钛及钛合金具有耐腐蚀性、比强度高、密度小、熔点高等优点,广泛应用于各行各业,尤其是航空航天行业[1]。但钛和钛合金导电导热性差,可焊性差,因此其应用范围受限。对钛方块、钛环等钛基材表面处理常用的方法是电镀,但钛基材极易与空气中的氧气生成致密的氧化膜,造成钛基材表面难以电镀,镀层结合强度差[2-7]。国内外提高钛表面电镀结合的一般方法是通过酸洗氢化,酸洗除去钛表面的氧化膜,氢化在钛基材表面形成一层氢化膜,或者氟化膜来延缓钛表面生成氧化膜的速度[8-9]。前人曾使用X-射线光电子能谱仪(X-ray photoelectron spectroscopy,XPS)、X-射线衍射仪(X-ray diffractometer,XRD)表征生成的氢化膜[10-12],但是对氢化膜具体的结构研究甚少,也未见氢化膜结构对钛和镀层结合影响的研究。
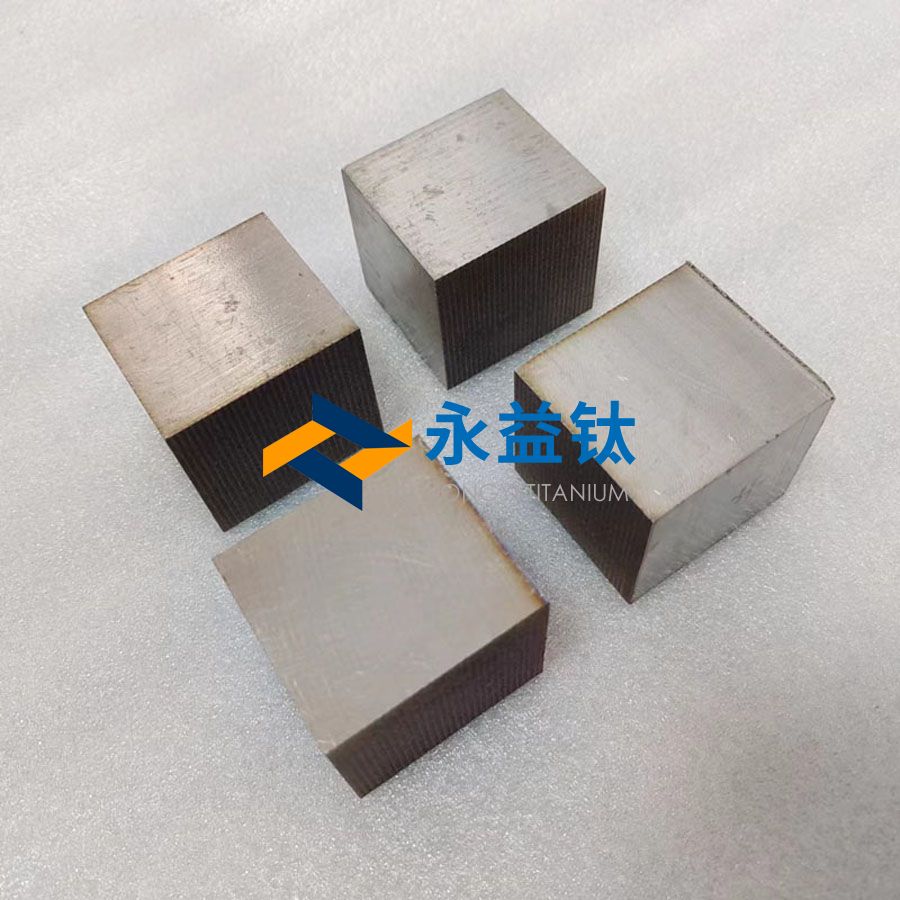
本文用H2SO4和HCl的混合溶液氢化钛材,在钛表面形成氢化膜,用扫描电子显微镜(scanning electron microscope,SEM)研究了氢化膜的微观结构,用XRD分析物质的物相组成;研究电镀初期生成镍的结构特征以及镀层中杂质,分析氢化膜结构对镀层结合的影响。
1、试 验
1.1试验材料和试验过程
试验样品选用长30mm、宽30mm、厚0.2mm的TA2板,本文先用HCl酸洗除去钛板表面氧化膜,再用H2SO4和HCl的混合溶液氢化钛板,然后进行预镀镍,最后电镀铜。酸洗前对样品进行除油。
