钢铁是全球经济中最重要的工程材料。而钒钛磁铁矿作为炼铁原料在世界上的存量很大(约 200 亿吨) [1] 。我国四川攀枝花拥有储量高达 100 亿吨的钒钛磁铁矿,是我国三大铁矿之一,占据世界含钛铁矿储量的一半 [2] 。然而,钢铁工业一直对环境有着较大的影响。为响应国家“双碳计划”号召,将控制钢铁企业二氧化碳的排放,促进其与环境保持协调一致。
钢铁的大规模生产不可避免地伴随着产出大量的炉渣。冶炼钒钛磁铁矿所产出含钛高炉渣的处理是钢铁工业可持续发展的一大挑战 [3] 。若没有对含钛高炉渣进行积极有效的处理,可能会使其有害成分渗入地下,严重破坏附近生态系统,会严重威胁居民用水;还会导致粉尘扩散到空中,使得大气环境中的颗粒物增加,降低空气质量。因此如何高效进行含钛高炉渣的资源化利用,使含钛高炉渣变废为宝,防止对环境产生污染,又给相关行业提供适合的原料变得极为重要 [4-6] 。当前,针对含钛高炉渣资源化利用的关键为对钛元素和余热的利用。
部分企业使用钛含量低的含钛高炉渣制作水泥,因为钛含量较低不会对水泥的强度产生较大影响 [7] 。严芳等 [8] 发现制备混凝土所需的天然砂可以用含钛渣来替代,并使其力学性能能够有所保证。但这些利用含钛高炉渣的方式为低价值利用,没有对含钛高炉渣中钛元素高效利用,造成了极大地浪费。曹洪杨等 [9] 发现对于含钛高炉渣在适宜条件下对其进行酸浸处理,能够得到 95%以上的钛浸出率。龙雨等 [10] 发现对含钛高炉渣进行高温碳化处理,其提钛的最佳温度是为1450 ℃,碳化钛在碳化渣中的比例能够达到 38.35%。上述方法能够利用到含钛高炉渣中的钛元素,有效回收其中的钛资源,但是处于实验阶段,尚不能大规模运用于生产实践中。故需要为含钛高炉渣的高效资源化利用提供一个新的方式。
因此,如何科学处理产量巨大、成分复杂的含钛高炉渣,使其减量化、无害化、资源化,从而推动我国钛资源高效、清洁、可持续利用,在改善我国能源结构的同时,达到保护环境的目的,这已成为我国重点关注的课题。
1 、含钛高炉渣利用途径调研
含钛高炉渣的形成流程如图 1 所示。

含钛铁矿石首先进行精炼,成为铁精矿,将其在高炉中进行冶炼,而含钛高炉渣则为其产物之一 [11] 。某含钛高炉渣成分如表 1 所示。TiO2 的含量为 22.19%,CaO 含量为 20.34%,SiO2 含量为 17.80%,Al 2 O3 含量为 14.59%,MgO 含量为 8.20%。

1.1 含钛高炉渣低附加值利用
由图 2 可知含钛高炉渣制作水泥和混凝土的流程。将含钛高炉渣作为水泥掺混料,加入到普通水泥中,混合均匀,制备成硅酸盐水泥。当高炉渣中钛含量低于 10%时,整体含钛高炉渣与普通炉渣性能相似,可直接作为掺混料。然而,当高炉渣中钛含量高于 10%,与普通炉渣性能有明显的差异,会严重影响到最终水泥成品的性能。故需按一定比例加入至普通水泥中,最终形成硅酸盐水泥 [12] 。在胶结料中加入含钛高炉渣,改变胶结料中不同原料的比例,形成新的胶凝材料,再将其与集料混合均匀,最终形成混凝土。此方法配置出的混凝土性能优于传统混凝土,其力学的性能优异 [8] 。
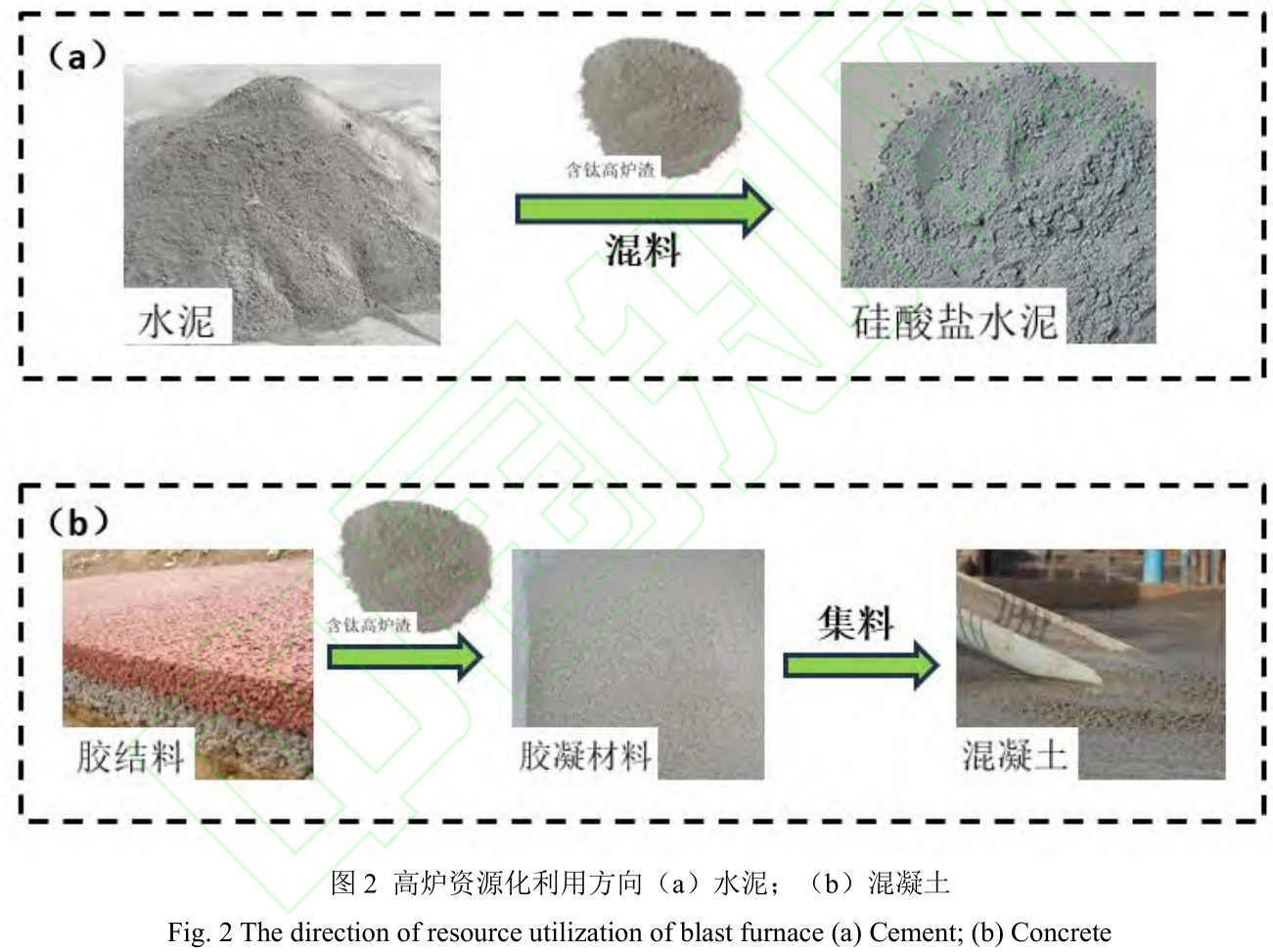
含钛高炉渣生产微晶玻璃的工艺流程如图 3 所示 [13] 。图 3(a)熔融法所示,含钛高炉渣加入形核剂,在高温情况下进行熔化和均化,并形成玻璃熔体。再进行浇注成型形成基础玻璃素坯。随后对其进行退火和热处理最终形成微晶玻璃 [14-17] 。图 3(b)烧结法所示,熔融烧结是将玻璃熔体进行水淬、筛分形成基础玻璃,再压延成型为基础玻璃素坯,最后对其进行热处理,制成微晶玻璃。直接烧结是将含钛高炉渣直接烧结形成基础玻璃素坯,再对其进行热处理,最终形成微晶玻璃。

由图 3 知,熔融法与熔融烧结法两者都要进行二次加热,两者区别为成型的方式不同,熔融法为浇注成型,而熔融烧结法为压延成型,最终微晶玻璃的形成都要受到磨具的影响。
