钛合金具有高比强度、耐高温、耐腐蚀等优异的性能,已广泛应用于航空航天、兵器、汽车、能源、生物医疗及体育用品等领域[1-2]。超声波检测作为一种重要的无损检测手段,广泛应用于钛合金产品的生产和检验,相关国标和国军标中都规定了超声波检测要求。除了对单体缺陷和连续缺陷的尺寸进行限制,对钛合金超声波底波衰减也进行了明确规定。特别是要求较高的军用产品,对超声波杂波水平也提出了很高的要求。例如,在GJB494A—2008《航空发动机压气机叶片用钛合金棒材规范》中,要求静子叶片用小规格棒材(φ≤45mm)的超声波检测杂波水平不大于φ0.8-9dB,转子叶片用棒材杂波水平不大于φ0.8-12dB。
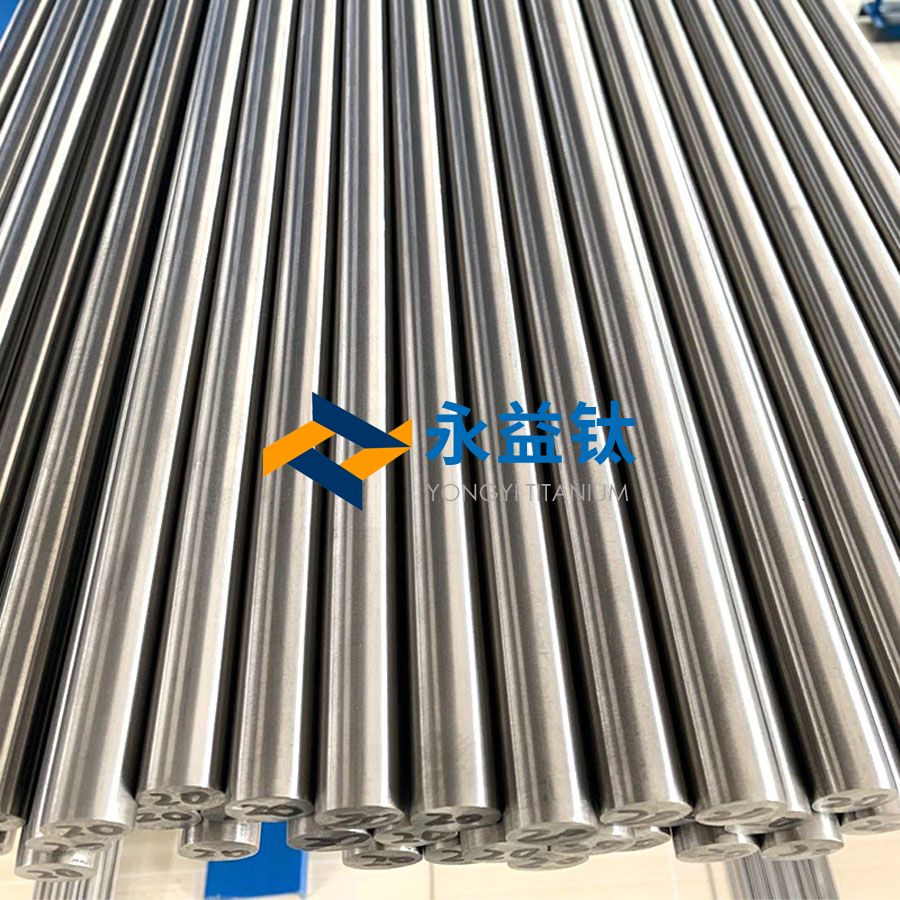
在生物医疗领域,医用钛合金超声刀广泛应用于外科手术。超声刀的超声波波速不仅需要控制在一定范围,而且波速波动值越小越好[3-4]。
然而,钛合金产品由于成分和加工工艺的差异,其微观组织千差万别。复杂的多相多晶结构,以及晶粒取向的差异性,导致不同钛合金产品的超声行为截然不同。影响钛合金产品超声波信号的因素包括超声检测方法(接触法、水浸法等),超声波探头频率,钛合金的表面粗糙度、显微组织类型、晶粒尺寸和形状、织构类型和强度、残余应力等[5-14]。然而,钛合金产品在冷热加工过程中,无法满足各部位的均匀变形,这也造成了钛合金产品不同部位的组织和织构存在差异。因此,当超声波检测时出现杂波水平增大、底波强度衰减等异常信号时,判定其准确来源存在一定的难度。
为了深入研究钛合金组织和织构对超声波检测信号的影响,科研人员排除硬件设备、表面粗糙度、内部缺陷的干扰,对超声信号异常区域进行组织和织构分析[5-9]。本文介绍了超声波在钛合金中的传播、反射和衰减行为,针对超声波波速变化、底波衰减、杂波水平3种常见的超声波检测信号,详细论述了钛合金组织和织构对超声波影响的规律和机理。
1、钛合金中超声波波速的影响因素