化学除油用30g/L的NaOH,25g/L的Na2CO3,30g/LNa3PO4作为除油溶液,温度60℃,时间5min。酸洗用50%的HCl除去钛板表面的氧化膜,酸洗时间为15min。氢化选择体积比为1:1的H2SO4和HCl的混合溶液,氢化时间为10、30、50、70min。
预镀镍用130g/L的NiCl2·6H2O和100g/L的HCl作为预镀镍溶液,阳极为镍板,阴极为钛板[13–18]。电流密度为5A/dm2,温度为室温。电镀铜镀液使用200g的CuSO4·5H2O和100g的H2SO4、10g的酒石酸钾钠和0.1g的硫脲配制的混合溶液,采用的电镀工艺是电流密度2A/dm2,时间4min,温度为室温。阳极为磷铜片,阴极为钛板[19-22]。
1.2氢化膜和镀层表征方法
采用D8-ADVANCE型XRD分析钛板氢化前后表面物质的物相组成;
采用PhenomNanoG2型SEM和能谱分析仪分析氢化膜结构、镀镍的形貌以及镀层断口的结构和成分。
1.3镀层结合强度测试方法
采用镀层拉开法(GB/T5210—2006)定量测量电镀铜镀层和基体的结合强度[23–26]。
2、试验结果与讨论
2.1钛表面氢化膜的形成
用H2SO4和HCl的混合溶液氢化钛板表面,然后对氢化前后的表面进行XRD物相分析,结果如图1所示。从图1中可知,钛板氢化后的XRD谱图在35.9°、60.0°、41.0°、71.9°出现新的衍射峰,这些峰对应的物相为TiH2;由于氢化膜很薄,所以衍射峰的强度很弱。
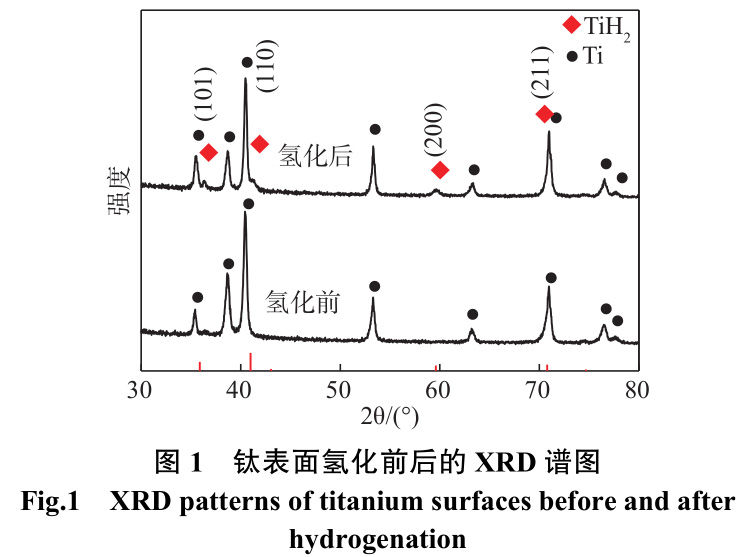