而这两种方法与直接烧结法最大的区别就是直接烧结法只需进行一次加热,没有高温熔融,大大节省了能源。其中熔融法相较于烧结法,其微晶玻璃的气孔较少,其力学性能优于烧结法形成的产品。
泡沫玻璃的工艺流程如图 4 所示。废玻璃与含钛高炉渣作为原料,经过预热、熔融、发泡、退火等工艺,制造了导热性能差、孔径大小均匀的泡沫玻璃。其作为吸音绝热物质,具有显著的隔热,疏水,微气孔等特点,经常应用在隔热砖、板中。
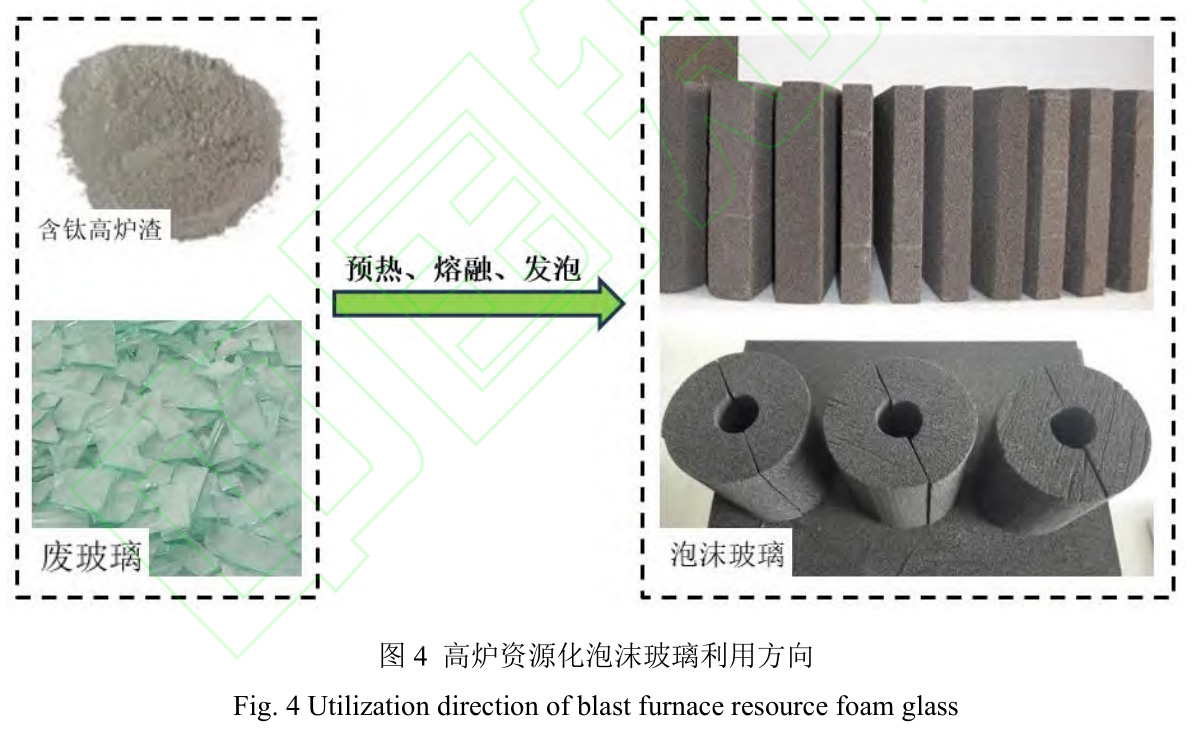
由此可知,含钛高炉渣资源化利用有很多方向。例如,制作混凝土、水泥、微晶玻璃和泡沫玻璃等建筑材料。然而,这些方法存在缺陷:一是使用这些方法对含钛高炉渣进行资源化利用时,没有充分利用含钛高炉渣中的金属元素,造成了资源上的的浪费。二是建筑材料没有什么附加值,产生不了大的经济效益。
1.2 含钛高炉渣高附加值利用
二氧化钛光催化剂机理如图 5 所示。TiO2 中被束缚的电子要成为自由电子或者空穴,必须获得最小能量值为 3.2 e V。当二氧化钛通过对光的吸收而收集的能量(h v )能使其跨过带隙的宽度(E g ),二氧化钛自由空穴存在的能带(VB)中电子受到刺激,进行跃迁行为,到达自由电子存在的能带(CB),生成了新电子 (e–),空穴(h+)将会在 VB 中出现,带正电荷。
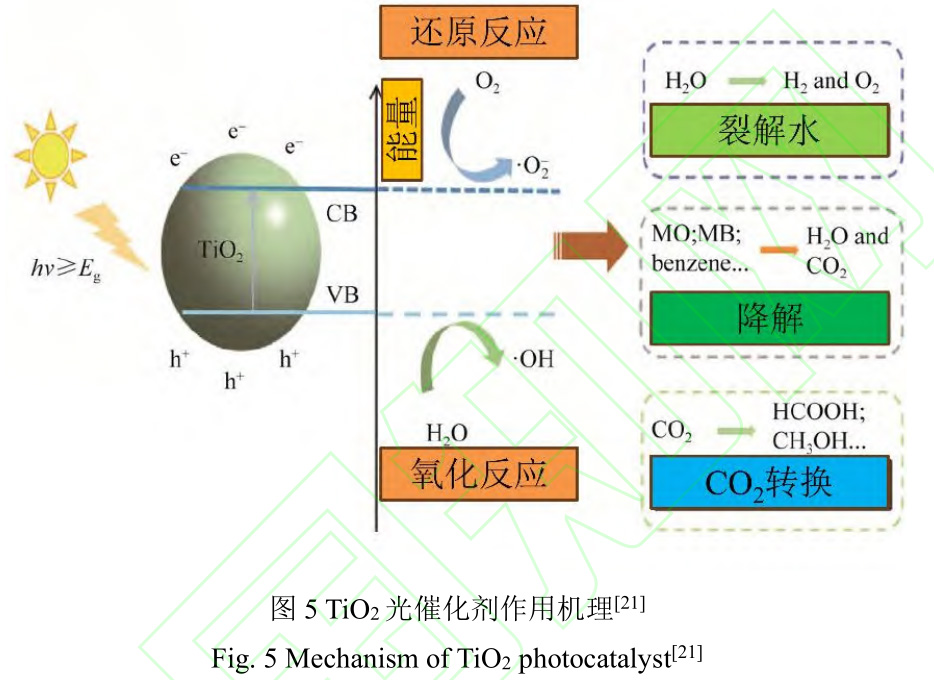
二氧化钛最终出现了空穴–电子对。
在空间电场范围内,高能导带的电子转移到 TiO2 催化剂表面,会与其周围的 O2 发生还原反应,生成产物 O2- ,低能价带的空穴也会与其附近的 H 2 O 发生反应生成产物 OH - 。在 TiO2表面会生成的活性基团能够降解有机的污染物,使其转化为 H2 O、CO2 。之后水和二氧化碳在催化剂表面被反应生成 H2 、O2 和甲酸、甲醇、乙醇等化合物。
含钛高炉渣能够具备光催化活性的关键之处在于其中的钛元素。杨合等 [18-19] 通过掺杂蕴含稀土元素的 CeO2 ,Y 2 O 5 等氧化物来提高含钛高炉渣对甲基蓝和含酚废水的光催化能力。
雷雪飞等 [20] 通过将比例不同的硫酸铵加入至含钛高炉渣,形成了具有硫酸盐的钙钛矿型的含钛高炉渣催化剂,用于降解六价的铬废水。
综上所述,含钛高炉渣所具有的光催化性能能够用来降解废弃物,保护环境。由此可得,利用含钛高炉渣的光催化性能是一种具有高附加值的方法,能够充分发挥渣中的 TiO2 作用。但是,由于含钛高炉渣较差的光催化性能,其只能处理较为单一的废水。含钛高炉渣中含有丰富的金属和非金属离子,对含钛高炉渣光催化性能还需要深入的研究,距离大规模工业化还有段距离。
含钛高炉渣制备硅钛合金的工艺流程在下文展示。侯世喜等 [22] 、李祖树等 [23-24] 将含钛高炉渣制备成硅含量为 28.4%~32.5%的合金,在此过程中新型还原剂起到了重要作用。邹星礼等 [25] 使用含钛高炉渣制作阴极材料,碳饱和铜液作为阳极材料,CaCl 2 熔盐作为电解质来制备 Ti x Si y 系列合金。在此过程中,需要保持 1100 ℃的温度,3.5~4.0 V 的电压,并持续 2~8h。
综上所述,含钛高炉渣可以通过添加还原剂或电解法生产出性能合格的硅钛合金,能用于特殊钢冶炼,具有很高的附加值。但是,钛硅合金种类偏少,可应用的市场范围较小,需求量较低,难以从根源解决问题。
2 、含钛高炉渣处理工艺
2.1 含钛高炉渣低附加值处理工艺
2.1.1 水淬法
水淬法的工作流程如图 6 所示 [26] 。高温液态含钛高炉渣在高炉铁口出渣的过程中使用高速水流对其进行分割、击碎,当高温液态含钛高炉渣遇到高速水流进而急速冷却时,高炉渣会由于应力集中而发生收缩行为,促进含钛高炉渣的粉化、破碎,高速水流促使含钛高炉渣发生粒化行为。含钛高炉渣液水淬处理时,对熔渣的控制主要取决于水的操控,水淬法的关键是保证渣彻底粒化。
