残余应力等方面起着关键作用,但过程较为繁琐,提高了制造成本与制造周期。近年来,除了在工艺方法上调整外,添加元素冶金调控方法成为前沿的增材制造调控方法。在增材制造过程中引入元素,其一可以通过改变熔覆材料或者使用送粉器送入一定量粉末来添加,其二可以通过改变保护气成分的方式引入元素。Bermingham 等[46]在 TC4 钛合金焊丝表面涂抹了两种不同配比的 B 元素熔覆层,发现 B 元素可以有效消除钛合金 α 晶界和团束组织,细小 α 等轴晶也会有所增加,降低各向异性,原始柱状 β 晶粒也变得更加狭小,微量元素 B的添加使其压缩塑性提升约 40%。此外,添加微量的 Nb、Si、La2O3等也可显著细化晶粒[47-49]。第二种改变保护气成分的方法,可以利用保护气氛与熔池发生冶金作用,实现组织的原位强化。黄健康等采用 GTAW 或 PAW 作为热源,在氩气保护气体中混入一定比例的氮气来原位生成 TiN 增强相[50,51]。研究结果发现,在氮气比例较低时组织中形成了 TiN 树枝晶,当不断增加氮气比例后树枝状的 TiN 逐渐转变为颗粒状。氮原子作用的示意如图 6 所示,氮气分子在高温下电离成原子态,在熔池表面吸附并扩散至内部,最后与 Ti 原子结合生成 TiN 相。对堆垛的钛合金材料进行力学性能测试,发现氮气流量的增加能
够显著提升材料的抗压强度。此外,还研究了在保护气中混入 CO2气体时的作用,发现在组织中生成了大量的 TiOx 和 TiC相,且其含量随着 CO2通入量增加而增加。因为 TiOx 相和 TiC 相的存在,材料的显微硬度和耐蚀性也有所增加[52]。
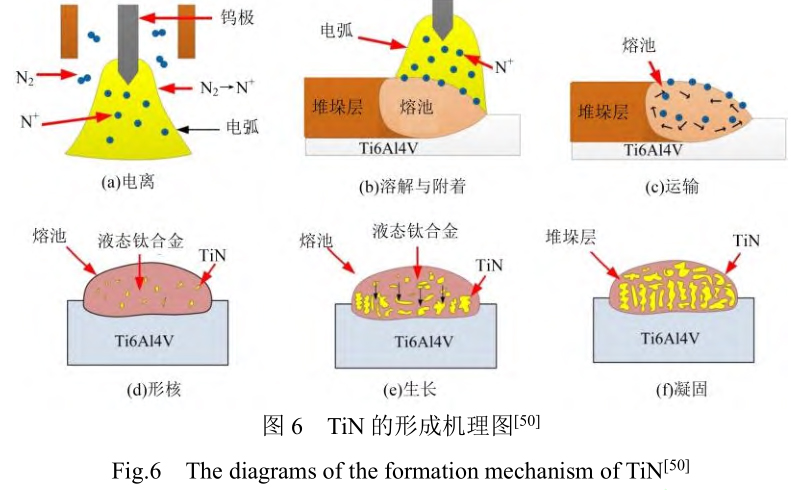
3、 展望
近年来,市场对钛合金增材制造产品的需求及质量要求越来越高,迫切需要提高钛合金增材制造水准。钛合金在逐层堆垛过程中,经历多次热循环,整个过程是一个非平衡热过程,并且在增材制造过程中,材料往往存在复杂的物理化学冶金变化,以上过程影响因素众多,涉及材料、结构设计、工艺过程、后处理等诸多因素,但当前主要的研究工作仍主要集中在材料组织分析、性能规律描述阶段,并未对冶金机理及理论进行深入研究,这也使得增材制造过程的材料—工艺—组织—性能关系往往难以准确把握,难以实现有效控制。因此,未来应进一步研究 WAAM 工艺中潜在的物理化学冶金机理,从而为工艺优化以及组织控制提供指导。
另一方面,如何对增材制造工艺中的残余应力-变形分布、成型精度和微观组织演变进行物理建模分析及预测仍然是一个挑战,通过数值模拟技术可以大大缩短试验周期,有效验证试验中的相关基本理论,当前对于微观组织演化的数值分析及相关的热力学-动力学计算的研究较少,已有的数值模型研究主要集中于移动热源对熔池特征、温度分布及柱状晶组织的影响规律,但是随着数值分析手段的不断完善和丰富,数值模拟将在电弧增材制造领域发挥更大的作用。此外,人工智能也将在 WAAW 加工过程得到更多的应用。例如:基于深度学习的模式识别技术可以用来实现熔池分类、表面缺陷检测等信号分析;强化学习可用于实现 WAAM 的机器人路径自主规划、参数优化和过程控制;大数据的概念将有助于实现数据共享和处理,从而改进 WAAM 的 CAD 设计、工艺优化和质量控制。
4、 结论
钛合金电弧增材制造技术作为先进的钛合金加工制备技术,具有较大发展潜力。通过对国内外钛合金增材制造过程中的工艺方法及微观组织调控的总结与对比分析可获得如下主要结论:
(1) 对于钛合金电弧-丝材增材制造技术,按照热源分类主要有 GTAW、PAW 和 GMAW 三种工艺方法。对于钛合金来讲,GMAW 会导致电弧漂移,并且获得的表面也很粗糙。当前对于钛合金的电弧增材制造,还是以 GTAW 和 PAW 两种工艺方法为主。
(2) 钛合金的电弧增材制造,其组织具有一定的不均匀性以及力学性能的各向异性。可以根据需要,选择在增材制造过程中或增材制造后借助辅助工艺来优化钛合金组织及性能。在增材制造后处理中,通过热处理来消除脆性相、细化晶粒、降低各向异性;另外可以在增材制造过程中进行组织优化,如使用层间冷却、喷丸和超声波冲击、添加合金元素等方式来改善钛合金组织,其中,添加合金元素通过冶金调控的方式可以原位生成增强相,因其可以实时调控材料的成分及组织,将成为未来钛合金增材制造的研究热点。