超声波的波速与介质的弹性模量和密度密切相关。由于钛的晶体结构为密排六方结构,当超声波在钛合金中传播时,其传播速度会受到弹性模量各向异性的影响。对于钛单晶,密度为ρ=4.507g/cm3,弹性模量张量的分量分别为


超声波在钛单晶中的纵波波速分别为:
c 轴方向
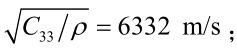
垂直于c轴方向

由此可见,超声波在不同取向的钛晶粒中传播速率不同,理论波速差高达329m/s[9]。
对于多晶钛材料中的超声波波速,不仅需要考虑弹性模量各向异性的影响,还需要考虑材料宏观织构的影响。
Zheng等人[16]表征了φ260mm大规格Ti6242s合金棒材的组织和织构,并对棒材横截面进行水浸超声波波速检测,计算了沿直径方向的波速数据。
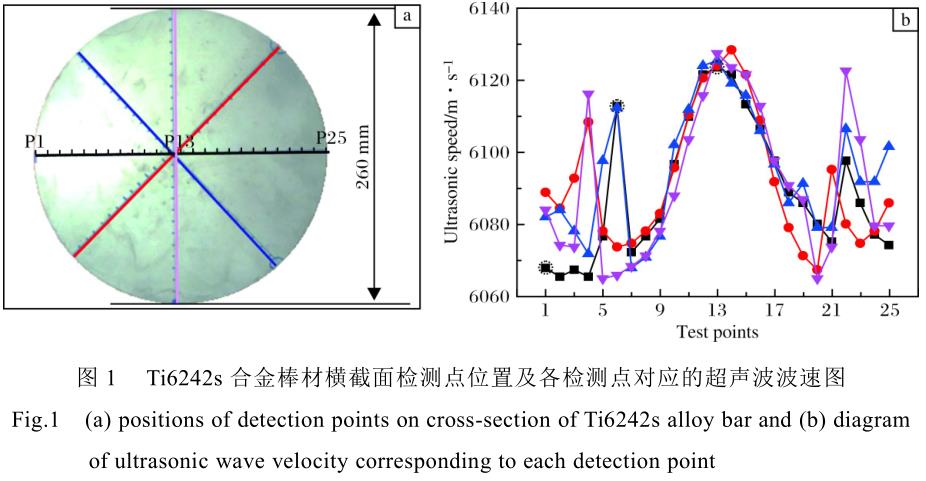
图1a展示了超声检测样品和检测点,沿直径方向每间隔1cm取一个检测点,在每条直径上取25个检测点,沿4个直径方向呈“米”形进行超声波波速检测。图4b展示了4个方向上各检测点的超声波波速数据,4条曲线显示出相同的变化趋势。棒材边部检测点(P1-3;P23-25)波速较低,接着波速会出现一次突然起落变化,然后逐渐增加,在棒材中心位置(P13)达到最大值。图1b中波速低值和高值的特征点位(图中黑色圆圈检测点)分别对应图1a中样品直径方向黑色线上的检测点P1、P6、P7、P13,对其进行XRD宏观织构检测,各检测点(002)晶面的极图数据如图2所示。P1和P7检测点的极密度值分别为1.52和1.99,与其较低的超声波波速一致。而P6和P13检测点的极密度值分别为2.89和7.91,对应较高的超声波波速。
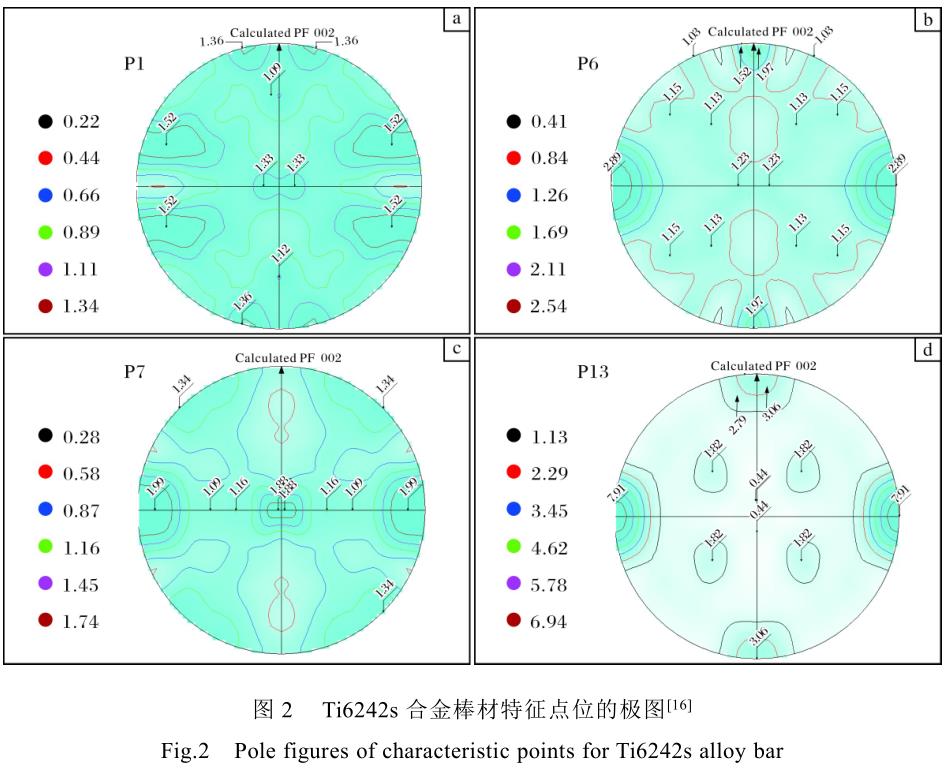