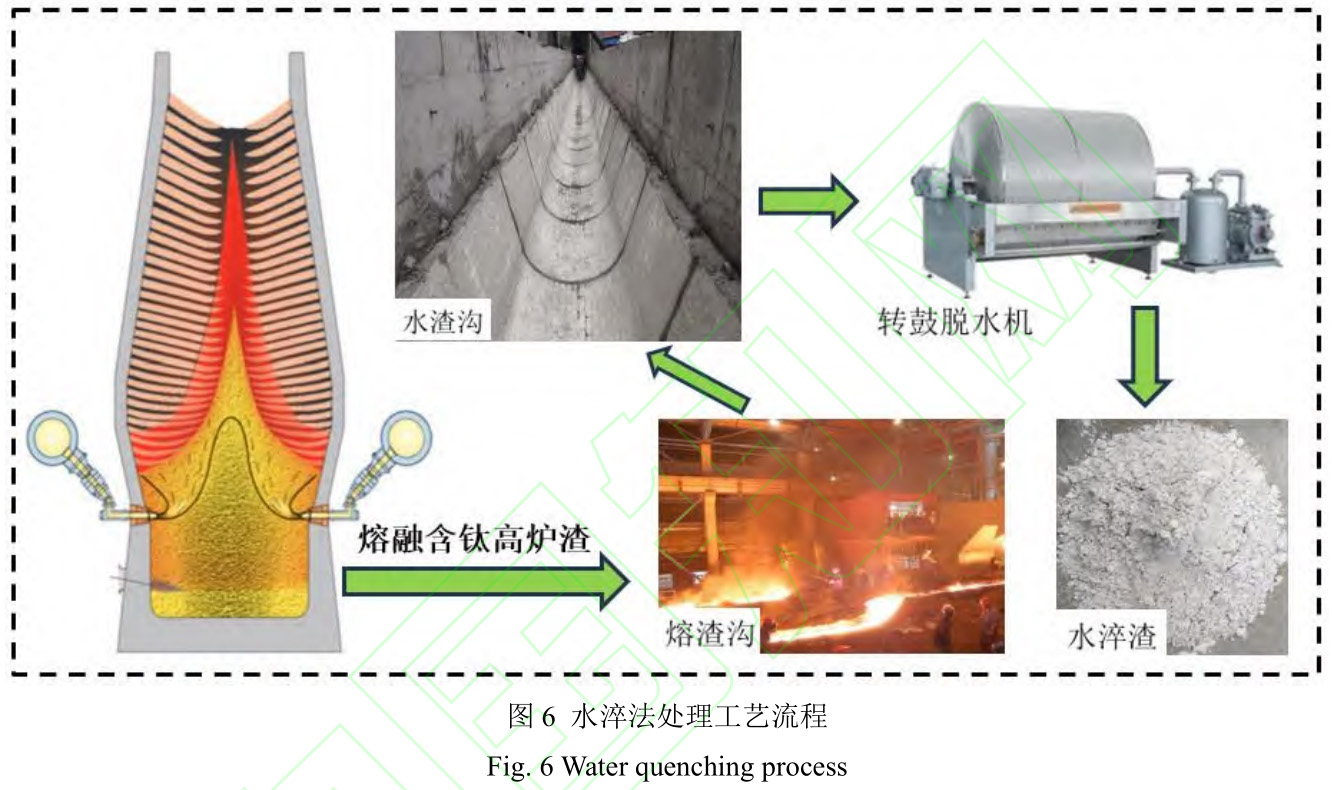
水淬法占用较小的场地面积,需要较少的投资,对环境的污染程度较轻。但其存在发生爆炸的风险,无法保证渣粒度的均匀性,只适合单一液态渣的处理,且没有对含钛高炉渣中金属元素有效利用,没有什么附加值,产生不了大的经济效益。
2.1.2 风淬法
高炉渣风淬工艺流程如图 7 所示 [27] 。渣罐被高炉渣装满,通过倾翻支架将高炉渣液倾倒至中间包,随后通过锅炉,含钛高炉渣的热量通过热辐射被锅炉管吸收,进而对水加热,将产生的蒸汽统一被收集。含钛高炉渣最后传输至粒化器,其释放的高速气流会将高炉渣击碎,且高炉渣表面存在着张力,高炉渣液最终形成半径 1 mm 左右的球状颗粒,并被皮带走。
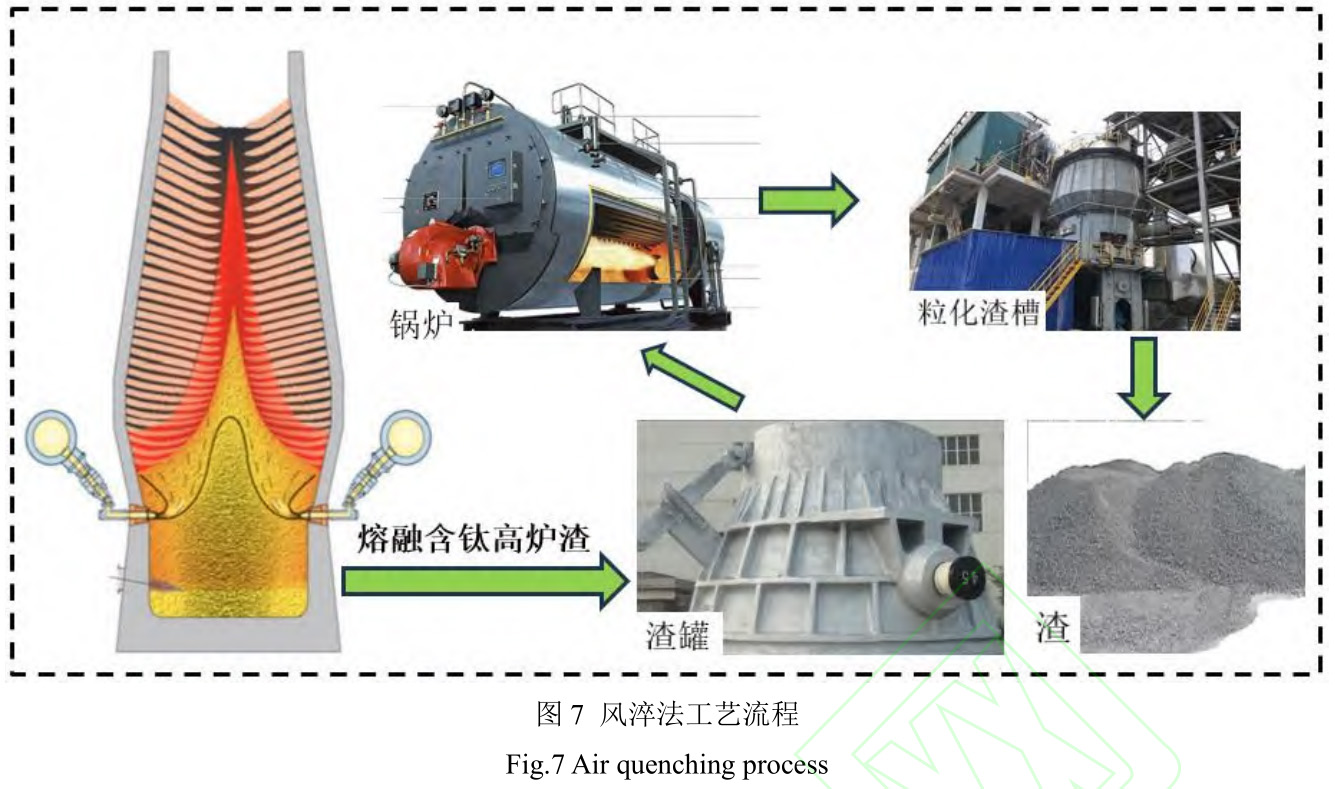
风淬法可以在完成对高炉渣资源回收的前提下,在锅炉处实现对高炉渣余热的回收利用,对比其他处理工艺,能够进一步加强对高炉渣资源的回收利用。风淬法相较于较为类似的水淬法,具有更高的安全系数,生产效率更为高效,整体工艺流程简单,前期投入成本和后期维护成本相对较少。但是,还是没有对含钛高炉渣中金属元素进行有效利用。
2.2 含钛高炉渣高附加值处理工艺
2.2.1 硫酸法处理工艺
由于 TiO2 只能与浓硫酸反应而不能与盐酸反应,可以使用硫酸法处理含钛高炉渣。硫酸法 [28] 是将含钛高炉渣与浓硫酸混合,两者之间会发生反应,将含钛高炉渣中钛化合物反应成钛离子,并进入液体中,随后对其水解形成偏钛酸,将其通过洗涤、过滤和煅烧等措施形成钛白粉,如式(1)、式(2)、式(3)所示。
2 + H2 SO4 = TiOSO4 + H 2 O (1)
TiOSO4 + 2H 2 O = H2 TiO3 + H2 SO4 (2)
H2 TiO3 = TiO2 + H 2 O (3)
硫酸法浸出的工艺流程如图 8 所示。硫酸与 TiO2 反应,从而生成硫酸氧钛,硫酸氧钛再经水解生成偏钛酸,偏钛酸经过煅烧后最终可以得到钛白。Mg、Al 等杂质元素与硫酸反应进入液相,在硫酸氧钛水解时与之分离;而 Ca、Si 等元素则进入渣相。
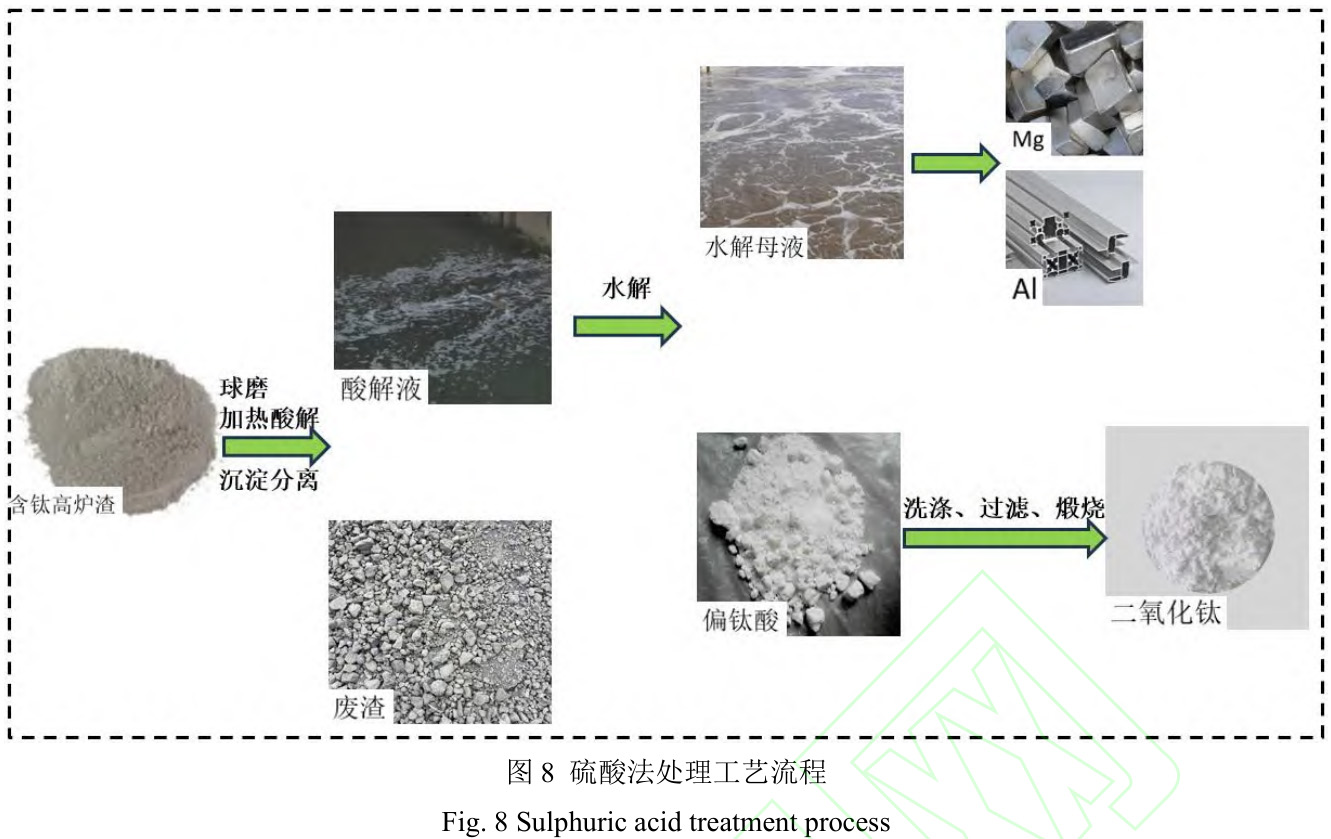
硫酸法可以将含钛高炉渣中的钛分离提取出来,但由于 TiO2 在含钛高炉渣中含量较低,而杂质元素占比很高,超过了 70%。这导致使用硫酸法提钛时,需要消耗大量的酸,且拥有复杂的工艺,生产的成本也高,产生的废酸和尾渣多,对环境造成严重,且使用硫酸法浸取含钛高炉渣时,酸解和水解反应过程复杂,无法确保 TiO2 产品的质量稳定。
2.2.2 稀盐酸处理工艺
在含钛高炉渣进行酸解液处理,在其酸解液中,含有 Fe、Al、Ca、Mg 等金属离子和Cl 离子,其中 Fe、Al 等组分存在较高回收价值,Cl 离子不经处理排放会对环境造成破坏。
稀盐酸法的工艺流程如图 9 所示。将含钛高炉渣加入到存在纯盐酸的密闭容器中,并用磁力搅拌加剧反应的发生,对容器进行加热到预定温度。经过一定时间的反应,对其进行过滤,将过滤出来的滤渣通过去离子水洗涤,在进行研磨、烘干处理,最终得到酸浸渣。稀盐酸法避免了处理高炉渣需要高压、氯气和高温等要求,可以使处理成本下降和减少对环境的破坏 [29] 。
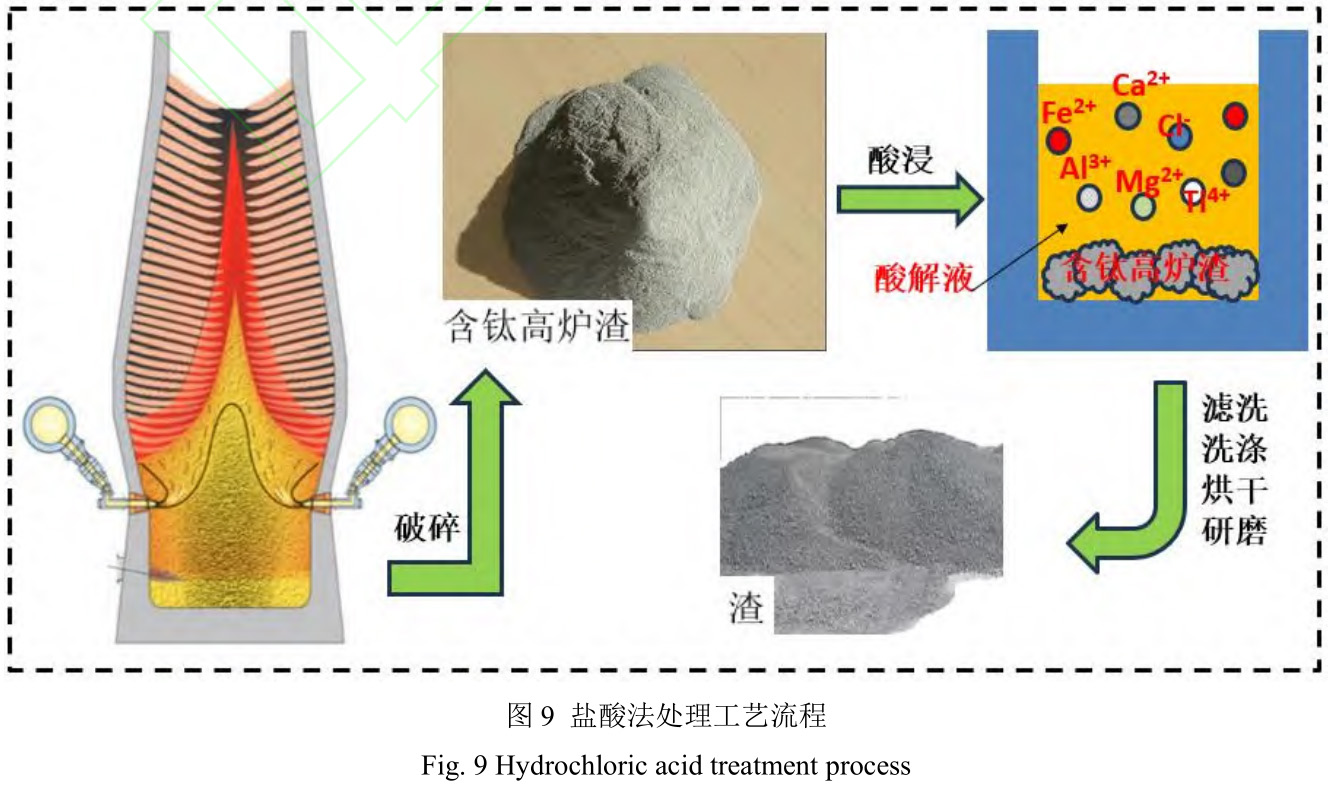
2.2.3 碱熔盐法处理工艺
碱熔盐法 [30] 的原理是由于在高温下渣中含钛物质与强碱会发生反应,形成偏钛酸、钛酸盐,再对其进行水浸、水解和煅烧等操作,最终可以得到钛白粉。发生的反应如下:
TiO2 + 2NaOH = Na 2 TiO3 + H 2 O (4)
Na 4 TiO4 + 4H 2 O = H 4 TiO4 + 4NaOH (5)
H 4 Ti = TiO2 + 2H 2 O (6)