(3) 对于电弧增材制造钛合金微观组织的调控,已有一定研究成果,但大多还处于试验研究阶段,对于深层次的成型机理的研究还有所欠缺。所以在未来,应进一步研究 WAAM 工艺中存在的物理化学冶金机理,并结合数值模拟技术对微观组织的演化进行预测,以及借助人工智能技术实现电弧增材过程的智能化,这将有助于推动 WAAM 在研究和工业领域的发展。
参考文献
1 Jin H X, Wei K X, Li J M, et al. The Chinese Journal of Nonferrous Metals, 2015, 25(2): 280-292 (in Chinese).
金和喜, 魏克湘, 李建明, 等. 中国有色金属学报, 2015, 25(2): 280-292.
2 Zhou H Y, Shi X L, Lu G C, et al. Surface and Coatings Technology, 2020, 387: 125552.
3 Yang C, Xu W C, Wan X J, et al. Journal of Plasticity Engineering, 2019, 26(2): 69-78 (in Chinese).
杨川, 徐文臣, 万星杰, 等. 塑性工程学报, 2019, 26(2): 69-78.
4 Yang Z S. Aviation precision manufacturing technology, 2002, 38(6): 20-23 (in Chinese).
杨尊社. 航空精密制造技术 ,2002, 38(6): 20-23.
5 Wang J, Lin X, Wang M, et al. Materials Science and Engineering A, 2020, 776: 139020.
6 Herzog D, Seyda V, Wycisk E, et al. Acta Materialia, 2016, 117: 371-392.
7 Li L, Yu Z S, Zhang P L, et al. Transactions of the China Welding Institution, 2018, 39(12): 37-43, II (in Chinese).
李雷, 于治水, 张培磊, 等. 焊接学报, 2018, 39(12): 37-43.
8 Ou W, Wei Y, Liu R, et al. Journal of Manufacturing Processes, 2020, 53: 84-98.
9 Szost B A, Terzi S, Martina F, et al. Materials and Design, 2016, 89: 559-567.
10 Wu S S, Guo C, Liu W M. Modern manufacturing technology and equipment, 2021, 57(3): 2 (in Chinese).
吴随松, 郭纯, 刘武猛. 现代制造技术与装备, 2021, 57(3): 2.
11 Cunningham C R, Flynn J M, Shokrani A, et al. Additive Manufacturing, 2018, 22: 672-686.
12 Yang H O, Wang J, Wang C. et al. Materials reports, 2018, 32(12): 2028-2031 (in Chinese).
杨海欧, 王健, 王冲, 等.材料导报, 2018, 32(12): 2028-2031.
13 Barriobero-Vila P, Requena G, Buslaps T, et al. Journal of alloys and compounds, 2015, 626: 330-339.
14 Kumar R, Hynes N R J. International Journal of Lightweight Materials and Manufacture, 2019, 2(3): 193-205.
15 Malinov S, Sha W, Mckeown J J. Computational Materials Science, 2001, 21(3): 375-394.
16 He Z, Hu Y, Qu H T, et al. Aerospace Manufacturing Technology, 2016(6): 11-16 (in Chinese).
何智, 胡洋, 曲宏韬, 等. 航天制造技术, 2016(6): 11-16.