对于通过液压机锻造加工的大规格钛合金棒材,由于变形速率较慢,压力可以传导至棒材内部,变形往往集中在棒材心部(P13),造成心部的极密度值远大于其他部位。大规格棒材在最后使用模具归圆的过程中,由于变形量很小,往往变形集中在次表面(P5-P7)附近。而棒材边部受到温降的影响,流变抗力增加,变形量相对较小。变形量的差异造成大规格棒材各处的极密度值差别较大,因此大规格钛合金棒材的超声波波速沿直径方向呈现三峰结构。
除了织构会对钛合金的超声波波速产生影响,显微组织也会对超声波波速产生影响。钛合金显微组织的类型和形态与加工工艺以及热处理制度有关,显微组织的变化会影响材料的弹性模量,进而影响超声波波速。
韩飞孝等[3]研究了TC4钛合金轧制棒材的加工工艺和热处理工艺对超声波波速的影响。在940℃轧制的棒材,变形量由69.14%增加至92.89%时,超声波波速从6136m/s降至6093m/s;轧制温度从900℃升高至980℃时,超声波波速从6110m/s提高到6162m/s。李运等[4]研究了精锻温度、变形量及热处理制度对Ti7Al4Mo合金棒材超声波波速的影响。研究发现,随着变形温度的升高,棒材初生α相含量逐渐降低,而超声波波速逐渐增大。
2、钛合金中超声波杂波水平的影响因素
2.1超声波在钛合金中的传播规律
超声波从一种介质传播到另一种介质时,在两种介质的界面处会发生反射和透射。第一介质和第二介质界面处的声强反射率R可以表示为:

式中,Z1和Z2分别为两种介质的声阻抗。声阻抗Z与介质密度ρ和超声波纵波波速c有关,可以表示为:

其中,超声波纵波波速又与材料的弹性模量密切相关。对于六方结构钛合金,弹性模量的各向异性导致不同取向区域(或晶粒)的波速和声阻抗存在差异,进而造成区域界面(或晶界)处发生发射,超声探头接收到的这些反射信号即显示为杂波[5,9]。
另外,影响杂波水平的一个关键因素是反射界面的大小。对于钛合金超声检测常用的探头,频率一般为5MHz或10MHz,其对应的超声波波长分别为1.2mm和0.6mm。如果钛合金的晶粒尺寸在几十微米量级,其晶界反射界面的尺寸远小于超声波波长,界面处的反射很小,可以忽略不计。而当晶粒大小与超声波波长在同一量级时,界面处的反射增强,超声波杂波强度增大。