碱法提钛工艺流程如图10所示。碱法提钛原理就是在含钛炉渣中加入渣钛分离剂NaOH或 Na 2 CO3 等,利用提取出来的钛生产钛白粉。先将含钛高炉渣粉碎后,再往含钛高炉渣粉末中添加 NaOH 或 Na 2 CO3 ,将其放入高温炉中进行反应,将高温炉中的炉渣进行分离,将熔体进行冷却水解,将固液两相进行分离,分离出来的液相可以用于制备水玻璃等,将固相进行高温脱水,再进行粉碎,最后加工制成钛白粉。
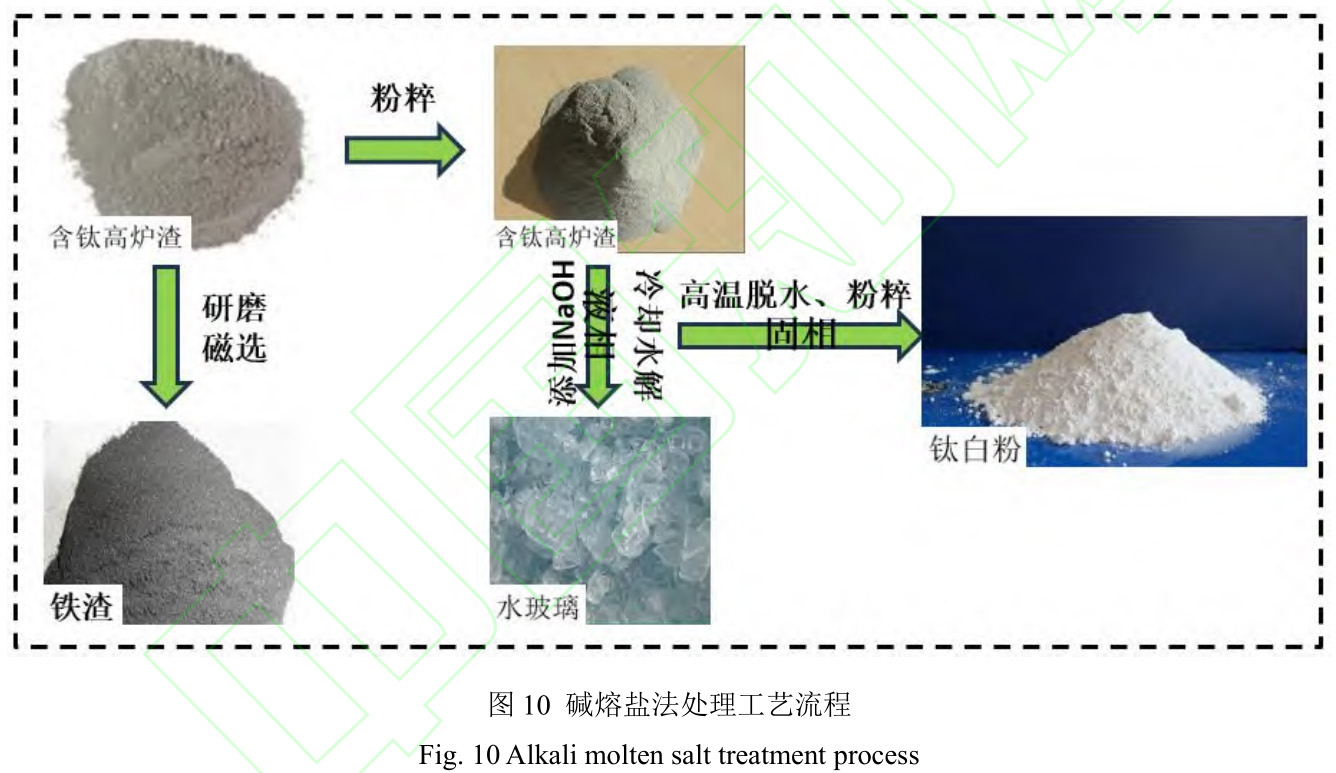
碱法提钛较之酸法,其反应产物的利用率较高,且污染较少。但碱法提钛火法反应温度较高,大多在 1000 ℃以上,较危险,且反应过程中 NaOH 易挥发,容易腐蚀生产设备。
2.2.4 高温选择性结晶分离法处理工艺
高温选择性结晶分离法是针对复合矿冶金渣综合利用的一种新技术,目前已成功应用于硼镁渣中硼的合理回收。含钛高炉渣选择性富集与析出技术的基本原理为:通过改变条件,使得钛组分富集到钛富集相(如钙钛矿、金红石、黑钛石等)中 [31] ,然后控制其冷却条件,促使钛富集相析出长大,最后确定分离工艺,确定相对应的技术参数,促进基体相和钛富集相的分离,其工艺流程如图 11 所示。
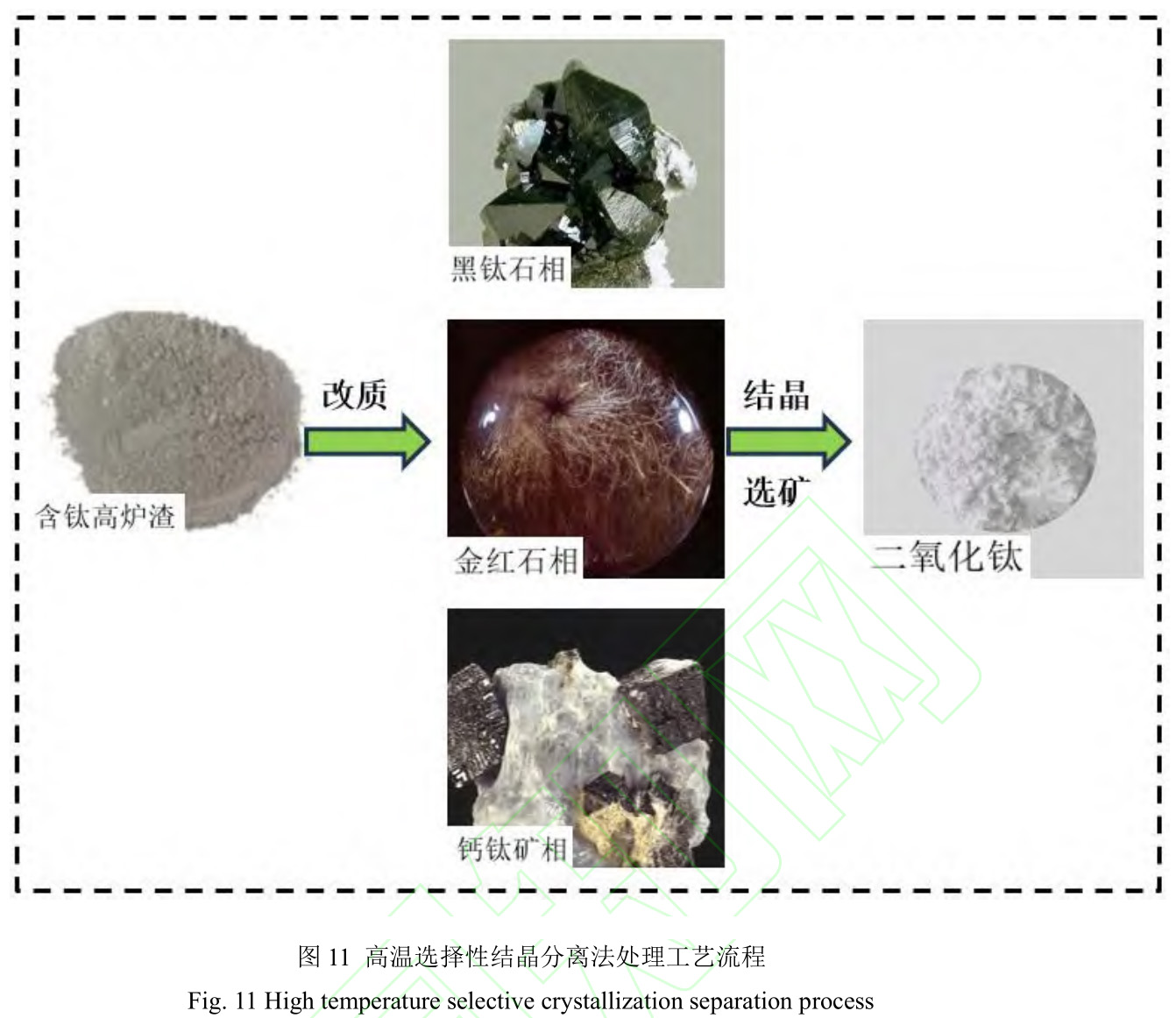
将钛富集到钙钛矿或黑钛石中进行选择性结晶。但钙钛矿大多通过树枝或骨架状析出晶体,钙钛矿晶体的整体尺寸较大,但无法避免出现一些细小颗粒,以不规则锯齿状出现在不同矿相界面。且钙钛矿富钛料的直接利用价值不高,去除钙钛矿富钛料中的 CaO 等需要使用盐酸,工业化条件还不成熟。黑钛石的选择性结晶还无法大规模应用,黑钛石析出条件还需进一步完善。
2.2.5 高温碳化-低温氯化法处理工艺
含钛高炉渣碳热还原得到的 Ti(C,N)精矿,可进一步处理得到纯度较高的 Ti(C,N)。
碳氮化钛能用于制备高级耐火材料、磨料或太阳能吸收新材料,也可以经过低温氯化获得TiCl 4 ,作为制备海绵钛或钛白的原料 [32] 。
含钛高炉渣处于 T>1500 ℃的环境下,其中的钛化物会与碳反应,形成 TiC。当温度至400~550 ℃,氯气会选择性与 TiC 发生反应,并形成 TiCl 4 。发生的反应如式(7)和式(8)所示。
TiO2 + 3C = TiC + 2CO (7)
TiC + 2Cl 2 = TiCl 4 + C (8)
含钛高炉渣高温碳化-低温氯化技术流程如图 12 所示。含钛高炉渣与碳粉进行熔融选择性碳化,再进行冷却,将其产物破碎成粉末,进行磁选,将其中金属铁取出,对剩余物料进行低温性的氯化,制成粗四氯化钛,再精致成精四氯化钛。
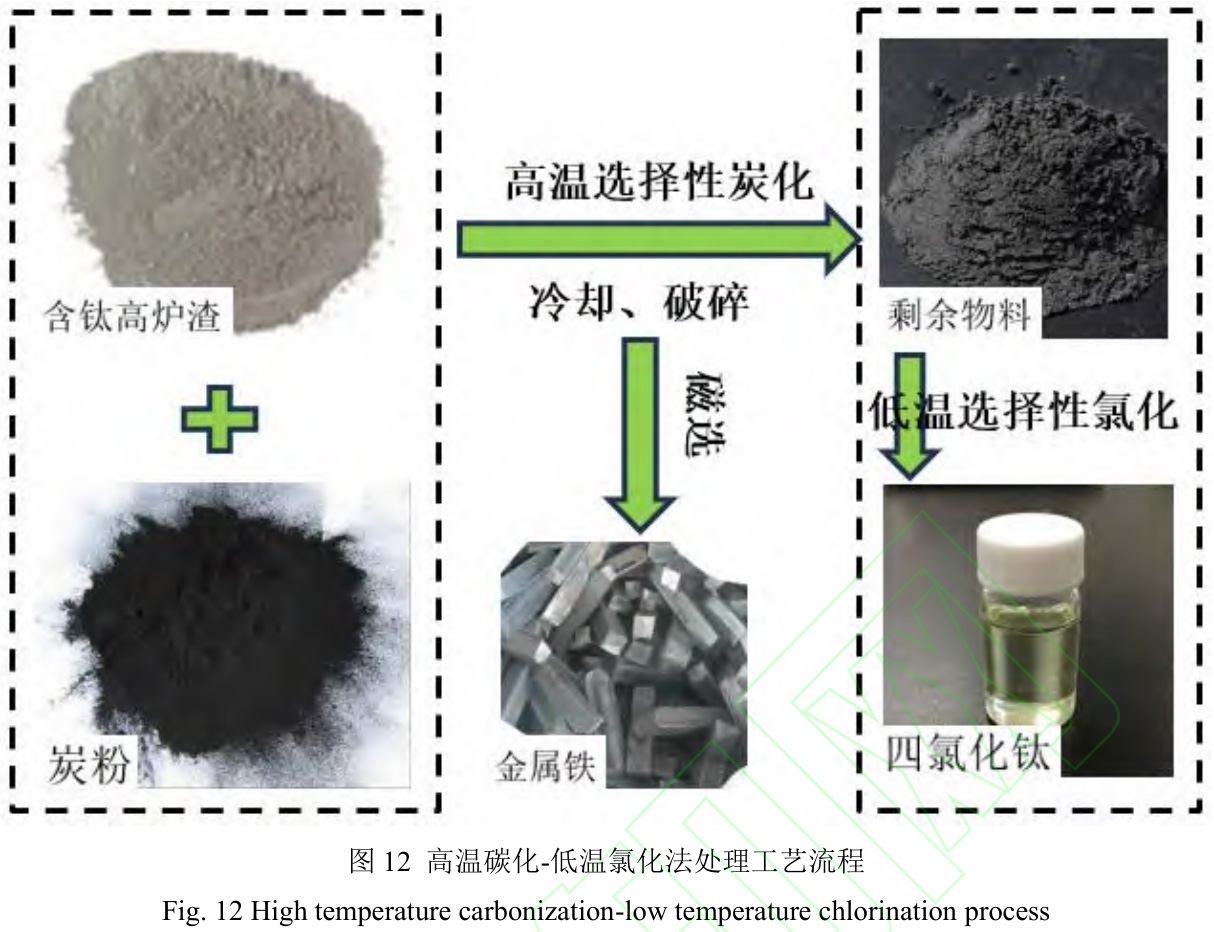
高温碳化-低温氯化法的工艺流程短,通过对含钛高炉渣先进行高温选择性碳化,之后再进行低温选择性氯化操作,使渣中 Ti 富集,解决了含钛高炉渣中钛元素资源化困难问题。
但高温碳化、低温氯化法的碳化、氯化的工艺还不成熟,需要继续完善。且经过此工艺处理后的氯化残渣与普通高炉渣成分十分相似,其利用价值较低,但是由于氯离子必须先经过洗涤除去其中含有对环境产生污染的 CaCl 2 、MgCl 2 等物质,无法进行回填。由于氯离子洗涤除去的花费较大,用于烧制水泥经济上不合算,是导致工业化未能完成的主要原因之一。
2.2.6 钛合金合成法
钛-硅(Ti-Si)合金和钛-硅-铝(Ti-Si-Al)合金在含钛高炉渣中均可提取。因此,通过铝热法和硅热法,从含钛高炉渣中制备钛合金。在铝热过程中,添加过量的铝作为还原剂与SiO2 和 TiO2 反应,新生成的金属 Si、Ti 和残余铝可能形成 Ti-Si-Al 合金 [33] ,如图 13。WANG等[34] 发现了含钛高炉渣中钛和硅的回收率分别为 80%和 70%。当硅用作还原剂时,只有钛被还原生成钛−硅合金。铝热过程和硅热过程是强烈的放热反应。因此,一定量的合金颗粒溅入残余炉渣,降低了萃取效率。