图2显示了氢化前后钛表面的形貌变化。从图2(a)中可以看出,氢化前基体表面有腐蚀的痕迹,表面的氧化膜被除去。而从图2(b)经过1:1体积比的H2SO4和HCl的混合溶液氢化30min后的表面形貌可知,钛表面形成的氢化膜是蜂窝状的孔状结构和氢化之前的结构有明显的区别。图中黄色箭头所指的浅析孔结构直径平均值为0.45μm,而图中氢化膜上红色箭头所指的深析孔直径平均值为0.85μm。
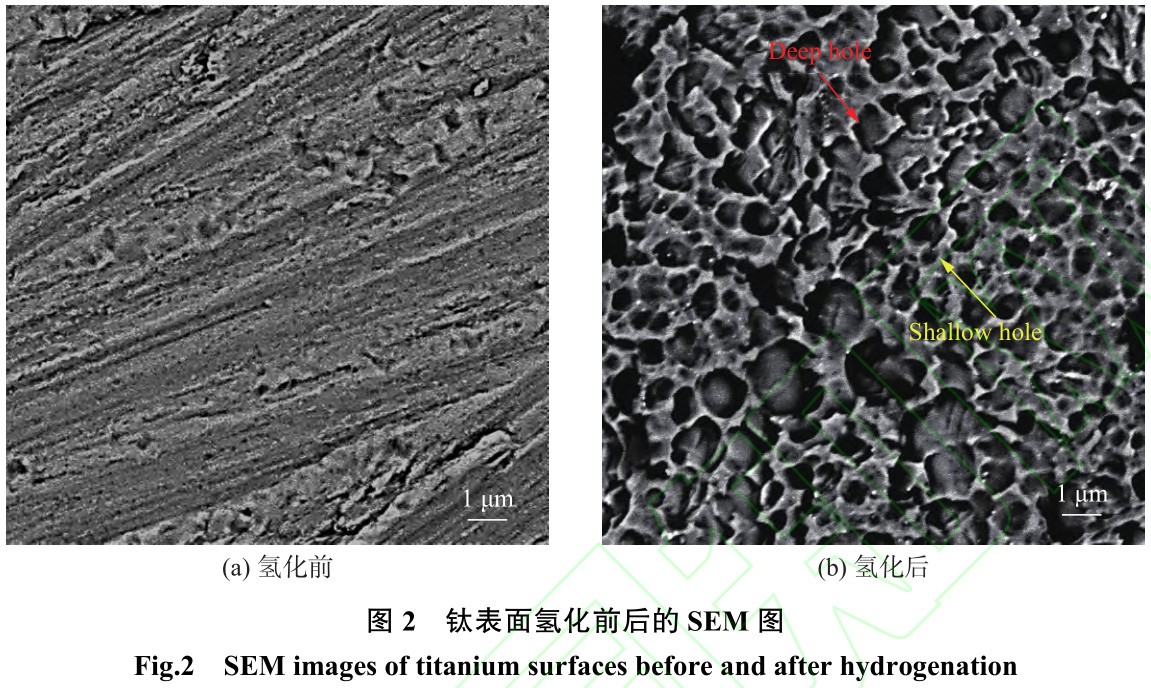
氢化膜呈蜂窝状多孔结构的原因是因为钛和酸的反应过程中会生成H2,如方程式(1)~(5)显示,H2在钛基体上析出,冲破了表面覆盖的氢化膜,造成了氢化膜的多孔结构。氢化过程化学反应方程式如下;
Ti+3HCl=TiCl3+3[H](1)
Ti+H2SO4=TiSO4+2[H](2)
2Ti+3H2SO4=Ti2(SO4)3+6[H](3)
Ti+2[H]=TiH2(4)
[H]+[H]=H2(5)
氢化膜的多孔结构受氢化影响最大,图3显示了H2SO4和HCl混合氢化不同时间后钛表面SEM形貌。图3(a)为氢化10min后的钛基材表面,表明此时钛开始和氢离子反应,生成的H2从钛基体内出来,钛表面开始出现小孔状的结构,但蜂窝状的结构还没形成。图3(b)表明,当氢化时间延长到30min时析出大量的H2,钛表面的孔状结构更加明显,存在明显的蜂窝状结构。图3(c)表明,氢化膜开始溶解,氢化膜结构被破坏,出现大的深孔。图3(d)为氢化70min时钛表面的氢化膜结构,表明氢化膜表面孔的数目减少,孔的直径减小,氢化膜特征慢慢消失。