17 Mereddy S, Bermingham M J, Stjohn D H, et al. Journal of Alloys and Compounds, 2017, 695: 2097-2103.
18 Lin Z D, Song K J, Yu X H. Journal of Manufacturing Processes, 2021, 70: 24-45.
19 Pan Z, Ding D, Wu B, et al. Transactions on intelligent welding manufacturing, 2018: 3-24.
20 Baufeld B, Brandl E, Van der Biest O. Journal of Materials Processing Technology, 2011, 211(6): 1146-1158.
21 Baufeld B, Van der Biest O, Gault R. Materials and Design, 2010, 31: S106-S111.
22 Baufeld B, Van der Biest O, Gault R. Science and Technology of Advanced Materials, 2009, 100(11):1536-1542.
23 Wang F, Williams S, Colegrove P, et al. Metallurgical and Materials Transactions A, 2013, 44(2): 968-977.
24 Wang F D, Williams S, Rush M. International Journal of Advanced Manufacturing Technology, 2011, 57(5):597-603.
25 Aiyiti W, Zhao W, Lu B, et al. Rapid Prototyping Journal, 2006, 12(3): 165-172.
26 Martina F, Mehnen J, Willians S W, et al. Journal of Materials Processing Technology, 2012, 212(6):1377-1386.
27 Lin J J, Lv Y H, Liu Y X, et al. Materials and Design, 2016, 102: 30-40.
28 Spencer J D, Dickens P M, Wykes C M. Proceedings of the Institution of Mechanical Engineers, Part B:Journal of Engineering Manufacture, 1998, 212(3): 175-182.
29 Gou J, Shen J, Hu S, et al. Journal of Manufacturing Processes, 2019, 42: 41-50.
30 Zhang F Q, Chen W G, Tian M J. Rare metal materials and engineering, 2018, 47(6): 6 (in Chinese).
张飞奇, 陈文革, 田美娇.稀有金属材料与工程, 2018, 47(6): 6.
31 Yin H, Huang R F, Cao H J, et al. China Surface Engineering. 2021,34(3): 1-15 (in Chinese).
伊浩, 黄如峰, 曹华军, 等.中国表面工程, 2021,34(3): 1-15.
32 Singh S R, Khanna P. Materials Today: Proceedings, 2021, 44: 118-128.
33 Huang J K, Yuan W, Yu S R, et al. Journal of Manufacturing Processes, 2020, 49: 397-412.
34 Lin Z, Goulas C, Ya W, et al. Metals 2019, 9(6): 673.
35 Lin Z, Ya W, Subramanian V V, et al. The International Journal of Advanced Manufacturing Technology, 2020,111(1): 411-426.
36 Wilson-Heid A E, Wang Z, Mccornac B, et al. Materials Science and Engineering A, 2017, 706: 287-294.
37 Liu Y J, Wang H L, Li S J, et al. Acta Mater 2017, 126: 58-66.
38 Colegrove P A, Donoghue J, Martina F, et al. Scripta Materialia, 2017, 135: 111-118.
39 Wauthle R, Vrancken B, Beynaerts B, et al. Additive Manufacturing, 2015, 5: 77-84.
40 Baufeld B, Brandl E, Van der Biest O. Journal of Materials Processing Technology, 2011, 211(6): 1146-1158.
41 Wu B, Pan Z, Ding D, et al. J Mater Process Technol 2018, 258: 97-105.
42 Ding D, Wu B, Pan Z, et al. Materials and Manufacturing Processes, 2020, 35(7): 1-7.
43 Li G, Qu S, Xie M, et al. Surface and Coatings Technology, 2017, 316: 75-84.
44 Yang Y, Jin X, Liu C, et al. Metals, 2018, 8(11): 934.
45 Gou J, Wang Z, Hu S, et al. Journal of Manufacturing Processes, 2020, 54: 148.
46 Bermingham M J, Kent D, Zhan H, et al. Acta Materialia, 2015, 91: 289.
47 Chen Y, Yang C, Fan C, et al. Materials Letters, 2020, 275: 128170.
48 Gou J, Wang Z, Hu S, et al. Journal of Alloys and Compounds, 2020, 829: 154481.
49 Mereddy S, Bermingham M J, Stjohn D H, et al. Journal of Alloys and Compounds, 2017, 695: 2097.
50 Huang J K, Liu S E, Yu S R, et al. Surface and Coatings Technology, 2020, 381(5): 125141.
51 Huang J K, Chen H Z, Pan W, et al. Materials Today Communications, 2020(24): 101171.
52 Huang J K, Liu S E, Wu L J, et al. Journal of Alloys and Compounds, 2021 857: 157557.
黄健康,男,1981 年生,教授,2005 年本科毕业于湘潭大学获学士学位,2007 年毕业于兰州理工大学获硕士学位,2010 年毕业于兰州理工大学获博士学位。主要从事电弧增材制造、异种金属连接、焊接物理与焊接过程检测与控制等方面的研究,发表论文 200 多篇。
相关链接