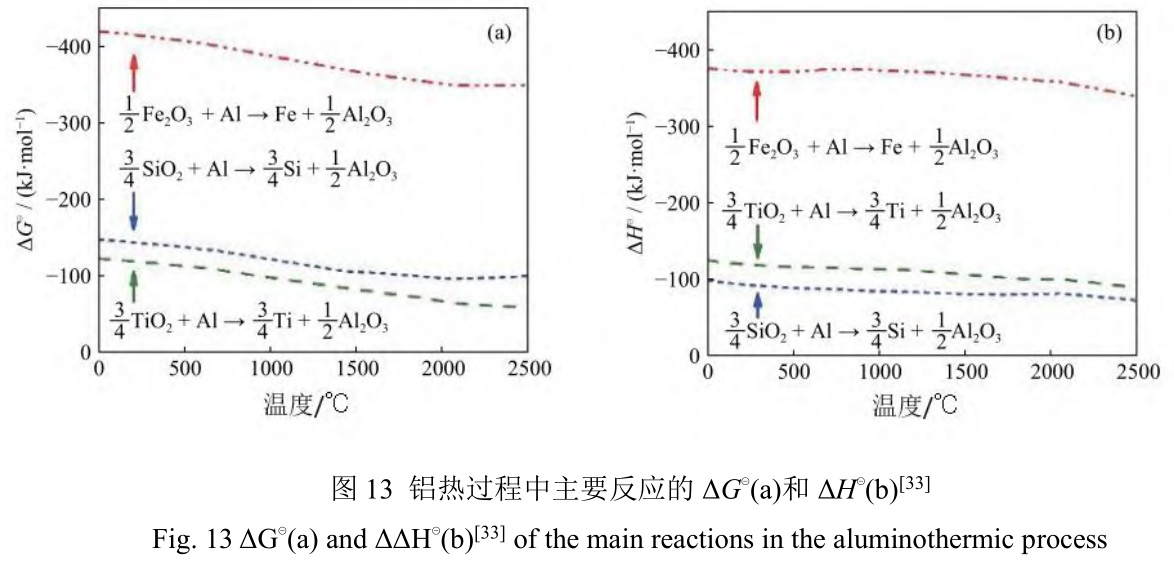
所得合金只能用于金属冶炼,这种低消耗限制了这些合金的广泛应用。且为获得的合金提出了一些后处理策略,如定向凝固和多步骤湿法冶金工艺,以最大限度地利用含钛高炉渣。例如,王超等[35] 对 Si 进行了后处理,钛合金与盐酸一起生产高纯度硅(99.94%),TiO2和 NaF 的产品通过碱性湿法加工生产,如图 14 所示。然而,其后处理工艺复杂,成本高,阻碍了其工业应用。
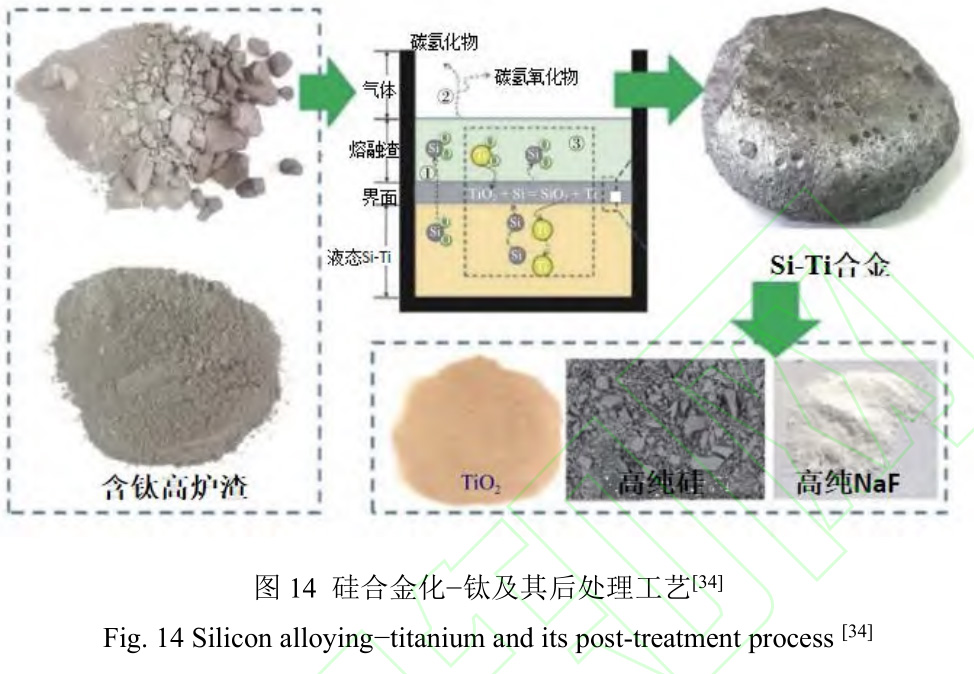
2.2.7 硅-钛溶剂精炼方法
TiSi 2 是 1473 K 以上的一种有用的结构材料,因为其比重量低、熔点高、抗氧化性好。
由于其低电阻率(约 13–16 μ Ωcm)、高温稳定性和良好的耐腐蚀性,TiSi 2 已广泛用于制造微电子器件,如栅极布线、连接器产品、肖特基势垒和欧姆接触材料。
采用了电磁定向结晶,通过分离含钛高炉渣的硅还原获得的硅-钛合金来制备 TiSi 2 ;然而,所获得的 TiSi 2 晶体中残留少量杂质。现在使用硅-钛溶剂通过溶剂精制制备高纯度 TiSi 2 ,以提高 TiSi 2 晶体中杂质的去除率。
这方法提出了一种以含钛高炉渣和低纯硅为原料制备高纯 TiSi 2 的新方法,即硅-钛溶剂精炼。首先,用低纯度硅还原含钛高炉渣中的 TiO2 ,形成未加工的硅钛合金。然后,将不同量的低纯度 Si 添加到原始 Si–Ti 合金中,以获得三种不同的 Si–Ti 溶剂(Si–39.6%Ti、Si–35%Ti 和 Si–30%Ti),用于 TiSi 2 的溶剂精炼。然后将三种 Si–Ti 溶剂分离为 TiSi 2 、共晶 Si–Ti 合金,通过电磁定向结晶凝聚杂质,获得纯净的 TiSi 2 晶体 [36] 。
2.2.8 氢氧化钠常压分解制备二氧化钛的新工艺
最近,中国科学院过程工程研究所开发了一种新的钛铁矿和含钛高炉渣的冶金工艺。在此过程中,钛铁矿或含钛高炉渣首先在常压下被浓缩的 KOH 溶液分解,形成高钛低铁的中间产物,进一步处理后可转化为颜料级二氧化钛。然而,大量 KOH 溶液的回收占用了最多的工艺能耗。
氢氧化钠常压分解制备二氧化钛的新工艺是使用无烟煤作为还原剂,在电弧炉中冶炼钛铁矿来制造用作制备二氧化钛原料的钛渣。在此过程中,钛渣首先在 NaOH 系统中低温分解。然后用水处理中间产物,提供可能被描述为含有固体氧化钛和溶液中副产物的浆料。氧化钛可以通过过滤从混合物中分离出来,并通过以下在稀酸溶液中回流的方式进行纯化 [37] 。该工艺的一般流程如图 15 所示。与氯化物工艺中的氯化和氧化相比,该工艺中的反应温度降低了 500 ℃。
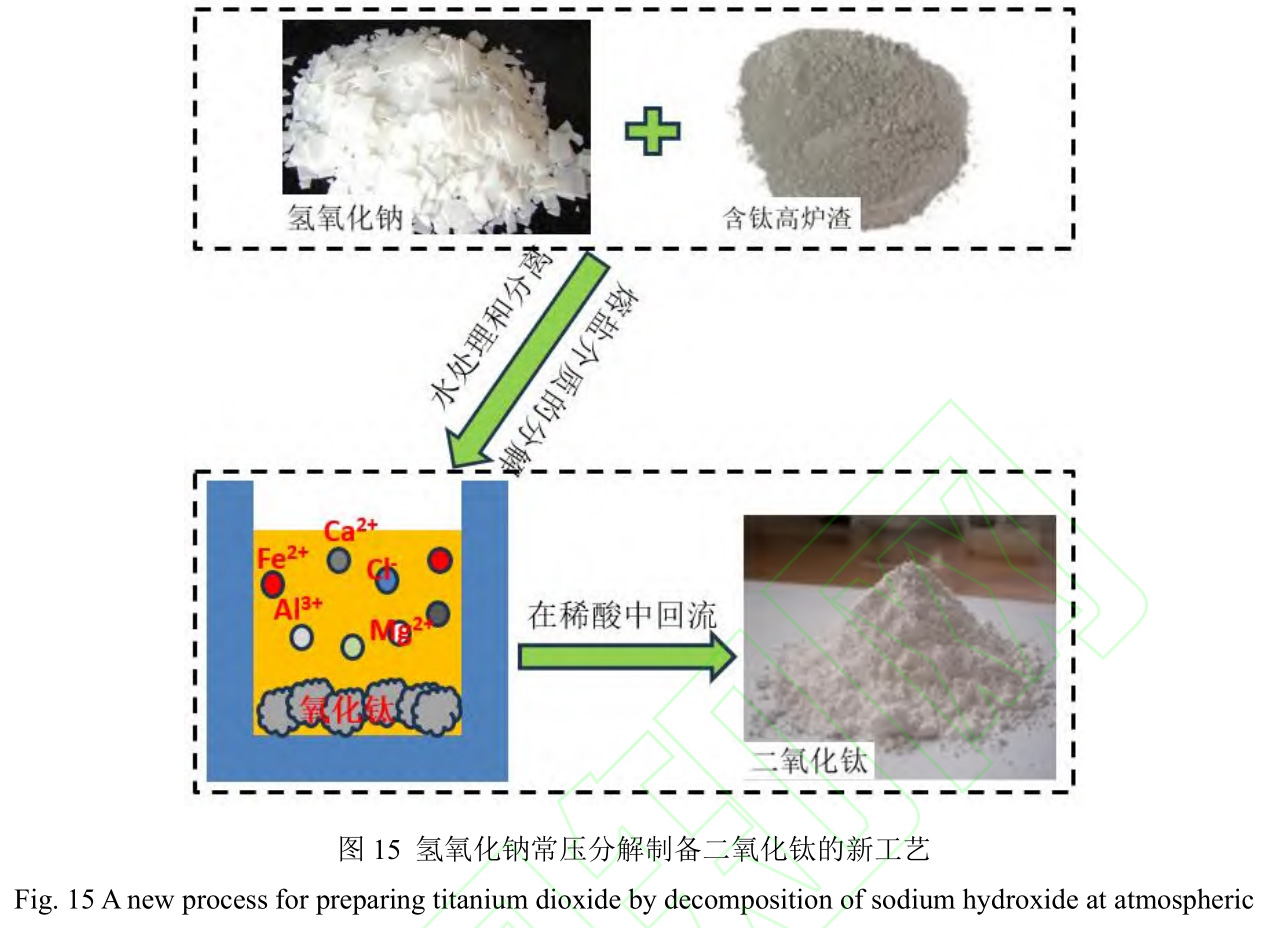
2.2.9 高炉熔融渣直接生产人造石材工艺
将高温液态含钛高炉渣作为原料直接利用,在尽量不调质的前提下加工成制成品。首先经过理论论证,认为高炉渣的成分构成具备形成良好岩石材的条件。在此基础上,通过多次试验,在实验室熔化渣样及在渣沟直接取渣进行晶化及退火实验,证实了熔融态高炉渣可以在受控条件下,直接晶化为人造石材。该工艺既能利用高炉渣的显热,又能完全利用固体物。
熔融含钛高炉渣生产人造石材,其制备技术有 2 种:浇铸法和压延法。浇铸法用于生产耐磨耐腐蚀复合管,压延法用于生产板材产品。压延法工艺流程为:将熔融高炉渣通过专用渣包转运到熔窑内,于 1 450 ~1 470 ℃保温、均化后,将熔体压延成型,在一定的热处理制度下进行核化和晶化,以制得晶粒结构均匀致密的结晶材料,最后经切割、抛光等工序得到成品。高炉熔融含钛高炉渣直接生产人造石材工艺流程如图 16 所示。
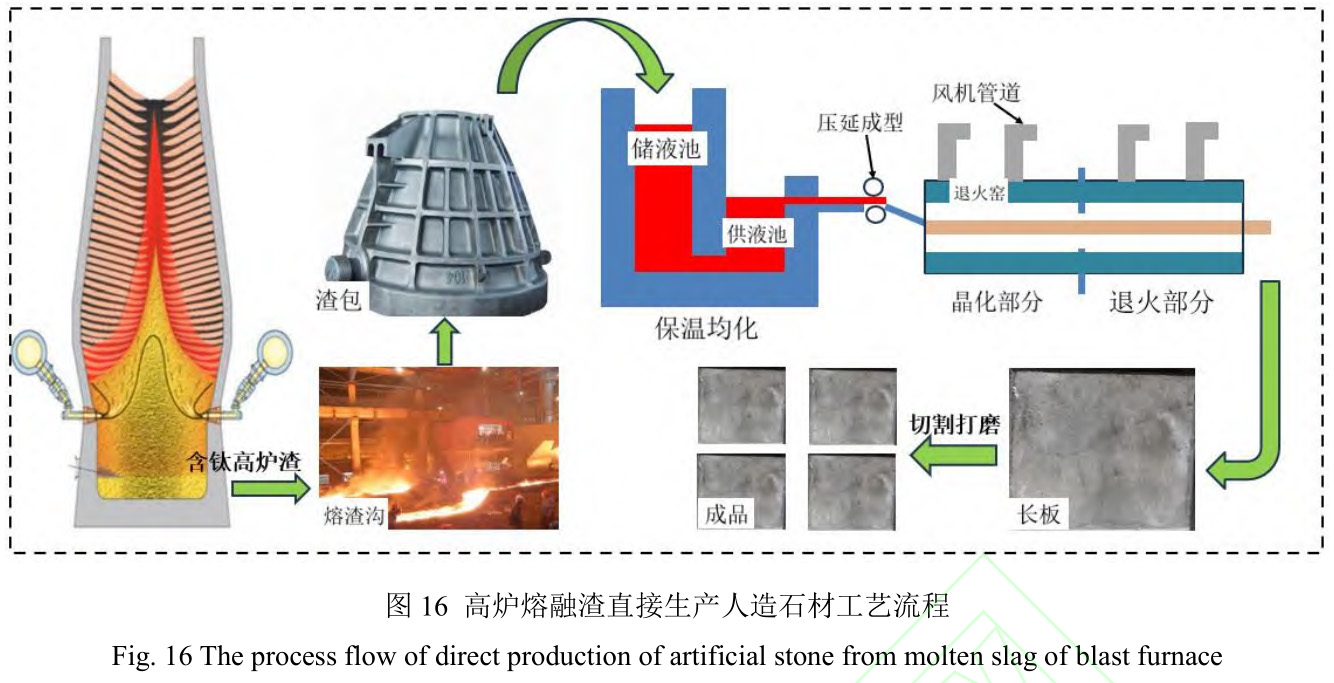