当H2SO4和HCl混合溶液中的氢离子浓度减小时,氢化膜的形成速率小于氢化膜溶解速率时,氢化膜结构开始溶解,氢化膜孔状结构慢慢消失。对比不同氢化时间的SEM图可知,在氢化时间30min时,氢化膜的蜂窝结构特征最显著。
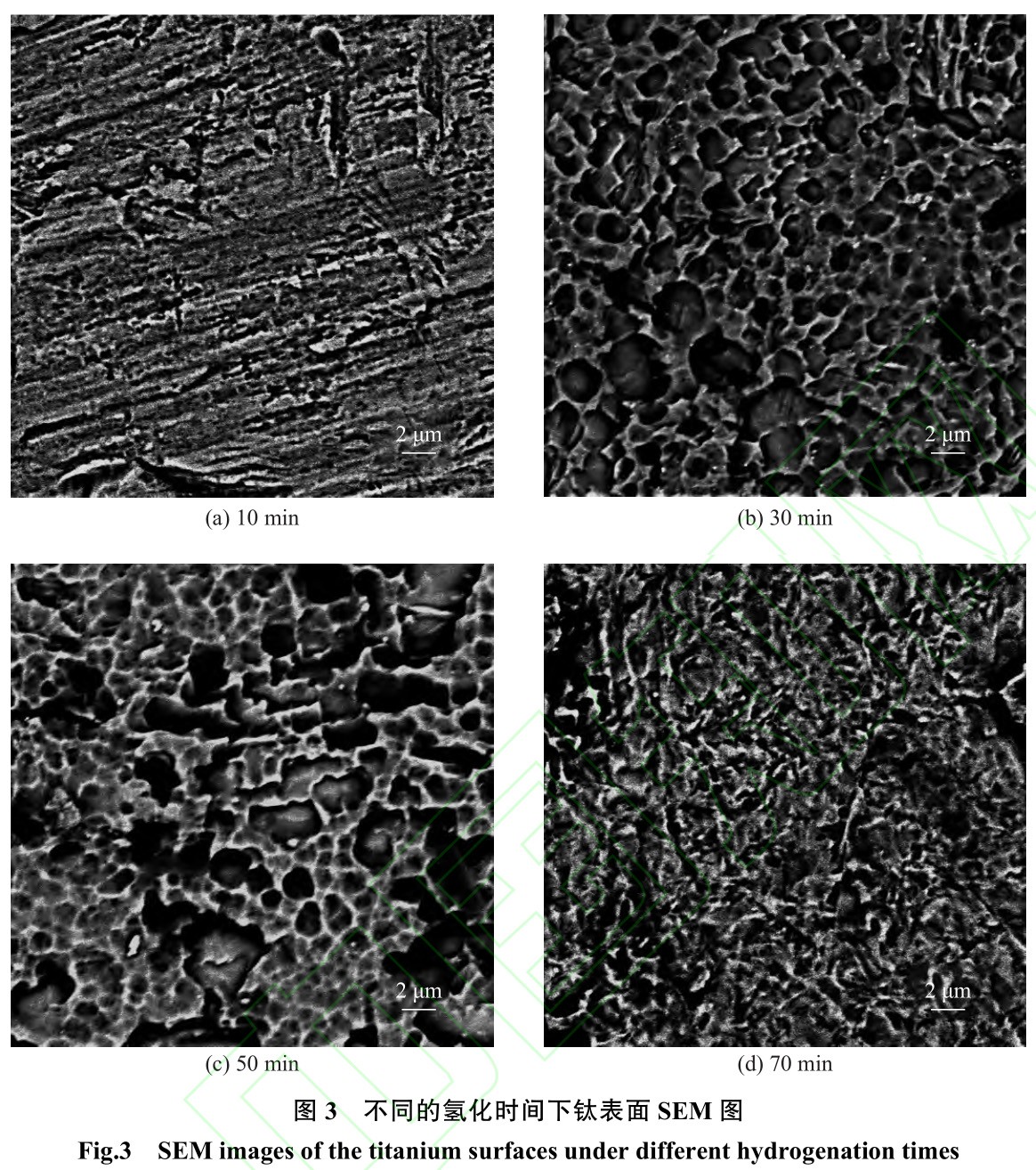
测量了不同氢化时间下氢化膜孔的尺寸,列于表1。从表1可知,随着氢化时间的延长,钛表面析孔的直径也发生改变,氢化时间为30min时,浅析孔直径为0.45μm,深析孔的直径为0.85μm,此时氢化膜蜂窝结构最显著。而氢化时间为50min时,氢化膜开始溶解,表面出现更大的孔。氢化时间为70min时,钛表面的蜂窝状结构慢慢消失。
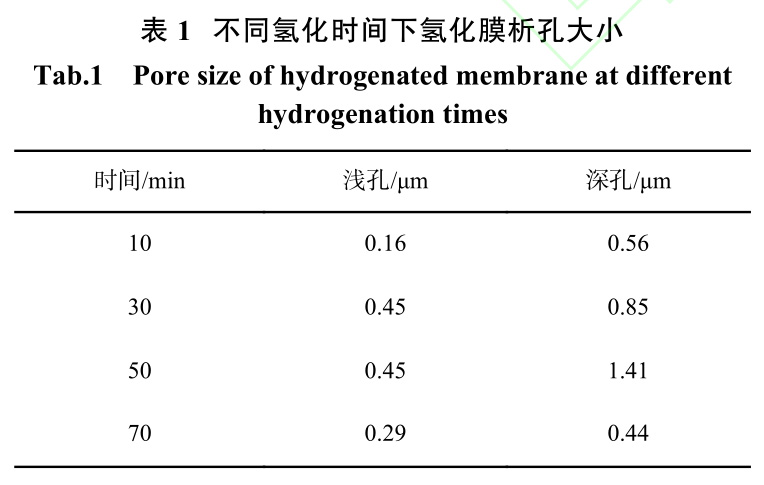
2.2氢化膜对电镀沉积镍、铜的影响
氢化处理在钛基体表面生成一层灰黑色的保护膜,延缓钛基体被氧化,而且氢化膜为导电膜,具有金属键的性质,从而以金属键的形式将钛基体和镀层金属紧密的结合在一起,提高镀层结合强度[27]。
钛表面经过混酸氢化处理后,进行不同时间的预镀镍和电镀铜,用SEM观察沉积的镍镀层和铜镀层的形貌,如图4所示。其中采用镀液温度为室温,电流密度7A/dm2。图4(a)为镀镍10s的镀层形貌。从图4(a)中可以看到,因为电镀时间短,沉积的镍很少,黄色箭头所指的几颗白色的颗粒为镍颗粒,镍颗粒的尺寸很小,直径仅有0.08μm。