2.2钛合金组织和织构对超声波杂波水平的影响
一般情况下,钛合金经过热加工变形使晶粒细化后,超声波杂波水平会得到改善。然而,在实际生产中,往往会出现随着变形量的增加,杂波水平异常升高的现象,这与变形引起的晶粒形态和织构变化有关。
Thompson等人[6]研究了Ti6246合金微观组织对超声波杂波水平的影响,并建立了通过超声波杂波数据获得材料品质因数的模型。Li等人[11]研究了多晶材料中晶粒形状和织构与超声波背散射的关系,建立了具有织构化椭圆形晶粒的多晶材料超声背散射模型。Humbert等人[9]研究了IMI834钛合金盘件高杂波区(HBA)和低杂波区(LBA)的织构。如图3所示,在高杂波区,六方晶粒的c轴沿饼材直径方向排列的比例高达35%,这些相同取向的晶粒形成了一个晶格取向相同的晶粒群,称之为“宏区”。当超声波穿过宏区时,由于宏区内各晶粒的声阻抗基本一致,超声波会将其视为一个“大型”晶粒,并在宏区的界面处发生反射,导致杂波强度增大。
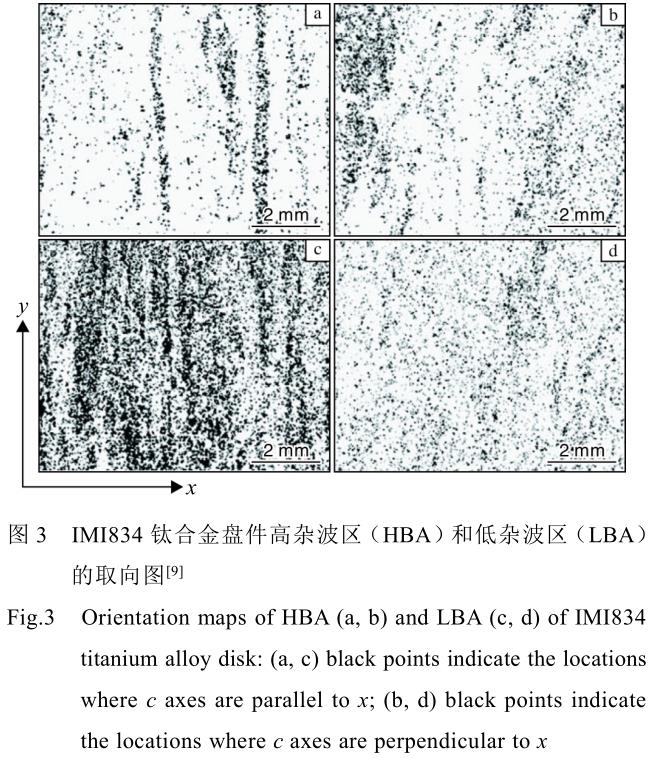
在钛合金生产中,加工工艺–组织和织构–超声波杂波水平之间有着紧密的联系。李磊等人[17]对叶片用小规格TC4钛合金径锻棒材的组织和织构进行分析得到了棒材心部和边部的反极图(IPF图),如图4所示。从图4可以看出,棒材边部和心部的组织和织构存在明显差异。这是由径锻加工特殊的变形方式造成的。棒材径锻过程中,4个锻锤高速往复锤击棒材,棒材受到冲击载荷快速变形。由于冲击载荷主要作用于样品边部区域,且会产生切向应力,边部晶粒迅速破碎,并沿轴向被拉长,形成强烈的{0001}<1010>板织构。心部区域的晶粒虽然也得到细化,但是锤击产生的冲击载荷不易传导至心部,变形量相对边部较小,晶粒尺寸也比边部大。而且心部区域在各个方向的受力基本一致,因此形成了<1010>//轴向的丝织构。
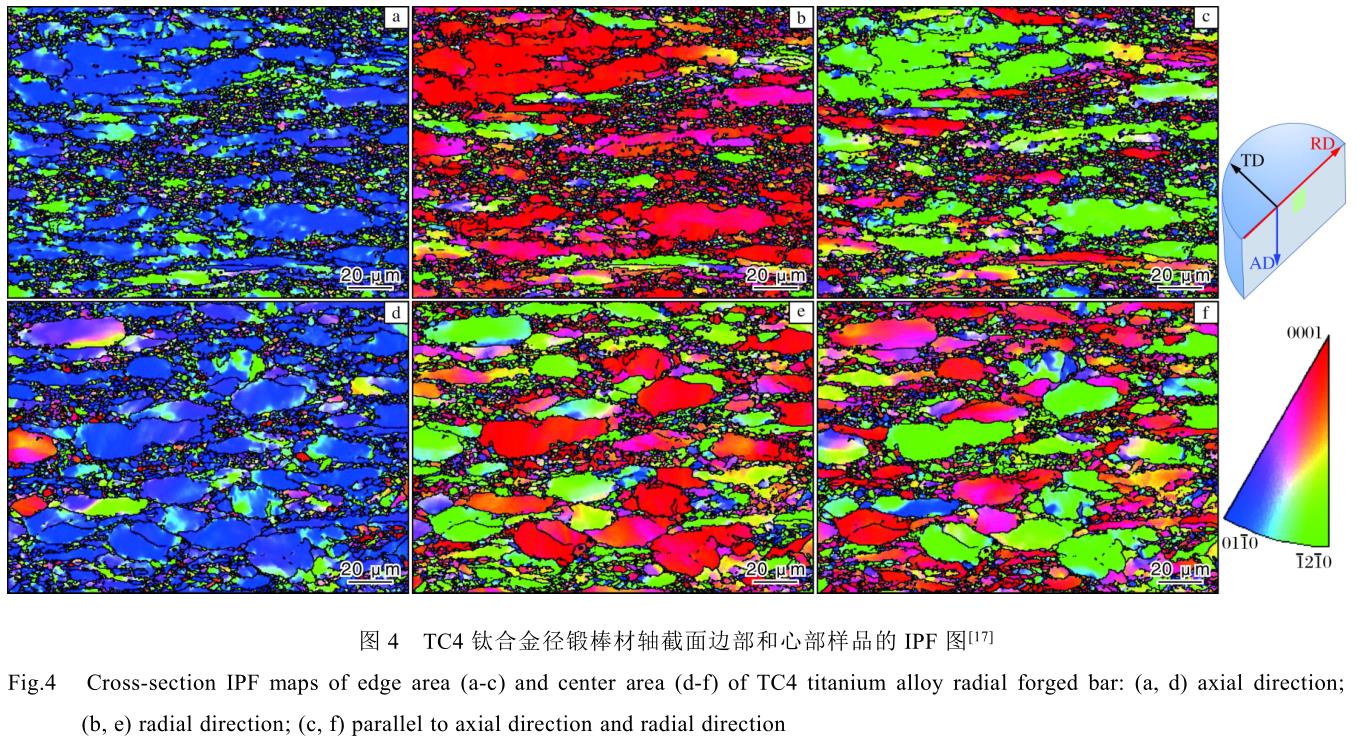