压延法借鉴了铸石的生产流程。将铸石的熔化窑替换成保温均化窑,铸石成型替换为压延成型,晶化退火炉都是一样。保温均化炉需根据高炉渣成分特点,对其使用高炉与转炉混合煤气进行顶部加热,钼电极进行液内电加热。晶化退火炉需采用专门用于无机材料析晶而设计的炉子,可调节各段温度。
高温熔融含钛高炉渣工业化面临的问题有需要为压延机提供连续可调的供料。其属于高氧化钙硅酸盐材料,加工温度区间很窄。其晶化与退火时需要确定其中间过冷度。
高炉熔融含钛高炉渣直接生产人造石材的产品可分为两类,一类是晶粒较大、结晶均匀、指标合格的结晶人造石材,代替天然石材,面向路面石材板、路缘石及外墙石板;另一类是晶粒细小、结晶均匀致密、指标优良的二代产品-瓷砖。
3、 含钛高炉渣前景工艺
3.1 国内含钛高炉渣目前现状
随着粗钢产量的快速增长,高炉渣的产量也稳步上升 [38] 。截至目前为止,我国高炉冶炼产生的含钛高炉渣已达 9000 多万吨,而且每年仍然以超过 300 万吨/年的速度增长。如图17 所示,我国每年在攀枝花地区会生产约 400 万吨的高钛渣,在河北承德地区会生产约 250万吨的中钛渣,另还会生产约 1000 万吨的低钛渣。含钛高炉渣资源化利用的前景十分广阔。
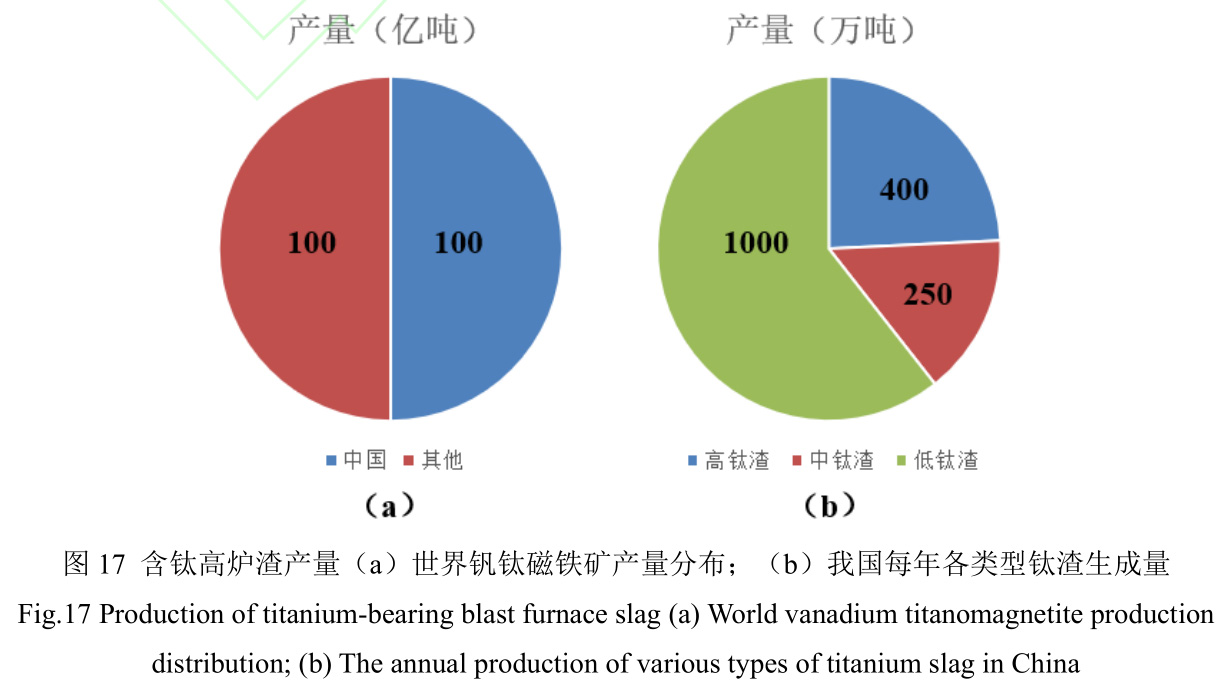
因此,含钛高炉渣不断增长而引起的一系列环境污染问题,是我国亟待解决的难题。近年来,随着政府对环境和资源问题的关注力度不断加大,含钛高炉炉渣资源化的技术路线、管理模式、价值化标准和环境法规不断完善。
3.2 高炉熔融渣直接生产人造石材工艺优势
如图 18 所示,人造石材是由岩浆从火山喷发出来,经过自然演变而形成的。而熔融状态的含钛高炉渣与岩浆有着相似的地方,其都为硅酸盐材料且都具有高温性能。对熔融含钛
高炉渣经过一些可控的操作,如成型和晶化,从而制造人造石材。因此,高炉产生的 1450 ℃的熔融高炉渣就如同可以控制的岩浆,是一笔巨大的财富。
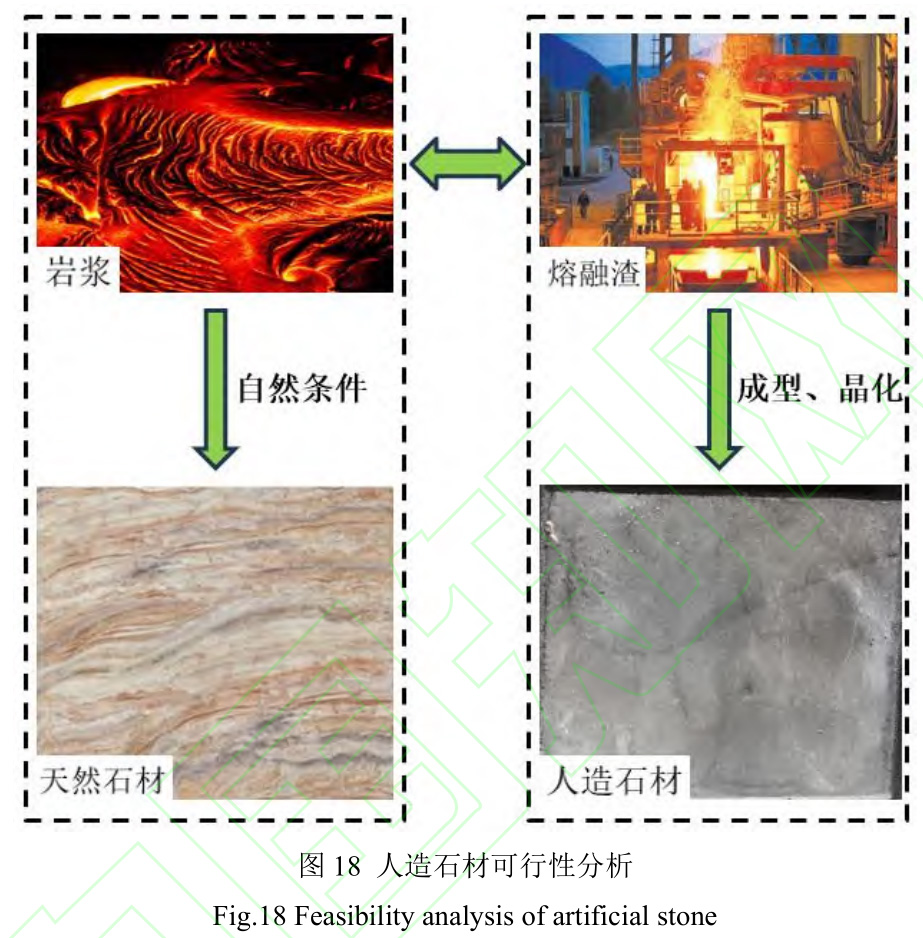
理论论证表明高炉渣的成分构成具备直接生产良好岩石材的条件。高炉熔融渣直接生产人造石材工艺较之当前处理高炉渣工艺,可以实现“渣”与“热”的双利用,提高了高炉渣的利用效率;减少了原燃料、运输及原料加工等环节的费用,可大幅度降低终产品的成本;采用全干法生产,无废水、废气的处理及排放。该工艺竞争优势极其明显。高炉熔融渣直接生产的人造石材成本优势明显,粗略估算吨成本仅为原石材的 30%左右。与生产烧结砖成本对比,省去了原料运输、原料破碎和烧结燃料的费用,综合估算人造石材成本比烧结砖约少 30%。
随着环保要求的不断提高,国土局等有关部门对原石材及黏土等建材原料的开采限制越来越严,近几年建材行业的原料成本涨幅巨大,耐火材料的原料涨幅更大,烧结砖也有明显的涨价趋势,这为高炉熔融渣的直接利用提供了非常好的政策环境。如表 2 所示,目前普通石材产地原石的成本约 450 元/吨;中国黑色石材产地原石的成本约 800 元/吨,熔融态钒钛渣人造石材估测成本约 232 元/吨。从成本上,熔融态钒钛渣生产普通颜色人造石材,每吨利润提高约 218 元/吨;生产黑色人造石板,每吨利润提高约 568 元/吨。从高炉熔融渣直接生产人造石材工艺和成本优势来看,该工艺在未来的含钛高炉渣资源化利用中有很高的应用潜力。

4 、结 论
半个世纪以来,高炉矿渣的综合利用深受广泛关注,最常用的处理途径是将高炉矿渣用作建筑材料的原材料,如水泥和烧结材料。这种处理方法的特点是高炉煤气消耗量大,但对有价金属元素的有效利用未充分考虑,因此应该减少或杜绝含钛高炉渣的非资源化利用。
钛元素的提取是金属资源最为丰富的一种替代方法。目前为止,已制定了各种提取策略,如酸浸、碱熔盐煅烧、碳化-氯化和高温浓缩等。然而,以上诸多方法在该行业的实际应用仍存在障碍。例如,湿法冶金可以获得钛的高萃取效率,但使用高腐蚀性试剂,这增加了环境污染的风险;火法冶金因其效率低、成本高而受到限制等。