表面呈现的是氢化膜的蜂窝状多孔状特征结构,测量图4(a)中蜂窝孔的直径平均值约为0.26μm;图4(b)为镀镍30s的镀层形貌,从图4(b)中可以看到,随电镀时间延长,白色镍沉积球明显增多,同时球状镍颗粒尺寸变大,镍球的直径约为0.17μm。从图4(b)中还可以发现,镍存在两种沉积位置:一种是在氢化膜孔内和表面,呈现白色颗粒;而另一种生长位置是在氢化膜孔的边棱上面,随着电镀时间的延长会生长成中空镍管。图4(c)为镀镍60s的镀层形貌,随着预镀镍时间的增加,镍球继续长大直径变为0.22μm,氢化膜析孔棱上的镍晶粒则继续生长,形成特征更明显的中空镍管,此时镍管的直径为0.25μm。镍管的直径大小和图4(a)中氢化膜蜂窝孔的直径0.26μm接近。图4(d)为镀镍120s的镀层形貌,此时白色球状镍的直径增大为0.23μm,而镍管的大小为0.24μm,图中镍颗粒更加致密和均匀。图4(e)为镀镍180s的镀层形貌,随着电镀时间的延长,晶粒开始不均匀沉积,镍球的直径变化不大,直径为0.22μm,镍管的直径增大为0.24μm,镀层颗粒致密程度不均匀。图4(f)为预镀镍180s后镀铜240s的镀层形貌,铜晶粒在镍层上继续生长,上层镀层成为更致密的镀层结构,但镀层中仍存在中空管状结构,减弱了镀层和氢化膜之间的结合。
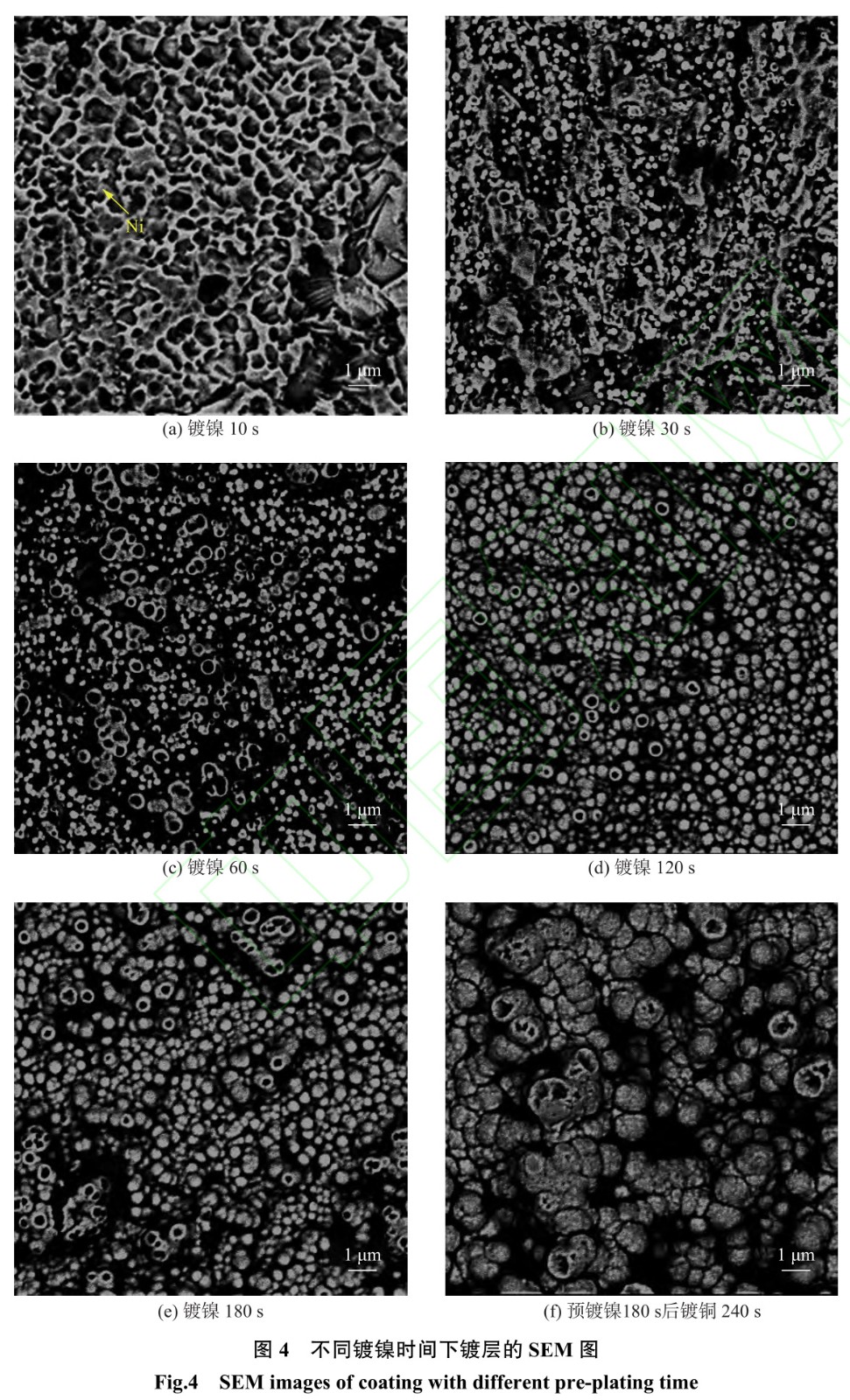
测量不同预镀镍时间镍球和镍管的直径大小,结果列于表2。从表2可以看到,随着预镀镍时间的延长,镍球的直径一直增大;而镍管的直径大小保持在0.24~0.25μm,不受预镀镍时间的影响,镍管的直径和氢化膜的析孔直径0.26μm接近,因此可以推测镍管是由氢化膜特殊的蜂窝状结构而形成的。