TC4钛合金径锻棒材的这种梯度组织和织构特征造成超声波杂波的异常信号。图5为TC4钛合金径锻棒材水浸超声波检测的A扫图,可以看出在22~30mm范围内(棒材R/2到周面区域)出现了杂波强度异常增大现象。
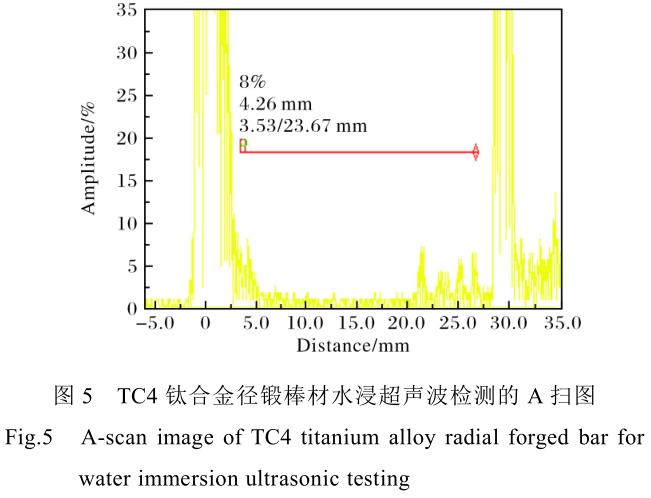
对于异常的超声波杂波信号,不仅需要分析材料的组织和织构,还需要结合材料加工的方式和工艺,才能理解其产生机理。该异常区域对应棒材的边部,其晶粒尺寸相对心部更加细小。杂波强度增加是由于边部晶粒被拉长,以及强织构导致的宏区效应,造成超声波反射增强,杂波水平超过指标要求。通过增加径锻温度、缩短径锻坯料长度等方法可以优化棒材的织构分布,降低超声波的杂波水平,满足指标要求[18]。
3、钛合金中超声波底波衰减的影响因素
引起超声波底波衰减的主要原因有波束扩散、介质吸收和晶粒散射。扩散衰减与钛合金样品探测方向的长度有关,超声波的声压与长度的平方根成反比,介质吸收与质点间的内摩擦和热传导有关。散射衰减指超声波在钛合金中传播时,遇到声阻抗不同的界面产生散乱反射而引起的衰减。散射衰减与钛合金的组织和织构密切相关,一般情况下,晶粒粗大时,散射衰减比较严重,被散射的声波形成杂波造成信噪比下降,可能会淹没缺陷信号[19-20]。
韩飞孝等人[18]研究了热加工工艺对TC4钛合金棒材组织和超声波杂波的影响。对文献[18]中西部超导材料科技股份有限公司在940℃通过径锻(1#)和轧制(2#)制备的φ30mmTC4钛合金棒材的横截面进行超声波底波强度C扫描和织构检测,结果如图6、图7所示[17]。
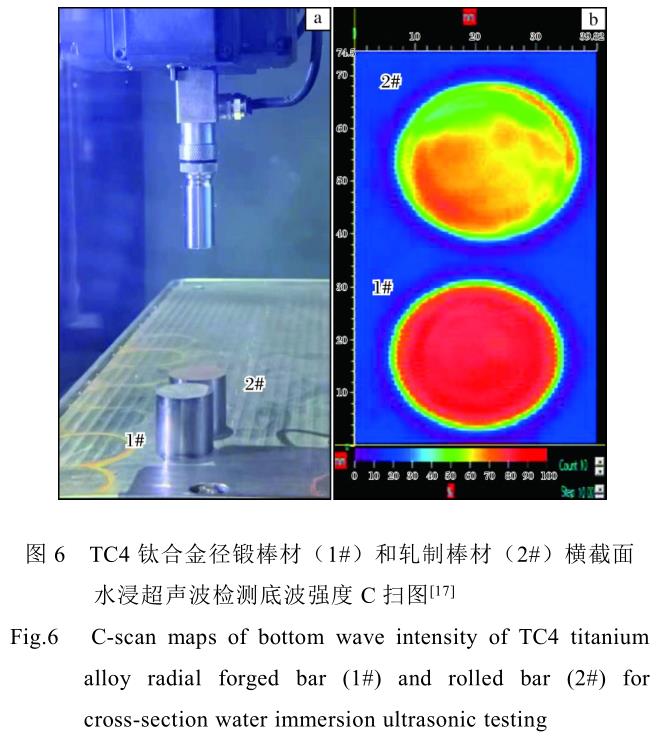
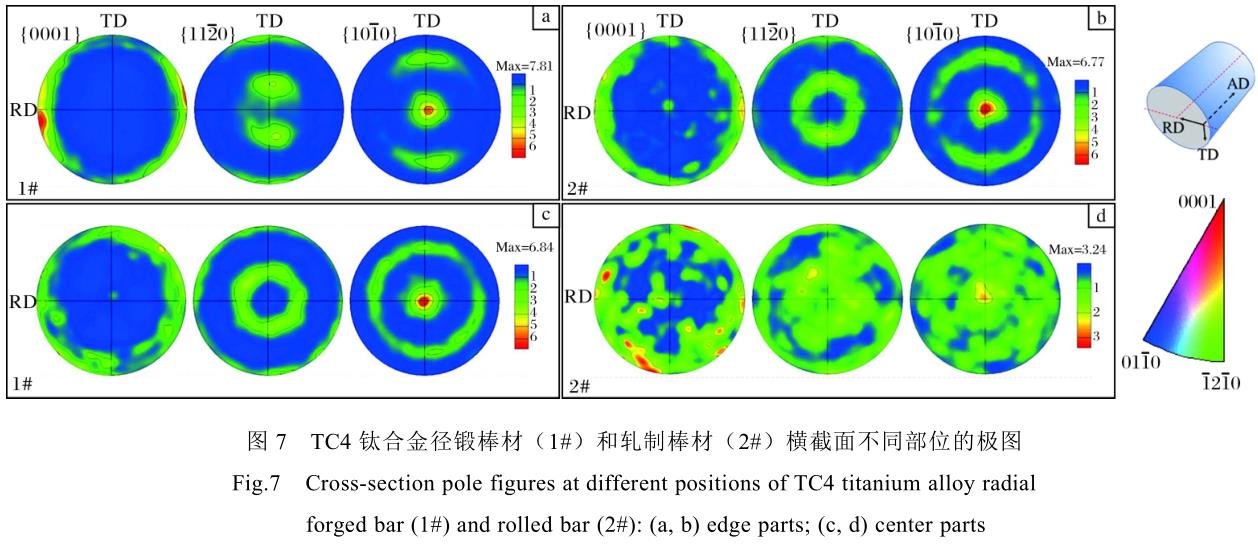
从图6可见,径锻棒材的底波强度在各个方向基本一致,且变化较小;轧制棒材的底波强度出现了明显的各向异性,且心部与边部的强度相差较大。根据图7中2种棒材边部和心部的极图可知,径锻棒材边部与心部的极密度分别为7.81和6.84;轧制棒材边部与心部的极密度分别为6.77和3.42。由此可见,在显微组织相近的情况下,由于加工方式造成的TC4钛合金棒材不同部位的织构差异对超声波的底波衰减有明显的影响。