目前,含钛高炉渣的资源化利用工艺都存在一些问题,比如没有很好的利用渣的余热及固体物,造成环境污染,生产成本高等。高炉熔融渣直接生产人造石材工艺作为含钛高炉渣资源化利用的前沿工艺,能够很好的解决其他工艺存在的诸多问题,比如高效利用渣的余热及固体物,无废水、废气处理及排放,节省成本等,因此该工艺在未来大有为之。
参考文献:
[1] 贾峰.含钛高炉渣资源化综合利用研究[D].南京:南京师范大学,2013.
[2] 杜鹤桂,等.高炉冶炼钒钛磁铁矿原理[M].北京:科学出版社,1996:8-11.
[3] 张媛媛.直接还原高磷铁矿铁磷分离工艺基础研究[D].北京:北京科技大学,2019.
[4] 张立生,李慧,张汉鑫,等.高炉渣的综合利用及展望[J].热加工工艺,2018,47(19):20-24.
[5] 杨合.含钛高炉渣再资源化的一个启发性观点[D].沈阳:东北大学,2005.
[6] CAI Y F,SONG N N,YANG Y F,et al.Recent progress of efficient utilization of titanium-bearing blast furnace slag[J].International Journal of Minerals,Metallurgy and Materials,2022,29(1):22-31.
[7] 董海刚.从含钛高炉渣中回收钛的基础研究[D].长沙:中南大学,2006.
[8] 严芳,李春,梁斌.水淬含钛高炉渣二段酸解工艺[J].过程工程学报,2006,6(3):413-417.
[9] 曹洪杨,付念新,康常波,等.改性含钛高炉渣的盐酸加压浸出[J].矿产综合利用,2008(4):11-14.
[10] 龙雨,张新建,李书兰,等.含钛高炉渣高温碳化制备 TiC 影响因素研究[J].重庆理工大学学报(自然科学),2017,31(8):93-97,119.
[11] CAI Y F,SONG N N,YANG Y F,et al.Recent progress of efficient utilization of titanium-bearing blast furnace slag[J].International Journal of Minerals,Metallurgy and Materials,2022,29(1):22-31.
[12] 景建发,郭宇峰,郑富强,等.含钛高炉渣综合利用的研究进展[J].金属矿山,2018(4):185-191.
[13] 安卓卿,王艺慈,张帅,等.冶金工业固废制备微晶玻璃研究进展[J].中国陶瓷,2022,58(7):9-20.
[14] 连水瑕.高炉渣中二氧化硅选择性提取及应用研究[D].太原:太原理工大学,2021.
[15] 刘栩雯.气粉流粒化高炉渣及余热回收工艺的探索[D].天津:天津大学,2018.
[16] 甄玉兰.攀枝花含钛高炉渣资源化利用新途径[D].北京:北京科技大学,2016.
[17] 陈蓓,魏瑞航,罗启泉,等.高炉钛渣和废玻璃生产矿渣微晶玻璃的研究[J].重庆大学学报(自然科学版),1992,15(4):62-67.
[18] 杨合,马明龙,高明磊,等.添加剂对含钛高炉渣制备泡沫玻璃性能影响[J].钢铁,2009,44(11):95-98.
[19] 杨合.含钛高炉渣再资源化的一个启发性观点[D].沈阳:东北大学,2005.
[20] 雷雪飞,薛向欣.掺杂硫酸盐对含钛高炉渣光催化性能的影响[J].材料导报,2009,23(2):63-66.
[21] 李明阳,张晨,梁锐,等.高炉渣基光催化材料在废水处理领域的研究进展[J].硅酸盐学报,2023,51(1):270-282.
[22] 侯世喜,柯昌明,李有奇,等.金属热还原含钛高炉渣制取合金及残渣的研究[J].铁合金,2007,38(5):20-23.