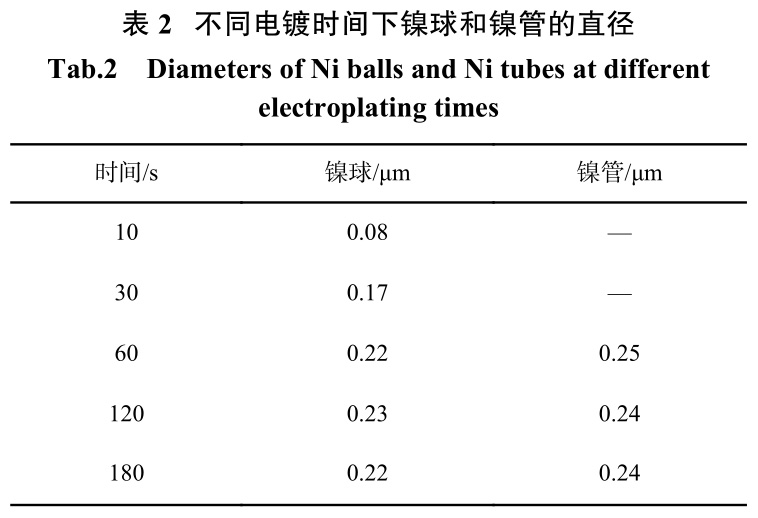
2.3氢化时间对电镀铜镀层结合强度的影响
图5为氢化时间对钛基体电镀铜镀层结合强度的影响。从图5中可以看到,没有氢化处理时镀层结合强度最差,仅有0.1MPa,经过氢化处理后,镀层结合强度大幅度提高。镀层结合强度随着氢化时间的延长,先增大后降低,在氢化30min时,镀层结合强度达到最大值为9.6MPa,说明有无氢化处理对镀层结合强度影响最大;而随着氢化时间的延长,镀层结合强度略微下降。
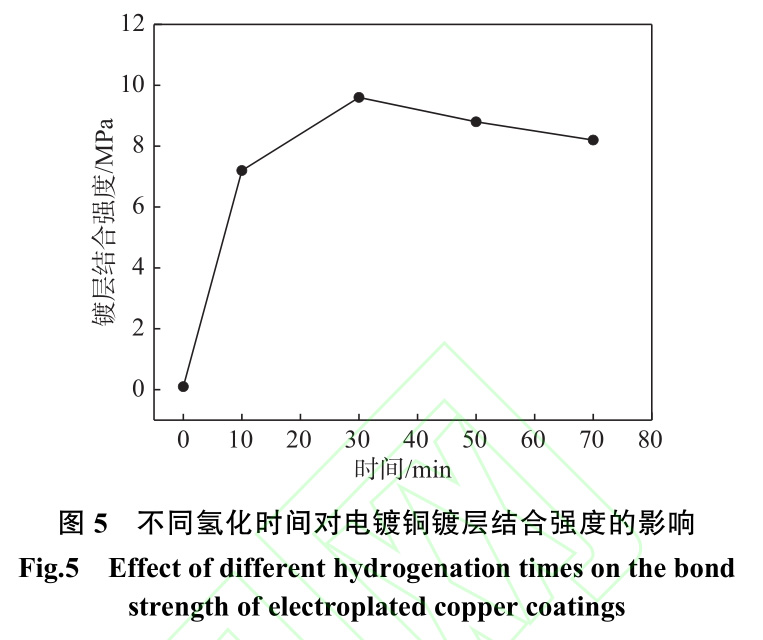
2.4镀层拉开断口分析
将镀层和基体拉开,观察拉开后的镀层断面,图6(a)为镀层拉开面的镀层断面形貌。从图6(a)可以看出,拉开部分形貌为多孔结构,和氢化膜多孔结构一致。图6(a)中黑色多孔状物质,经过图6(b)EDS分析可知,其主要元素为Ti,由于Ti基体强度高,极难把基体Ti拉断,而氢化形成多孔的氢化膜结构,在镀层拉开的过程中更有可能被拉开,因此出现了图6(a)中黑色部分即氢化膜部分。图6(a)中白色的物质为镍镀层,观察发现镍镀层多孔且存在空隙,而多孔的镍镀层正是由于多孔的氢化膜结构而形成的。在受力拉开时,中空的镍管也被拉断,形成了白色镍镀层。
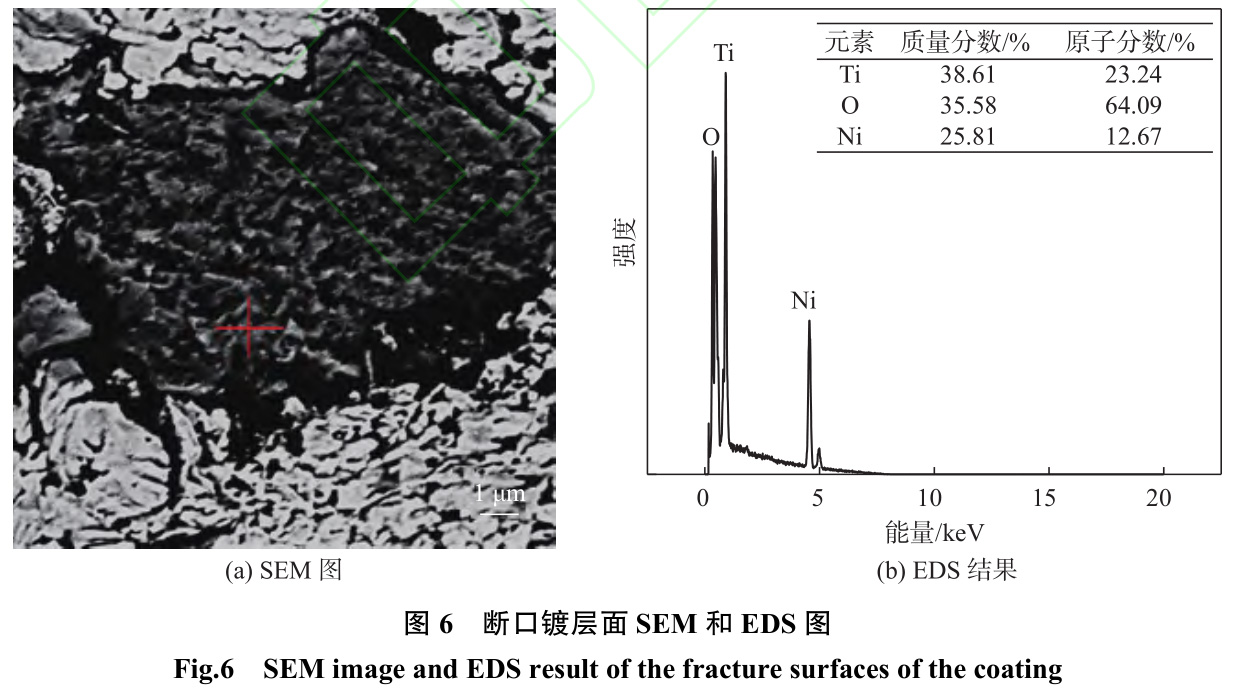