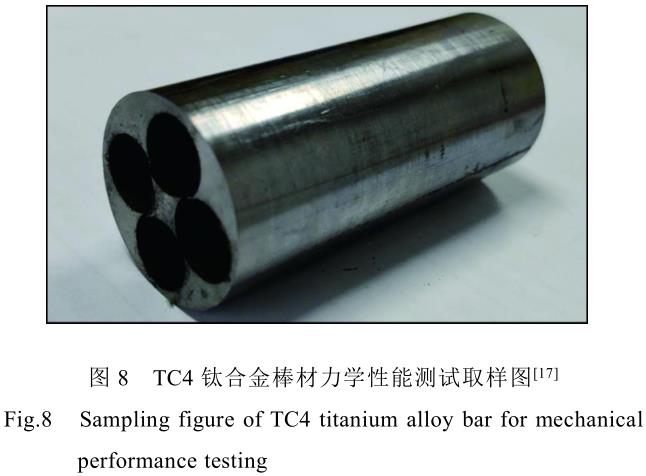
按图8所示在TC4钛合金径锻棒材和轧制棒材上沿轴向取样进行力学性能测试。径锻棒材抗拉强度和屈服强度的变异系数分别为0.24%和0.29%;而轧制棒材的变异系数分别为0.33%和0.49%。轧制棒材的力学性能波动相对较大,这与其超声波底波强度明显的各向异性一致。
4、钛合金超声波检测技术研究进展
钛合金的组织和织构对其力学性能和疲劳性能有显著影响[21-22]。钛合金中的织构宏区,特别是包含高比例c轴与受力方向一致的α相宏区,已经被确认为导致钛合金零部件过早失效的疲劳损伤累积区。超声波检测作为一种无损检测方法,成为钛合金关键零部件织构宏区检测的重要手段,近年来超声波织构的检测技术也取得了很多重要进展。
Moreau等人[23]提出了一种基于超声波波速波动的空间自相关函数的无损检测方法,能够定量表征钛合金宏区的大小。利用该方法检测IMI834钛合金中的织构宏区,其结果与EBSD的测试结果一致。Lan等人[24]通过理论计算和实验研究,提出了一种具有代表性的体积元方法,能够检测两相结构钛合金织构对超声波波速的影响,进而甄别织构宏区。之后,Lan等人[25-26]又提出了一种利用共振超声光谱(RUS)对织构进行无损评估的方法。将多晶区域的定向波速与其织构建立联系,并采用RUS通过测量弹性常数来获得
波速数据以判定材料的织构。Du[27]研究发现,模式转换超声散射的振幅高度依赖于微观组织的各向异性,并利用模式转换超声散射技术表征了Ti-6Al-4V合金坯料低散射和高散射区域的微观组织。模式转换超声散射法提供了一种表征微观组织各向异性的无损检测方法,可作为质量控制的无损检测方式。
5、结语