[23] 李祖树,徐楚韶.提高钛硅合金等级的研究[J].重庆大学学报(自然科学版),1994,17(4):96-103.
[24] 李祖树,徐楚韶,李在妙,等.用高炉钛渣冶炼钛硅合金的研究[J].重庆大学学报(自然科学版),1996,19(4):82-86.
[25] 邹星礼,鲁雄刚.攀枝花含钛高炉渣直接制备钛合金[J].中国有色金属学报,2010,20(9):1829-1835.
[26] 肖双林,陈荣全,谷孝保.应用水淬法处理韶钢 120t 转炉钢渣[J].材料研究与应用,2010,4(4):561-563.
[27] 闫兆民,周扬民,杨志远,等.高炉渣综合利用现状及发展趋势[J].钢铁研究,2010,38(2):53-56.
[28] 严芳.水淬含钛高炉渣的酸解研究[D].成都:四川大学,2006.
[29] 张月,王海波,刘湘.高钛高炉渣提钛综合利用研究现状[J].新型工业化,2018,8(8):124-127.
[30] 居殿春,武兆勇,张荣良,等.含钛高炉渣提钛技术研究现状及展望[J].现代化工,2019,39(增刊 1):104-107.
[31] 许莹,李单单,杨姗姗,等.含钛高炉渣综合利用研究进展[J].矿产综合利用,2021(1):23-31.
[32] 高洋,贵永亮,宋春燕,等.高钛高炉渣综合利用现状及展望[J].矿产综合利用,2019(1):6-10.
[33] WANG Z Y,ZHANG J L,LIU Z J,et al.Production of ferrotitanium alloy from titania slag based on aluminothermic reduction[J].Journal of Alloys and Compounds,2019,810:151969.
[34] WANG Z Y,ZHANG J L,ZHAO B J,et al.Extraction of titanium resources from the titanium-containing waste slag:Thermodynamic analysis and experimental verification[J].Calphad,2020,71:102211.
[35] WANG C,LEI Y,MA W H,et al.An approach for simultaneous treatments of diamond wire saw silicon kerf and Ti-bearing blast furnace slag[J].Journal of Hazardous Materials,2021,401:123446.
[36] LI Z C,LEI Y,MA W H,et al.An approach to prepare high-purity TiSi 2 for clean utilization of Ti-bearing blast furnace slag[J].Green Chemistry,2022,24(8):3344-3357.
[37] XUE T Y,WANG L N,QI T,et al.Decomposition kinetics of titanium slag in sodium hydroxide system[J].Hydrometallurgy,2009,95(1/2):22-27.
[38] MATSUURA H,YANG X,LI G Q,et al.Recycling of ironmaking and steelmaking slags in Japan and China[J].International Journal of Minerals,Metallurgy and Materials,2022,29(4):739-749.
相关链接