断口钛基体侧的形貌示如图7所示。从图7中可以看出,表面有很多白亮物质,经过能谱分析,可知白色物质为镍。镍呈现出孔状形貌可以推断是中空镀层在拉伸的过程中出现断裂,在钛基体上才会存留镍晶粒。从图中可以看出断裂的位置在镍管的根部,氢化膜析孔的棱上。这是因为随着镀镍时间的增加,上层堆积的镍和铜晶粒开始变得致密,而底层保留了多孔结构,没有生成致密的镀层,因此受力拉开时镀层先在镍底层稀疏的根部断裂。图7(a)钛基体孔内黑色杂质,经图7(b)EDS能谱分析可知,孔洞内黑色杂质含有很高的S元素,证明氢化的过程中产生的硫酸盐以及镀液组分,作为杂质聚集残存在氢化膜的孔内,杂质的存在会影响镍和氢化膜的结合,造成镀层结合强度减弱。
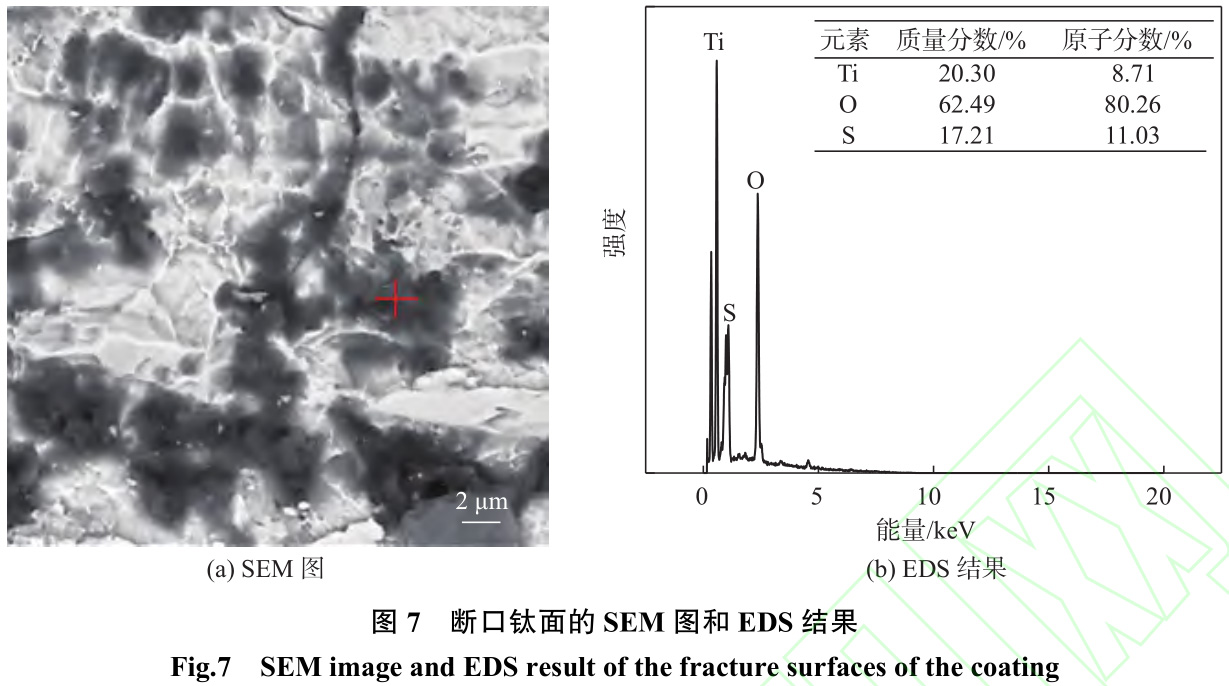
3、结 论
(1)钛经H2SO4和HCl混合溶液处理后表面形成蜂窝状多孔的氢化膜,氢化膜短暂保护基体不被氧化,有助于电镀层的沉积和结合,提高了镀层结合强度,镀层结合强度最大值为9.6MPa。
(2)孔状氢化膜的结构导致了氢化后沉积出不同的镍形状,一种情况是电镀镍颗粒生长在氢化膜孔边棱上,最后变成中空的镍管;另一种情况是生长在氢化膜孔内和氢化膜的表面平坦位置形成镍球。
(3)多孔的氢化膜结构还造成了氢化过程产生的硫酸盐以及镀液残留,被镀层覆盖,在镀层底部形成杂质。
(4)蜂窝状的氢化膜、中空镍管以及杂质残留,成为了镀层结构中的最薄弱层,造成了镀层强度的降低,影响了镀层和基体的结合。氢化膜的形成一方面实现了钛上电镀,但另一方面氢化膜的多孔结构又在一定程度上限制了镀层结合强度的提高。

参考文献:
[ 1 ]李蒙, 凤伟中, 关蕾, 等. 航空航天紧固件用钛合金材料综述 [J]. 有色金属材料与工程, 2018, 39(4): 49−53.