钛合金中超声波的传播受到密排六方结构晶体弹性模量各向异性的影响,使得超声波的波速、底波衰减以及超声波杂波信号与钛合金产品的组织和织构密切相关。通过对超声波信号的细致分析,能够判断钛合金产品复杂的微观结构以及织构特征,并结合钛合金加工过程分析异常超声波信号产生的原因,通过改进加工工艺使其满足钛合金相关标准。近年来开发的钛合金超声波检测技术有织构宏区的定量表征方法、共振超声光谱无损评估方法以及模式转换超声散射技术等,并已应用于航空航天等领域钛合金零部件的无损检测。
参考文献References
[1] 赵永庆, 葛鹏, 辛社伟. 近五年钛合金材料研发进展[J]. 中国材料进展, 2020, 39(Z1): 527-534.
[2] 赵秦阳, 陈永楠, 徐义库, 等. 钛合金材料低成本化制备技术 进 展 与 展 望 [J]. 中 国 有 色 金 属 学 报 , 2021, 31(11):3127-3140.
[3] 韩飞孝, 孙小平, 楼美琪, 等. 轧制和热处理工艺对 TC4 钛合 金棒 材 超 声声 速 的影 响 [J]. 钛 工业 进 展, 2023, 40(6):16-21.
[4] 李运, 韩飞孝, 秦立东, 等. 加工工艺对 Ti7Al4Mo 合金棒材 组 织 性 能 和 超 声 声 速 的 影 响 [J]. 钛 工 业 进 展 , 2022,39(6): 18-23.
[5] 李华, 马英杰, 邱建科, 等. TC4 钛合金显微组织对超声波探 伤 杂 波 水 平 的 影 响 [J]. 稀 有 金 属 材 料 与 工 程 , 2013,42(9): 1859-1863.
[6] Thompson R B, Margetan F J, Rose J H, et al. Influence of microstructure on ultrasonic backscattering noise in titanium alloys[J]. Nondestructive Testing and Evaluation, 1992, 8-9(1-6):485-495.