[ 2 ]SUTTER E M M, GOETZ-GRANDMONT G J. The behaviour of titanium in nitric-hydrofluoric acid solutions[J]. Corrosion Science, 1990, 30(4-5): 461−476.
[ 3 ]ZAIMAH N, HUSSAIN M S, MASRUR L. The effects of solution movement to the microstructure and size of nickel plating on titanium surface by high speed direct nanocrystalline plating[J]. Applied Mechanics and Materials, 2013, 465–466: 867–871.
[ 4 ]IZMAN S, KADIR M R A, ANWAR M, et al. Effect of pickling process on adhesion strength of Ti oxide layer on titanium alloy substrate[J]. Advanced Materials Research, 2010, 146–147: 1621–1630.
[ 5 ]BARAKA A M, HAMED H A, SHAARAWY H H.Electrodeposition of rhodium metal on titanium substrates[J]. Anti-Corrosion Methods and Materials,2002, 49(4): 277−282.
[ 6 ]VON GUTFELD R J, WEST A C. Copper plating on titanium alloy 6-2-4-2 using an in situ high voltage pulse followed by plate-up[J]. Journal of Applied Electrochemistry, 2008, 38(4): 531−536.
[ 7 ]孙志华, 刘佑厚, 张晓云, 等. 钛及钛合金的电镀工艺述评 [J]. 腐蚀与防护, 2005, 26(11): 493−496.
[ 8 ]屠振密, 朱永明, 李宁, 等. 钛及钛合金表面处理技术的应用及发展 [J]. 表面技术, 2009, 38(6): 76−78,86.
[ 9 ]王鸥, 贾亚洲. 钛合金电镀前处理工艺应用研究 [J]. 航空制造技术, 2015, (17): 110−113.
[10]沈志超, 谢发勤, 吴向清, 等. TC4 钛合金铜镀层的性能 [J]. 中国表面工程, 2012, 25(5): 45−49.
[11]于海, 李云飞, 王志煜, 等. TC2 钛合金电镀铜的应用[J]. 腐蚀与防护, 2015, 36(5): 432−434.
[12]李萌初, 屠振密, 张景双, 等. 钛上直接电镀机理的研究 [J]. 材料保护, 1991, (11): 12−14,3.
[13]朱万宇, 黄皓, 史青青. 前处理工艺对热处理后 301 不锈钢镀镍结合力的影响 [J]. 电镀与涂饰, 2021, 40(17):1332−1335.
[14]李红双, 高玉飞, 葛培琪, 等. 电镀金刚石线锯氨基磺酸盐 预 镀 镍 工 艺 [J]. 电 镀 与 涂 饰 , 2019, 38(21):1152−1155.
[15]赵林, 杨中东, 薛向欣, 等. 钛合金化学镀镍工艺 [J]. 电镀与涂饰, 2006, 25(4): 38−41.
[16]HUSSAIN M S. Direct Ni-Co alloy plating of titanium alloy surfaces by high speed electrodeposition[J]. Transactions of the IMF, 2012, 90(1): 15−19.
[17]OUYAN C, ZHANG X L, WU M F, et al. Physical and electrochemical properties of Ni-P/TiN coated Ti for bipolar plates in PEMFCs[J]. International Journal of Electrochemical Science, 2020, 15(1): 80−93.
[18]江星新, 卢耀军, 李欣彤, 等. 脉冲电镀 Ni 镀层参数影响及耐腐蚀机理 [J]. 有色金属科学与工程, 2022,13(1): 52−59.
[19]杜继红, 鞠鹤, 蔡天晓, 等. 钛上电镀铜工艺对镀层性能的影响 [J]. 材料保护, 2000, (12): 16−17.
[20]NING Z H, HE Y D. Rapid electroplating of Cu coatings by mechanical attrition method[J]. Transactions of Nonferrous Metals Society of China, 2008, 18(5):1100−1106.
[21]LI J H, DESHPANDE P, LIN R Y. Infrared heat treatment of Ti-6Al-4V with electroplated Cu[J]. Journal of Materials Engineering and Performance, 2004, 13(4):445−450.
[22]LU C H, YANG Y L, CHEN C P, et al. Adhesion properties of electroplating process between polyimide and metal layer for polymer/metal hybrid bonding[J].IEEE Transactions on Components, Packaging and Manufacturing Technology, 2020, 10(1): 168−175.
[23]杨班权, 陈光南, 张坤, 等. 涂层/基体材料界面结合强度测量方法的现状与展望 [J]. 力学进展, 2007, 37(1):67−79.
[24]刘强, 范晓东, 宋生印, 等. 钛合金油管表面抗粘扣处理工艺研究 [J]. 石油管材与仪器, 2017, 3(4): 26−31.
[25]李浩. 钛合金化学镀镍制备工艺及结合力研究 [D]. 沈阳: 东北大学, 2019.
[26]郑小玲, 游敏. 拉伸法测定涂层界面强度的适用性研究 [J]. 粘接, 2003, 24(2): 7−9.
[27]张景双, 李萌初, 杨哲龙, 等. 钛材表面生成“活性膜”的研究 [J]. 电镀与环保, 1993, (5): 3−4,1.
相关链接