[7] Gigliotti M F X, Bewlay B P, Deaton J B, et al.Microstructure-ultrasonic inspectability relationships in Ti6242: signal-to-noise in fine-grain-processed Ti6242[J].Metallurgical and Materials Transactions A, 2000, 31:2119-2125.
[8] Wu J, Wang L, Liu X, et al. Evolution of microstructure and microtexture in Ti-2A1-2.5Zr during one pass cold pilgering[J]. Rare Metal Materials and Engineering, 2022,51(4): 1145-1151.
[9] Humbert M, Moreau A, Uta E, et al. Analysis of backscattered ultrasound amplitude of Ti-5.8Al-4Sn-3.5Zr-0.7Nb-0.5Mo-0.3Si samples in term of their microstructures and local textures[J]. Acta Materialia, 2009, 57: 708-714.
[10] Lobkis O I, Yang L, Li J, et al. Ultrasonic backscattering in polycrystals with elongated single phase and duplex microstructures[J]. Ultrasonics, 2012, 52 (6): 694-705.
[11] Li J, Yang L, Rokhlin S I. Effect of texture and grain shape on ultrasonic backscattering in polycrystals[J]. Ultrasonics, 2014, 54(7): 1789-1803.
[12] Baelde A, Laurent J, Millien P, et al. Effect of microstructural elongation on backscattered field: Intensity measurement and multiple scattering estimation with alinear transducer array[J]. Ultrasonics, 2018, 82: 379-389.
[13] Kube C M, Arguelles A P, Turner J A. Ultrasonic backscatter from elongated grains using line focused ultrasound[J].Ultrasonics, 2018, 82: 79-83.
[14] Li X B, Fu Y D, Zhang F, et al. Detecting small flaws in two-phase Ti-6Al-4V with rough surfaces[J]. Ultrasonics, 2020, 106: 106128.
[15] Fisher E S, Renken C J. Single-crystal elastic moduli and the hcp→bcc transformation in Ti, Zr, and Hf[J]. Physical Review, 1964, 135: A482-A494.
[16] Zheng G M, Mao X N, Li L, et al. The variation of microstructures, textures and mechanical properties from edge to center in cross section of Ti6242s titanium alloy[J].Vacuum, 2019, 160: 81-88.
[17] 李磊, 韩飞孝, 周敏, 等. 叶片用小规格 TC4 棒材的组织和 织 构 研 究 [J]. 稀 有 金 属 材 料 与 工 程 , 2023, 52(11):3909-3914.
[18] 韩飞孝, 孙小平, 郑念庆, 等. 热加工工艺对叶片用 TC4钛 合 金 棒 材 组 织 与 性 能 的 影 响 [J]. 钛 工 业 进 展 , 2022,39(6): 7-12.
[19] Blodgett M P, Eylon D. The influence of texture and phase distortion on ultrasonic attenuation in Ti-6Al-4V[J]. Journal of Nondestructive Evaluation, 2001 20(1): 1-15.
[20] Bhattacharjee A, Pilchak A L, Lobkis O I, et al. Correlating ultrasonic attenuation and microtexture in a near-alpha titanium alloy[J]. Metallurgical and Materials Transactions A, 2011, 42: 2358-2372.
[21] Warwick J L W, Coakley J, Raghunathan S L, et al. Effect of texture on load partitioning in Ti-6Al-4V[J]. Acta Materialia,2012, 60: 4117-4127.
[22] Liu Y, Dunne F P E. The mechanistic link between macrozones and dwell fatigue in titanium alloys[J]. International Journal of Fatigue, 2021, 142: 105971.
[23] Moreau A, Toubal L, Bocher P, et al. Evaluation of macrozone dimensions by ultrasound and EBSD techniques[J]. Materials Characterization,2013,75:115-128.
[24] Lan B, Lowe M, Dunne F P E. Experimental and computational studies of ultrasound wave propagation in hexagonal close-packed polycrystals for texture detection[J].Acta Materialia, 2014, 63: 107-122.
[25] Lan B, Carpenter M A, Gan W, et al. Rapid measurement of volumetric texture using resonant ultrasound spectroscopy[J]. Scripta Materialia, 2018, 157: 44-48.
[26] Lan B, Britton T B, Jun T S, et al. Direct volumetric measurement of crystallographic texture using acoustic waves[J]. Acta Materialia, 2018, 159: 384-394.
[27] Du H L. Characterization of microstructural anisotropy using the mode-converted ultrasonic scattering in titanium alloy[J].Ultrasonics, 2022, 119: 106633.
相关链接